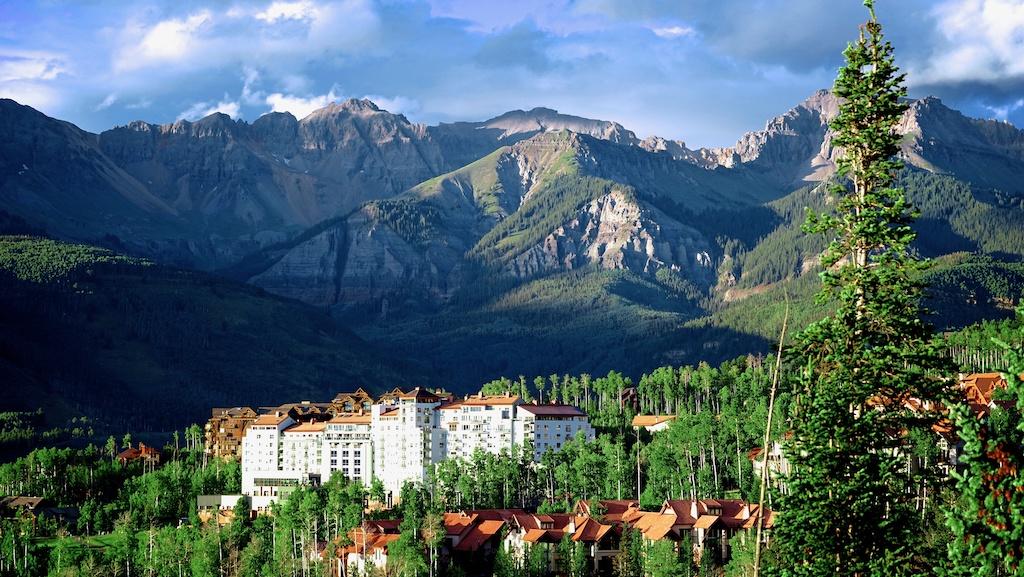
The combination of “hot and high” always has been a detriment to aircraft performance and safety. With excessively hot temperatures this summer, aircraft operators will have to take measures to reduce their negative effects on aircraft components and performance.
First, let’s quickly review the basics taught in ground school. When air heats up, it becomes less dense. Less-dense air means that the wing produces less lift, normally aspirated engines produce less power, and propellers produce less thrust. T o create sufficient lift, an aircraft needs to achieve a higher true airspeed. This all adds up to longer distances needed for takeoff acceleration as well as reduced climb performance. Both the rate and angle of climb will be reduced.
Density altitude is the pressure altitude corrected for non-standard temperature. Technically humidity also affects the density altitude. At sea level, the standard atmospheric pressure and temperature are 1013.2 millibars (29.92 in. Hg) and +15C. Under these conditions the density altitude and pressure altitude are the same. However, anytime the air temperature is warmer than standard, the density altitude will be higher than the pressure altitude. For example, let’s assume that you are maneuvering to land at Telluride Regional Airport (KTEX), Colorado, at 120 KIAS on a warm summer day in which the OAT is 85F. That equates to a density altitude of 12,570 ft. Your true airspeed is actually 145 KTAS in that thin air, which of course results in a longer landing distance.
This essentially sums up the material covered in standard ground schools on density altitude. This information might be sufficient for the operator of a light aircraft operating in flat terrain, but the operation of heavier and more complex equipment at a variety of airports requires more in-depth operational knowledge.
Let’s move on to a discussion more appropriate for the operation of turbine aircraft. Metal components in the hottest sections of turbine engines are exposed to extraordinary temperatures under normal operating conditions. Hotter-than-normal engine temperatures are likely when operating a turbine engine in hot conditions. If these turbine components are exposed to temperatures above established limits, irreversible damage may result. This can include cracks in turbine blades, which will lead to premature failure. It also can cause elongation of the blades, which then rub up against the casing. This unwanted friction will reduce engine rpm, and this in turn leads to less thrust and higher temperatures in critical sections of the turbine, which over time will reduce its reliability.
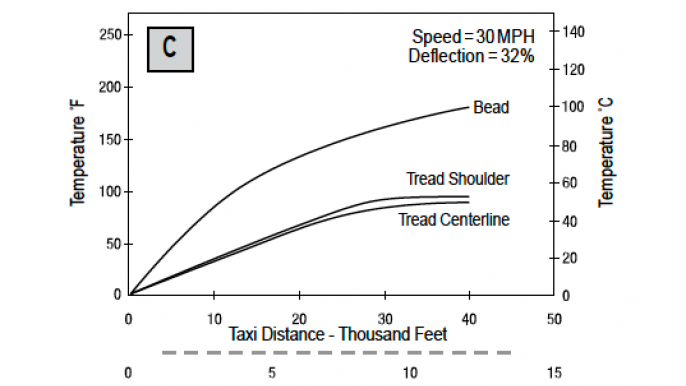
The engine manufacturers publish maximum temperatures to keep important engine components from being damaged by excessive heat, thus ensuring their reliability. Depending on the engine design, these temperature limitations may be specified in terms of the maximum turbine inlet temperature, interstage turbine temperature or exhaust gas temperature. These maximum temperatures will vary between engine types as well as phase of flight. The maximum takeoff temperature will often have a time limit. Under abnormally hot temperatures, the engine’s temperature limit will be reached well before the engine is producing its maximum rated thrust. For turboprop operations, this is often referred to as the engine “temping out” prior to its normal torque limit.
“Hot starts” are more likely in hot weather. Hot starts can occur because of insufficient air flow through the engine, often associated with insufficient acceleration of the turbine during the start sequence. For aircraft that utilize electrical power through a starter/generator for engine start, a hot start is likely caused by a weak battery. This can be prevented by using a ground power unit. For aircraft that utilize air pressure to turn the turbine, a hot start can be caused by insufficient air from the APU or the “huffer cart.” A tailwind blowing air in the reverse direction through the turbine will certainly inhibit the flow of sufficient air through the turbine as well. When possible, it is advisable to avoid tailwinds on hot days to reduce the chances of a hot start. Slower than normal acceleration of the engine rpm as well as an abnormally fast rise in the temperature are warning signs of a soon-to-occur temperature exceedance. If you manage to abort the start prior to exceeding a critical temperature, then the aircraft operating manual may allow a second start after allowing the starter to cool down. However, if the temperature limit is exceeded, maintenance action is required.
WAT Limit
There is an important paragraph buried far back in FAR Part 91 that carries important limitations for transport aircraft takeoffs, especially in hot weather. Part 91.605, “Transport Category Civil Airplane Weight Limits,” states “(b) No person may operate a turbine-engine-powered transport category airplane certificated after Sept. 30, 1958, contrary to the Airplane Flight Manual, or take off that airplane unless (1) The takeoff weight does not exceed the takeoff weight specified in the Airplane Flight Manual for the elevation of the airport and for the ambient temperature existing at the time of takeoff.”
This is often referred to as the “WAT” limit, short for weight, altitude and temperature limit. Perhaps you recall portions of the classroom discussion of the aircraft’s required performance during the various segments of the takeoff climb. The most restrictive of those climb segments is the second segment, which begins when the gear is retracted and the aircraft continues to climb with an engine inoperative with the flaps in the takeoff position at V2. For certification purposes the aircraft must climb at no less than a 2.4% gradient at that weight.
Part 91.605 is a link between the direct operation of the aircraft with the Part 25 certification standards. In practical terms, this means you cannot operate the aircraft outside of the certification limits. The maximum weight for any takeoff must assure that the aircraft still abides by these limits. For all practical purposes, this means that you must ensure that the weight of the aircraft for the takeoff at that altitude and temperature will allow a minimum second-segment climb gradient of 2.4%. Note that many other operational requirements, particularly obstacles in the takeoff flight path that require a steep climb gradient, are likely to restrict the takeoff to a lighter weight.
Let’s say that your aircraft performance charts extend as far as 49C, but as you taxi out at Phoenix Sky Harbor International Airport (KPHX) the ATIS reports the new temperature of 50C. It is tempting to reason that the temperature changed one mere degree to justify continuing your taxi to the runway. That reasoning can end up with a violation against your pilot certificate for operating outside of the certification limits of the aircraft. By the way, this is the very reason that some of the airlines are forced to stop flight operations at KPHX during exceptionally hot days in the summer.
As an interesting side note, there is a key word in the FAR title that has a significant meaning. That word is “Civil.” Public-use aircraft, such as those used for aerial firefighting, don’t have to comply with this limit.
Years ago, when I flew aerial firefighting aircraft the agency’s policy allowed operating with merely a 0.6% second-segment climb gradient. It was quite common to see our comrades in heavily laden, aging air tankers roll the entire length of the runway and barely rotate at the final length of the runway, struggling to stay airborne with all engines operating. The standard briefing among those flight crews was to immediately dump the heavy load of retardant if an engine failed during takeoff. We didn’t have that option with a load of elite smokejumpers on board, and a 0.6% second-segment climb gradient certainly wasn’t going to outclimb the steep terrain around smokejumper bases such as West Yellowstone.
Let’s put your aircraft at Eagle County Regional Airport (KEGE) in Colorado and you are planning to utilize the Gypsum Five departure procedure. Takeoffs are being conducted on Runway 25 with the daunting rise of terrain directly off the west end of the runway. The climb gradient requires 815 ft./nm to 9,200 ft. MSL, which equates to 13.5%. This requires an enormous reduction in weight to meet the climb gradient. The “weight penalty” is so excessive that operators who frequently fly into this destination have contracted with special engineering firms to custom-design procedures in case of engine failure, which will assure sufficient terrain and obstruction clearance while minimizing the weight penalty. For instance, one of the alternative designs specifies making a slight right turn in the event of an engine failure on takeoff and essentially flying down the canyon formed by the Colorado River. This requirement to have a sufficient climb gradient with an engine failure on takeoff is usually the most restrictive of all other performance limitations during the takeoff and climb phases.
Part 91.605 also specifies “(3) The takeoff weight does not exceed the weight shown in the Airplane Flight Manual to correspond with the minimum distances required for takeoff, considering the elevation of the airport, the runway to be used, the effective runway gradient, the ambient temperature and wind component at the time of takeoff, and, if operating limitations exist for the minimum distances required for takeoff from wet runways, the runway surface condition (dry or wet)….”
One of the inevitable problems for business aviation pilots is that clients show up late. If “Mr. Big Bucks” shows up late and the temps are 2-3C warmer, you really should recompute the aircraft’s performance. Technically speaking, this means your aircraft should comply with all of the various performance charts…accelerate-stop, accelerate-go and the climb gradient. If you are using charts to compute for your aircraft, this can be a lengthy process, especially if your aircraft has the infamous “spaghetti charts,” so named because of their size and complexity.
Those who utilize “airport analysis,” which is standard practice among the scheduled airlines, have a much easier process to quickly determine if their present weight meets all of the performance restrictions. The lengthy engineering work that goes into creating the data on the airport analysis assures that the aircraft will meet all of the required takeoff and climb restrictions when operating at the maximum weight for that temperature. It even includes easy-to-use adjustments at the bottom of the column in case of tailwinds or the necessity to use anti-ice.
Editor's note: Patrick Veillette's next feature will delve into more hot-weather operational issues.