
Nose view of the Hawker 800XP involved in a midair collision with a glider. No one is prepared to have the nose of their aircraft shattered in a microsecond and subsequently have another aircraft’s wing spar protruding through the instrument panel.
In our profession we have been trained to calmly and proficiently handle a wide variety of events that can occur without warning. But no one has ever been trained to have the wing spar of a glider crash through the instrument panel, spraying sharp debris, and rendering vision almost impossible from facial wounds and an insurmountable blast of 500 kts of air.
These were just a few of the challenges facing the pilots of a Raytheon Hawker 800XP that experienced a mid-air collision with a glider while on descent into Reno-Tahoe International Airport (RNO), Nevada, on Aug. 28, 2006. In a brief fraction of a second when the captain noticed a white glider filling her windscreen she grabbed the yoke and tried to turn away from the glider, but the impact at that immense speed was brutal.
The first officer heard an alarming “Whoomp” just as the instrument panel exploded before his eyes. In a microsecond all hell broke loose. The debris in the cockpit and the roar of noise were nothing they had ever experienced.
The captain reflexively determined to regain control of her stricken jet, but nothing in her training had prepared her for this situation. The instrument panel had been turned into tiny shards. In fact, the obliterated wires, glass, plastic and steel were now spilled over the yoke, actually constraining its movement.
Without instruments, not only did the pilots have no idea of critical flight information such as their airspeed, they had no other information to tell them the status of their engines, flaps and gear, all of which would be necessary for landing. They had no way of knowing that a large segment of the right wing was missing, or that one of engines was no longer functioning due to damage. A punctured fuel tank was rapidly causing a fuel imbalance, adding further to the abnormal flight characteristics of the normally docile Hawker.
The next minutes of their harrowing struggle in which they successfully landed the crippled jet at nearby Carson City airport illustrated supreme professionalism. The glider pilot bailed out and parachuted to the ground. He was faulted by the NTSB for not using his transponder.
There is no realistic training to prepare a pilot for an event such as this. Your chances of encountering a similar event are almost nil, and yet as pilots we need to be prepared to handle the many sudden surprises that occur in the real world. Not every surprise will be comparable to a mid-air collision. For fixed-wing pilots, events such as runway incursions, lightning and hail strikes, automation failures, and stalls can suddenly disrupt an otherwise routine flight and require immediate reaction. For helicopter crews, the list begins with a litany of components in the flight control system that can suddenly fail, loss of tail rotor control or Vortex Ring State.
It is worth examining the important lessons reinforced by the actions of the Hawker crew and others who have dealt successfully with surprise events, as well as examining the limitations of human performance and information processing when confronted with surprise. The historical record also includes examples of flight crews who have been unsuccessful when confronted with surprise, and those tragedies contain equally important lessons.
Simulator Responses Can Be Very Different
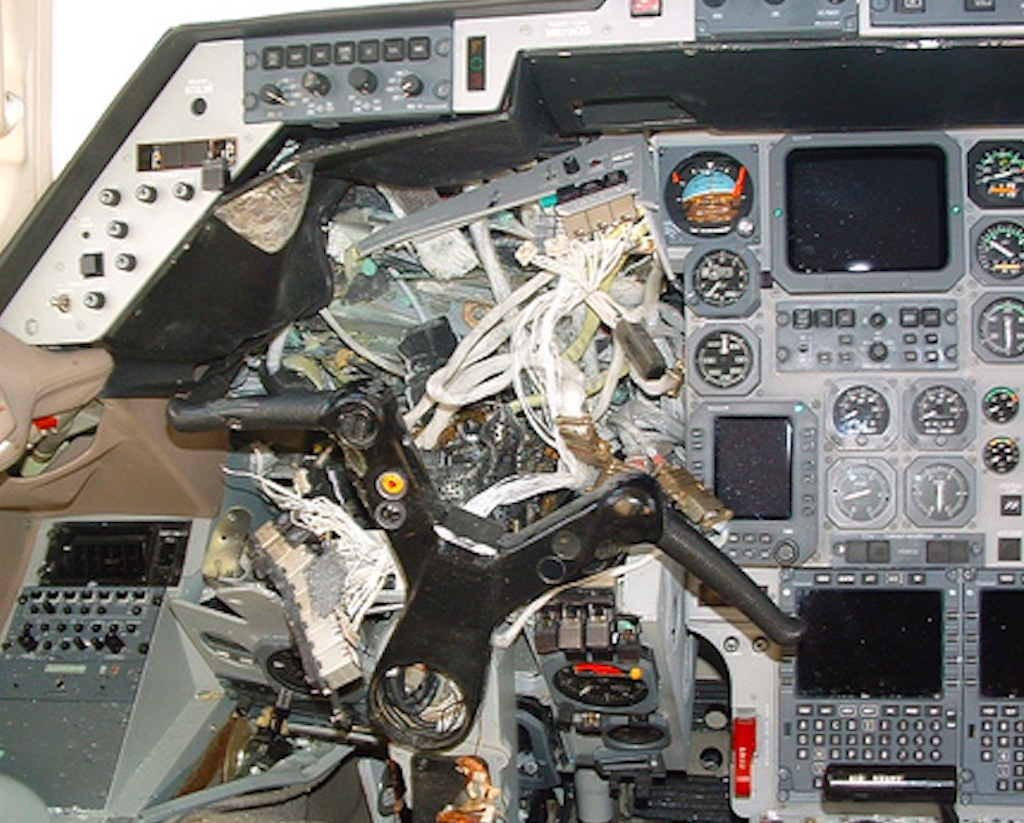
Prof. David Woods of The Ohio State University Department of Integrated Systems Engineering has researched complex human-machine systems for over 40 years and notes that a pilot’s response in a simulator can be very different to comparable events in the real world. Specifically, pilots tend to respond to an abnormal situation faster in the simulator, thus a 5-to-10 sec. response in the simulator might even double in the real world
This correlates with the digital flight data recorder pilot reaction times from eight real-world rejected takeoff (RTO) incidents that showed a range of 4.1 to 9.2 sec., with an average of 6.5 sec. Boeing engineers analyzed 69 rejected takeoffs documented in a special NTSB study, “Runway Overruns Following High Speed Rejected Takeoffs,” and noted that the crew had incorrectly interpreted the cause of the RTO in 53.8% of the 69 rejected takeoff events.
Human Factors Engineering, a textbook written by several notable human factors researchers, cites a large body of research on human detection and reaction to complex problems, and the rejected takeoff problem exactly fits the definition of a “complex problem.” The difficulty and speed of selecting a response or reaction are influenced by several variables. Three of the variables are particularly critical in the RTO problem. These are decision complexity, expectancy, and speed-accuracy tradeoff.
While our takeoff Go/No-Go performance numbers are primarily based upon the engine-failure scenario, there are many other maladies that can afflict an aircraft and make it un-airworthy for flight. A high-speed tire failure can cause stimuli that pilots have never experienced before. The complexity of the Go/No-Go decision for a tire failure exceeds the simple decision in the accelerate-stop criteria currently used in RTO certification that is reinforced the many times a pilot returns for recurrent simulator training.
Christopher Wickens, former head of the Human Factors Division at the University of Illinois Urbana-Champaign, and author of Engineering Psychology and Human Performance, found a very definable relationship between response-time and error-rate. In other words, there is a trade-off between speed and accuracy. When pilots scan the instrument panels rapidly because of time pressure, the accuracy of a pilot’s perception will suffer and the probability of error will increase.
This was illustrated by the crash of TransAsia Airways Flight 235, an ATR 72-600, on Feb. 4, 2015, during its initial takeoff from Taipei. Shortly after takeoff, a fault in the autofeather system on the right engine caused it to autofeather the engine. The flight crew misdiagnosed the problem and shut down the fully functioning left engine, resulting in a loss of control and crash into the Keelung River. Forty-eight of the 58 people on board were killed.
Our industry learned many decades ago that reaching up to make changes to throttles and fuel levers during an engine failure on takeoff was prone for mistakes. Thus, the industry standard cemented the concept that other than maintaining aircraft control, a flight crew would take no actions during an engine failure on takeoff until attaining a safe altitude and only then going through a deliberate, methodical process before any knob or lever was moved.
As we explain in Part 2 of this article, the slightest abnormality in the aircraft’s performance or handling during a takeoff in the simulator is quickly interpreted as an engine failure, but the real world may have other surprises.