
Man was intended to fly like a bird — not like a bat out of hell,” is an aphorism attributed to Lawrence Bell, founder of the eponymous rotary-wing manufacturer and, with inventor and polymath Arthur Young, developer of the first civil-certificated helicopter, the iconic Model 47.
Regardless of the statement’s provenance, the sentiment accurately conveys the age-old human dream of being able to rise vertically from the ground and then fly through the air — like a bird. The helicopter, of course, satisfies the vertical-takeoff half of Bell’s alleged dictum, but to go anywhere must thrash through the air, “beating it into submission,” as rotary-wing pilots like to joke. As a result, rotary-wing craft are limited in speed and range and generally confined to lower altitudes.
A Tiltrotor Legacy
As early as the 1950s, Bell began exploring the possibility of combining vertical capability with fixed-wing flight with the XV-3. One of the world’s early tiltrotor experiments, the aircraft featured twin wingtip-mounted helicopter-like rotors driven through shafts by a radial engine installed in the fuselage. While dogged by persistent rotor instability (specifically, a variation on whorl mode), the XV-3 nevertheless logged more than 100 hr. flown by Bell and U.S. Air Force pilots, thus proving the viability of the tiltrotor concept.
The XV-3 provided a knowledge base that two decades later led to Bell’s development of the NASA-funded XV-15, a fully functional tiltrotor design that established the practical operating envelope for combined rotary- and fixed-wing flight. Featuring unique proprotors characterized by severely twisted, wide-chord blades and pivoting wingtip-mounted engines, the XV-15 laid the groundwork for definition of the JVX tactical transport program in 1981 that culminated in development of the V-22 Osprey tiltrotor for the U.S. Marine Corps, Air Force and Navy. A prototype of the aircraft flew for the first time in 1989, commencing a nearly 20-year refinement program marred by several accidents and consequent setbacks. The MV-22 officially entered service with the Marines in 2007.
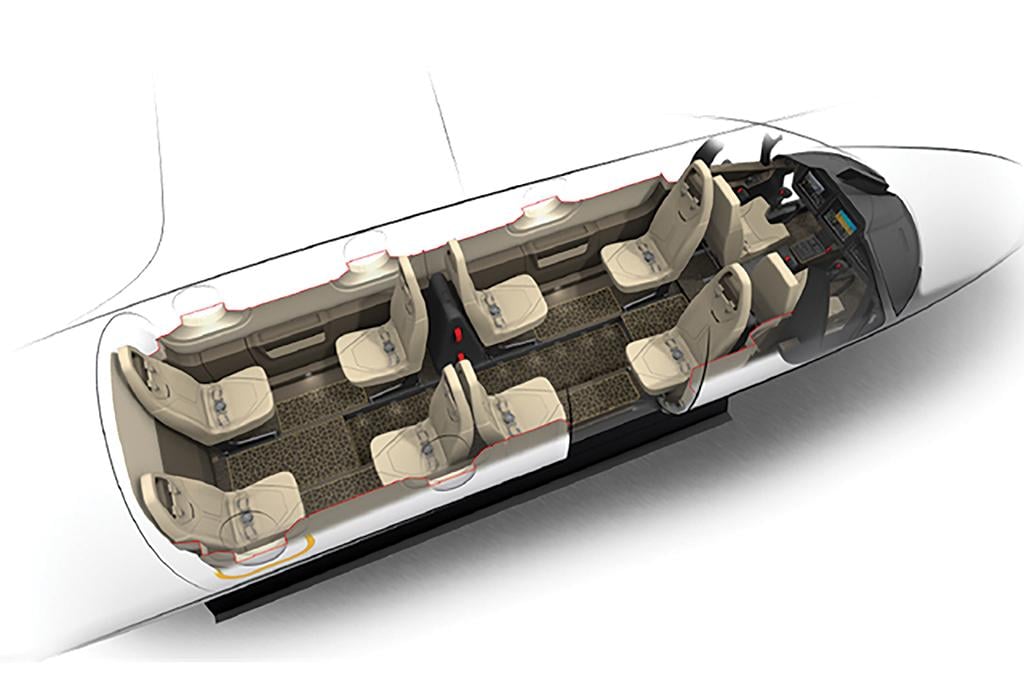


In conceptualizing and developing the V-22, Bell partnered with Boeing Helicopters, and in the mid-1990s, the two began discussing the possibility of teaming up to build a commercial tiltrotor. This resulted in the BB609, which was conceived as a nine-passenger, two-pilot aircraft and was more like the XV-15 in size and performance than the V-22. Following its merger with McDonnell Douglas, Boeing exited the commercial helicopter business in 1998 to focus on the military rotorcraft market with the CH-47 Chinook, AH-64 Apache and other products.
Meanwhile, Bell, which had a long history of licensing partnerships with Agusta Westland, teamed up with the Italian manufacturer to continue the 609 program, redesignated BA609. This arrangement continued until late 2011, when Agusta bought out Bell’s share, and the aircraft’s designation was again changed, this time to AW609. Subsequently, in the consolidation of Italy’s aviation industry, Agusta Westland was absorbed into Leonardo, a conglomerate that encompasses rotary- and fixed-wing aircraft, aerostructures, electronics and cybersecurity. “This is now a 100% Leonardo program,” William Sunick, head of tiltrotor marketing at Leonardo Helicopters, recently told BCA.
The AW609 is the distillation of thousands of hours of engineering, innovation, testing and refinement, and touched with tragedy. The program has been in progress for nearly 25 years and has yet to achieve certification, although with the fourth prototype now flying at Leonardo’s U.S. headquarters and factory in Philadelphia — where the AW609 will be produced — that prize is in sight and perhaps soon.
Tiltrotor Tech Is Mature
As Sunick points out, tiltrotor technology is well accepted and mature, with more than 500,000 hr. of operational experience, most of it by the V-22 in military and combat ops with the Marines and Air Force; Navy aircraft will begin carrier-on-board (COD) deliveries next year with the CMV-22V variant. Total hours logged in the AW609 testing program stood at 1,600 at the beginning of this year. In addition, thousands of hours of ground testing preceded flight. In Italy, a “run stand” was built on which prototypes are secured so that nacelles can be rotated and dynamic systems tested. Engineering simulators have been installed in Italy and Philadelphia for software development and avionics and actuator testing.
The fourth prototype, built in Philadelphia in production configuration, made its first flight Dec. 21; its first assignment is inflight testing of the Collins Fusion avionics suite that equips the AW609 line. It joins a second machine at Philadelphia currently engaged in aeroelastic stability and engine testing. Meanwhile, an earlier prototype is back on the run stand in Italy for further research purposes. Another prototype was destroyed in a 2015 inflight accident in Italy. In January, the first two customer aircraft were in production at the Philadelphia plant, destined for launch customer Era Aviation.

Given that tiltrotor technology was well along when the AW609 was conceived, why did it take so long for the program to reach its present state? “When we acquired the program,” Sunick explained, “we took a critical eye on where the program was in development within the context of both emerging technologies and the capability we wanted the AW609 to have at certification. So [in 2012] we embarked on a whole new development program to incorporate the latest technologies.”
As a result, the aircraft is “much changed.” This includes:
- An aerodynamic cleanup reducing drag by 10%, based on flight testing and wind-tunnel analysis.
- An engine upgrade to the Pratt & Whitney Canada PT6C-67A turboshaft rated at 1,940 shp for normal operation and 2,492 shp for 30 sec. under one-engine-inoperative (OEI) conditions.
- MTOW increased to 18,000 lb. from 16,799 lb. Useful load is 6,000 lb.
- Structural changes, including a beefed-up retractable landing gear to accommodate the higher gross weight.
- A new, wider cabin door. Measuring 35-in. wide and 50-in. high, it is a clamshell-type design, à la the Learjet 25/35, with segments hinged at the top and bottom, replacing the original, smaller door that was hinged on one side. The upper segment of the door is claimed to be sufficiently robust to serve as a mounting point for a hoist for a proposed search-and-rescue (SAR) version of the aircraft.
- A redesigned cockpit based on addition of the Collins Fusion suite.
- A new air data system.
- An upgraded flight control computer (FCC).
- A new environmental control system (ECS).
The last four improvements on the list are said to reduce pilot workload, and the new prototype/demonstrator at Philadelphia incorporates all of them. “All this results in a robust capability and is cutting edge,” Sunick proclaimed.
There is a popular misconception that the AW609 was spun off from the V-22 and is a scaled-down version of the military tiltrotor. Nothing could be further from the truth, Sunick insisted. “The tiltrotor concept and technology is shared with the V-22, but this is a commercial aircraft designed to FAA transport category aircraft standards, FAR Parts 25 and 29.” In addition, the FAA has conceived a whole new category to accommodate tiltrotors called “powered lift” — so far unnumbered and expressed simply as “Part TR.”
Optimized for Comfort
Also, unlike the spartan military V-22, the AW609 is “optimized for passenger safety and comfort,” Sunick said. So again, unlike the V-22, its cabin is soundproofed and pressurized to the aircraft’s 25,000-ft. ceiling.
Further, in the unlikely event both of the tiltrotor’s PT6C-67A engines were to fail, the AW609 can perform autorotational landings, since its proprotors generate much lower disk loading than those of the V-22, and, thus, the aircraft behaves more like a helicopter.
In a 2009 test of a dual engine failure, an AW609 prototype’s pilots were able to carry out a successful and safe autorotational landing from cruising altitude. Five years later, Leonardo pilots performed more than 79 power-off conversions from airplane to helicopter mode during autorotation tests monitored by the FAA, concluding that minimum altitude for a successful autorotation is 3,000 ft. and that, if the maneuver is conducted properly, the AW609 can easily maintain rotor rpm above 70%, the minimum for stable recovery.

The procedure is straightforward: Glide to windmill the proprotors; institute “a rapid conversion” to helicopter mode with an airflow inversion with respect to the proprotors; begin the autorotation with descent airflow keeping the proprotors turning; finally, time flare before touchdown.
Technically, the 30,000-lb. V-22 can autorotate if both of its Rolls-Royce/Allison turboshafts were to fail. However, due to the aircraft’s relatively high rotor-disk loading, safe autorotational landings are deemed to be “extremely difficult.” In order to meet a shipboard requirement of folding rotors for below-deck storage, the aircraft’s proprotors had to be truncated by 5 ft. to a 38-ft. span from a size considered optimal for vertical flight, resulting in the high disk loading. During the proving phase of V-22 development, the Pentagon testing directorate pronounced that an attempt to autorotate the aircraft below a 1,600-ft. hover would likely be un-survivable.
Emphasizing the AW609’s broad capabilities beyond vertical flight — speed, range, high-altitude cruise avoiding weather — Sunick pointed out that “about 85% of the time the 609 is flying, it will be in the airplane mode, depending on the mission. For example, it may go somewhere and hover, as in the SAR application, then return in the fixed-wing mode. So there would be a takeoff and landing and a mid-point hover for a rescue that will involve vertical lift.”
Operating under transport category rules, the AW609 can take off vertically at 16,800 lb. (the aircraft’s previous MTOW). Leonardo plans to establish vertical takeoff weight in the normal category this year and expects it to be higher. The AW609 is capable of short takeoff and landing (STOL) performance when the nacelles and proprotors are lowered from the vertical to a diagonal position to facilitate a rolling takeoff. (Nacelle angle is at pilot’s discretion but in the neighborhood of 75 deg.) “This will result in less wear and tear on the dynamic systems,” Sunick said. It also makes takeoff at the new 18,000-lb. MTOW possible. Run-on landings are also possible with the nacelles set at the appropriate tilt angle.
In the full helicopter mode (nacelles vertical), the AW609 can hover out of ground effect (HOGE) at 6,000 ft. and in ground effect (HIGE) at 10,000 ft., both under ISA conditions.
The load-bearing nacelles’ full extent of tilt is 95 deg. vertically to 0 deg. horizontally. For takeoff and hovering, the pilots will choose the optimal slant depending on various factors including weather and space constraints, usually between 87 and 90 deg. However, it is also possible to pivot the nacelles 5 deg. aft (i.e., to the full 95-deg. vertical extent) for braking or rearward flight. For forward flight, nacelles are automatically locked in the 0-deg. position. Conversion is facilitated hydraulically by dual telescopic ballscrews. Hovering, flaperons are automatically dropped to 66 deg. to reduce wing area from the proprotor downwash.
Diameter of the three-blade proprotors is 25 ft., 11 in. Blades are twisted 40 deg., distinguishing them from the flatter rotorblades of conventional helicopters. “By nature it is a compromise design between a rotor and a propeller,” Sunick observed, “and walks a fine line between them.”
Another difference is that a helicopter rotor is designed to operate in one plane of rotation, and the proprotors must function as both helicopter rotors and airplane propellers in planes 90 deg. apart. In the combined rotary- and fixed-wing modes, the blades exercise a fairly broad collective “excursion” of 0-60-deg. pitch. The blades are fabricated of mainly carbon fiber; their useful life is being determined by Leonardo’s maintenance review board.
With the nacelles mounted at the wingtips, the proprotors are more than 15 ft. from the cabin for “enhanced ride quality.” Also, with the AW609 on the ramp and the nacelles in the vertical position, the proprotors, when turning, are more than 15 ft. above the ground for safe movement of passengers or ramp personnel.
The AW609’s 32-ft., 10-in.-span wing (measured between proprotor centers) is slightly swept forward and fabricated of carbon fiber. It holds the AW609’s entire 2,571 lb. of fuel load, distributed among 10 crashworthy cells. In terms of range, this gets the aircraft — as expressed by Sunick — “700 nm to dry tanks under ISA conditions with no payload.” (Apparently, neither the FAA nor NBAA IFR range calculations have yet been worked out by the developer’s engineering test pilots.) Duration is listed as 3 hr. at maximum cruise speed of 275 kt. In 2015, one of the AW609 prototypes was flown 721 sm (626 nm) from Yeovil in the UK to Milan in 2:18 hr.
Leonardo is working on auxiliary fuel tanks that would be externally mounted under the wings, inboard of the nacelles, adding approximately 900 lb. of additional fuel, which would extend range under the same conditions to 1,000 nm. “They look like military drop tanks but are fixed,” Sunick said.
Lots of Moving Parts
Much of the AW609’s mechanical complexity is contained in the wing and nacelles. In addition to the power transfer shaft in the wing that connects the engines, enabling the operating turboshaft in an OEI situation to drive both proprotors, there is a mid-wing gearbox for the transfer shaft to get it “around the corner” at the apex of wing’s sweep. (The shaft is similar to the driveshaft that runs from the main rotor gearbox to the tail rotor in a conventional helicopter and so is well-established technology.) Additionally, two tilt-axis gearboxes for moving the nacelles plus a pair of proprotor reduction gearboxes are contained in the nacelles. That’s five gearboxes in all.

The empennage of the AW609 consists of a T-mounted horizontal stabilizer and elevator atop a vertical stabilizer that does not include a rudder. The aircraft is turned in the airplane mode using flaperons and “differential collective” (more on that later).
The aircraft has designed-in proprotor anti-ice and deice capability and is fitted with wing and engine inlet deicing boots and a heated windshield for eventual approval of flight into known icing conditions. Leonardo has tested the airframe with ice forms in flight to determine the effect of icing on the unprotected empennage.
Obviously, hydraulics are an essential component of the tiltrotor, to (among other functions) precisely rotate the nacelles under heavy dynamic loading, so the AW609 is equipped with a triplex (i.e., triply redundant) 3,000-psi hydraulic system. To meet electrical needs, three DC generators, two AC generators and a 28Ah battery are standard. The flight control computer is also backed up with two dedicated batteries. Vapor-cycle air-conditioning augments the cabin pressurization system. The aircraft, at least at present, is not equipped with an APU.
The fly-by-wire (FBW) control system is also triply redundant. “BAe Systems developed the FBW hardware and Leonardo wrote the software code in-house,” Sunick noted. Considering that it must govern both rotary- and fixed-wing operation and the transition between the two modes, the software must be among the most complex in civil aviation, and it makes flying the AW609 possible with a claimed minimum of pilot workload. “We are constantly updating it,” Sunick said, “just like your iPhone.” It is programmed to, in certain cases, “not let you do things,” he offered. However, note that this is not exactly like some FBW code in other aircraft that will not allow the aircraft to diverge from the established flight envelope.
One reason why it took so long to develop and perfect the tiltrotor concept is establishing the dynamics and control laws necessary to enable the conversion from vertical to horizontal flight in a seamless and safe manner. According to a Leonardo briefing document, “Flight controls from VTOL conversion to airplane mode are transparent, phased with nacelle tilt angle.”
Thanks to flight-control system augmentation, constant altitude during the conversion can be maintained (i.e., with no dip in altitude for translational lift) with low pilot workload as a byproduct. Consider that transition must be made starting from a condition where nacelles are vertical and lift is produced in a hover, to a lowering of the nacelles to about 75 deg. where forward speed builds to 60-80 kt., and lift is gradually transferred to the wing. As the aircraft continues to accelerate to about 160 kt., the wing becomes fully loaded, and conversion to airplane mode is complete.
According to Sunick, the Collins Fusion avionics are “pretty much unchanged from what you’d find in a typical business jet other than incorporating a nacelle position indicator.”
The suite features three large-format displays with touch-screen interfaces. A sink-rate warning system is also included to maximize allowable descent rates at slow forward speeds with a safety margin to avoid vortex ring state. (See “VRS and Other Controversies” sidebar.) The cockpit is designed for single-pilot IFR operation, although it is likely that in most roles such as in business aviation or offshore transport, two pilots will crew the aircraft.
While many of the functions in the AW609’s operation are automated via the FCC and its software algorithms, cockpit controls are designed to replicate those of conventional rotary-wing aircraft to ease transition of pilots into the dual-role tiltrotor. A collective stick is mounted on the left side of the pilot seats — in the AW609, it is called the “power lever” and is equipped with a thumb wheel to change the nacelle positions — with a cyclic stick facing the pilot that doubles as a “joystick” in the airplane mode.
How Does It Fly?
So, from a pilot’s perspective, how does the AW609 fly in either mode? The beauty of the FCC software is that it replicates the characteristics of each type of aircraft implicit in the hybridized aerial vehicle.
“As a helicopter, we programmed the fly-by-wire software so it flies in a similar fashion to the Leonardo AW139 midsize helicopter,” Sunick said. “This modeled the behavior. In the airplane mode, we wanted it to behave like a twin-engine turboprop, so it is modeled like one of those — for example, the Beech King Air 250.
By design we had to make it easy and intuitive for both kinds of pilots to fly.

“It doesn’t have a rudder, so when in airplane mode, we use differential collective — the yaw effect — to turn,” he continued. “Differential collective and flaperons enable the coordinated turn — all managed by the FCC. From the pilot’s perspective, though, nothing has changed. The flight-control computer takes the pilot’s input and moves the proper control surface to get the desired result. The AW609 can autorotate, and you have maximum compatibility so a conventional helicopter pilot would feel no difference in how it handles. Same for fixed-wing pilots.”
In what configuration would a crew fly an IFR approach in the AW609? “Easy,” said Sunick: “You transition to rotary-wing to fly the relevant IFR approach. This offers greatly reduced speed for maneuvering, unlike a fixed-wing aircraft.” (How this will come down with air traffic controllers at high-density airports under pressure to get as much traffic on the ground as quickly as possible remains to be seen.)
Vne (never exceed speed) is 283 KTAS at the aircraft’s ceiling of 25,000 ft. In the 2015 mishap in Italy that occurred during dive tests, the country’s accident investigation board, Agenzia Nazionale per la Sicurezza del Volo (ANSV), determined the test aircraft achieved a maximum airspeed of 306 kt. before uncontrollable oscillations (similar to Dutch roll) forced the proprotors to deform and strike the leading edges of the wings, severing fuel and hydraulic lines and culminating in an inflight breakup. Test pilots Herb Moran and Pietro Venanzi died in the crash.

ANSV also concluded that neither the control laws programmed into the FCC nor the project’s engineering simulator could predict the possibility for the oscillations and the ensuing event that destroyed the aircraft. As the investigation report stated, “Therefore, the [simulator] was not really able to properly carry out the role as test bench for the control laws and risk reduction.”
Leonardo declined to comment on the accident for this report, pending litigation. But one visual result of the mishap was a redesign of the AW609’s vertical stabilizer and the tail end of the fuselage (the difference can be noted in before-and-after-2015 photographs of the aircraft). And it would make sense for Leonardo to reprogram the engineering simulator to provide cues of an incipient Dutch roll condition when maneuvering at high speed.
Unanswered Questions
The AW609 is constructed primarily of carbon-fiber composite skins and aluminum frames, mechanically fastened. As noted, final assembly will take place in the Philadelphia plant from subassemblies made in Italy. Composites are fabricated in Leonardo’s Brindisi, Italy, works. (Leonardo’s rotary-wing division is headquartered in Milan, while the corporate headquarters is in Rome.)

Maintenance, or how the immensely complex AW609 will be inspected, maintained and overhauled, is yet to be determined. According to Sunick, Leonardo’s Maintenance Review Board is working out inspection intervals. Given its mechanical complexity, the tiltrotor’s maintenance costs will likely exceed those of comparable helicopters and turboprop airplanes.
Also in abeyance is pilot certification for the crossbred tiltrotor category of aircraft. “We are still defining pilot licensing,” Sunick said, “and discussing with the FAA the requirements, number of hours, and so forth. Certified helicopter pilots will need to obtain fixed-wing qualifications, and vice versa.” It would seem that the unique nature of the tiltrotor would require an equally unique pilot certificate.
Which brings up the subject of training. This summer at Leonardo’s Philadelphia Training Academy, the manufacturer will commission a “full-flight” six-axis motion-base Level D simulator to be built by Canada’s CAE and able to interchange between Leonardo’s AW139 and AW609 rotary-wing products. Jointly developed by Leonardo and CAE and based on the latter’s 3000 series, the simulator will be managed by Rotorsim, a joint venture between the two companies. The simulator is complemented by an AW609 procedures trainer featuring panels from the actual aircraft as well as other devices designed to prepare students for its operation.
Meanwhile, FAA and EASA reciprocal type certification of the AW609 awaits. “We can’t provide a date, but we are laser-focused on certification,” Sunick said. With the production prototype now flying at Philadelphia and some 25 years of engineering, development, millions of dollars and blood behind it, one might speculate that 2020 will be the year that a civil tiltrotor will receive production approval.
Other questions waiting to be answered are the AW609’s unit price, operating cost and number of orders Leonardo has accepted for production aircraft.
Concerning the first, Leonardo executives decline to reveal a range of purchase prices for AW609s or an average. At the beginning of the century, when the project was approximately five years old, price numbers between $8 million and $10 million were touted by the then developers. More recently, speculation holds that price may have escalated to as high as $30 million.
Whether the utility of the tiltrotor can offset such a unit price remains
to be seen. The company has said only that “The AW609’s price has not yet been set, though from a total operating cost perspective, the AW609’s point-to-point capability will be very competitive with legacy mixed-fleet transportation options.”
Leonardo is holding its operating-cost cards close to its corporate chest. However, given the high cost of operating helicopters, the dual personality of the AW609 and the consequent complexity of the tiltrotor, one can assume the aircraft’s DOCs will go even higher.
As for orders, Leonardo is equally mum. Early in the program — that is, when Bill Clinton was still president — orders totaled in the 70s. As program ownership changed hands and development dragged on, projective purchasers canceled their delivery positions and the order book thinned.
Leonardo has lofted several configurations for the AW609. These include:
- Utility/offshore, nine passengers, two crew.
- Search and rescue (SAR), up to four attendants, one-two litters.
- Emergency medical service (EMS), up to four attendants, one-two litters.
- Corporate shuttle, eight passengers, two crew.
- VIP/business aviation, six passengers, two crew and an option for a lavatory.
Whether the AW609 will find acceptance by business aviation remains to be seen. For flight departments with a need to service a corporate territory with a 700-nm radius and a paucity of airports, it could offer a solution. As could the ability to operate from an urban heliport or rooftop pad, an attractive convenience for the time-driven executive in an environment where surface transportation is abysmally restrictive.
While the AW609 offers new levels of flexibility to a variety of applications, it remains to be seen if the market is ready for this unusual aircraft.