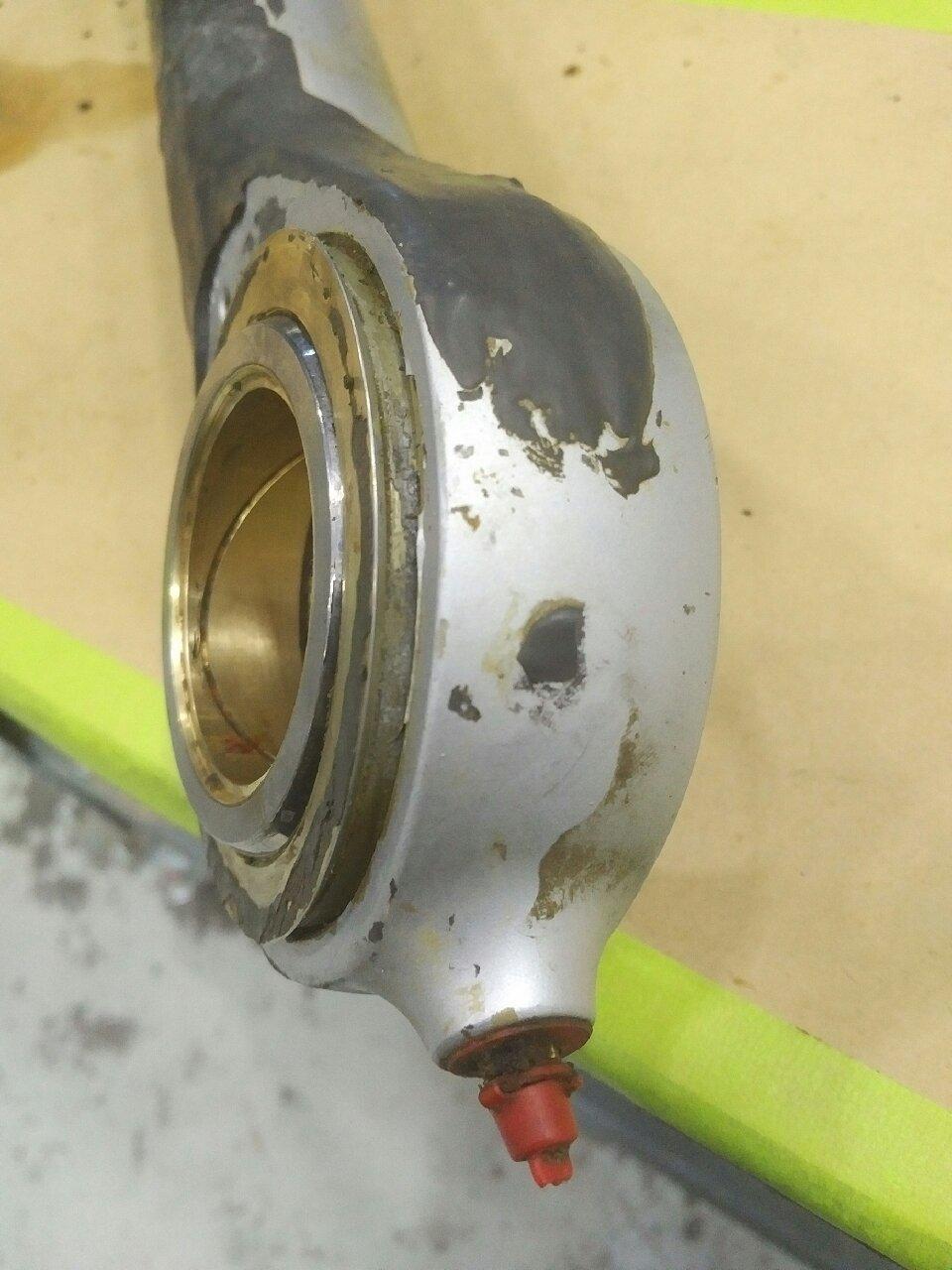
Editor's note: This is the first of a three-part article series.
Our aircraft have a multitude of components in which some movement is completely normal, and under specific circumstances, they create perceptible noises and vibrations. An example would be the lowering of flaps, spoilers and landing gear.
On the other hand, should you be worried if you sense subtle airframe vibrations while in a descent that seem out of the ordinary? Yes. It is important for a pilot to be able to distinguish what is a normal and acceptable aircraft vibration versus vibrations that aren’t normal. It is equally important that pilots know what proper actions should be taken to lessen unwanted vibrations, as well as providing accurate details so maintenance technicians can begin an efficient process of troubleshooting possible sources of the vibration.
Can vibrations compromise the safety of an aircraft, and if so, how? The answer to the first question is a resounding yes, as the following examples exhibit. If engineers did not purposely design a component of the aircraft to withstand an acceptable amount of vibration, the excessive movement will cause accelerated wear. If this happens to a critical aircraft component and the failure occurs in flight, this could quickly create a safety problem. At the very least, the accelerated wear will necessitate inspection and likely replacement of the worn component.
Flight Control Free-Play
In general, “cable and pulley” flight control systems are more susceptible to vibrations than hydraulically driven flight controls due to the inherent resistance that hydraulic servos provide against a flight control’s pressures. The interplay between separated airflow behind a Mach wave at transonic speeds and an aileron can cause unwanted aileron buzz (small vibrations). On conventional “cable and pulley” flight control systems, this tendency of aileron buzz, especially at transonic speeds, is heightened if there is any looseness in the cables, pulleys or bushings.
The FAA received reports of wing/aileron oscillations from operators of Hawker 800XP and 850XP aircraft at altitudes above 33,000 ft. and speeds over Mach 0.73. When the speed was reduced and the airplane was at an altitude below 30,000 ft., the oscillations ceased.
Investigation of the incidents revealed missing aileron bushings, low cable tensions and improperly installed brackets. If the aileron system, including cable tension, is not properly maintained, wing oscillations could develop into divergent flutter, causing severe damage to the structure. When corrective maintenance brought the aircraft into compliance with the type design configuration, the oscillations did not recur.
These oscillations can reduce the fatigue life of the aircraft, and in severe cases, can adversely affect the wing structure by causing cracks in the wing spars and stiffeners. Thus, the FAA issued Special Airworthiness Information Bulletin NM-14-05 dated Nov. 27, 2013, recommending a one-time maintenance check to verify all the bushing in the aileron and aileron tab assemblies are correctly installed and that the free play is within limits, and to ensure that the hinge brackets are properly installed and the cable tensions are correct.
While preflightight cable-driven flight controls, pilots should check the free play by gently moving the flight control to determine the slack. The exact amount of free play (i.e., the amount you can jiggle the flight control without restriction) should be stipulated in the aircraft maintenance manual. If excessive free play is found during a preflight, the proper action is to note the discrepancy in the aircraft logbook and not fly the aircraft until the condition is corrected by maintenance technicians.
Challenges With Control
The flight crew of a Canadair CL-600-2B19, operated by Atlantic Southeast Airlines as Flight 4690, took off on May 8, 2003, from Atlanta en route to Montreal. After doing so, the flight crew sensed a high-frequency vibration with their feet as well as from the flight control column. They glanced at the engine indicating and crew alerting system (EICAS) to see if there were any warning indications from a system on the aircraft to help them ascertain the source of the vibrations, but the EICAS screen remained blank. When the airspeed was increased to 250 kt., the vibrations started again. Initially, the vibrations were slow, but they increased in intensity and lasted about 30 sec. As the flight was cleared to 17,000 ft., the aircraft started an uncommanded 45-deg. roll to the right. The first officer (who was the pilot flying for this leg) immediately disconnected the autopilot and was able to regain control, albeit with difficulty due to the continuing tendency to roll to the right. The captain declared an emergency and ATC issued a clearance to Chattanooga, Tennessee. The pilots continued to sense the vibrations throughout the remainder of the flight at all airspeeds. The flight was successfully landed at Chattanooga without any injuries to the flight crew, flight attendant and 18 passengers.
When the NTSB’s systems group began its post-incident inspection, the team members discovered hand movement of the right-aileron control surface allowed free play with the hydraulic systems turned off. The extent of free play was measured at 0.4375 in. In contrast, the left aileron exhibited 0.25 in. of movement. Examination of the components by the NTSB’s materials laboratory revealed wear and polishing on many of the fraying surfaces. Wear locations included the outer diameters of the bolts, both diameters of the bushings, and balls and sockets of the links.
The NTSB determined the probable cause to be excessive wear on the bushings and the right aileron’s inboard and outboard power control unit, which resulted in upward movement of the right aileron. This directly led to the aircraft’s uncommanded right roll. A factor was the inadequate maintenance inspection procedure by the aircraft manufacturer for the aileron system’s check performed by the operator.
In Part 2, we’ll discuss getting the aircraft safely back to the ground when it exhibits unusual vibrations.