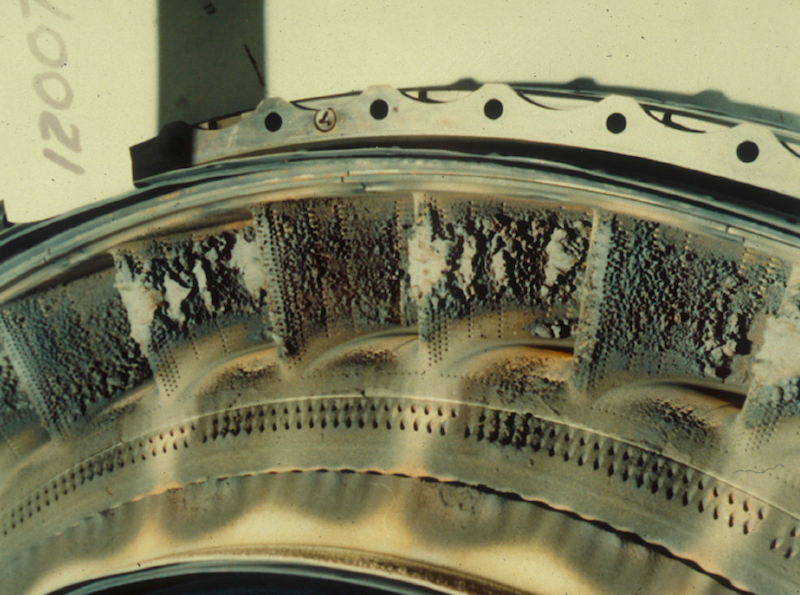
Widespread damage occurred in the hot sections of a KLM Boeing 747 that encountered volcanic ash from Alaska’s Mount Redoubt in December 1989.
A higher exhaust gas temperature (EGT) to produce the same amount of thrust will result any time that bleed air is extracted from an engine, particularly with the utilization of air conditioning packs and anti-ice.
If the conditions for a takeoff place a high demand on engine performance, one method to reduce the engine’s temperatures is to take off with the packs off, with the caveat that this method can only be done on aircraft that have been certified for this. Taking off with the APU on to provide air conditioning flow is a consideration to remove the bleed air demand from the engines.
Accurate observations are important to help maintenance technicians properly diagnose and resolve mechanical malfunctions leading to abnormally high engine temperatures. An interesting example is provided by a maintenance supervisor involved with an airframe that had recurring write-ups for an engine over-temping on takeoff. The maintenance technicians were unable to duplicate the over-temperatures during ground run-ups. It wasn’t until a non-routine flight operations pilot noticed that the engine temperature began to quickly spike seconds after lifting off that the troubleshooting process focused on the role of “something” changing in the engine once the squat switches were no longer compressed by the aircraft’s weight on the wheels.
It was discovered that the bleed air valve was opening too wide upon liftoff, allowing a major portion of the air to be vented into the bleed air system. This troubleshooting process took months and incurred several over-temp events on takeoff before the problem was corrected.
Harsh Operating Environments
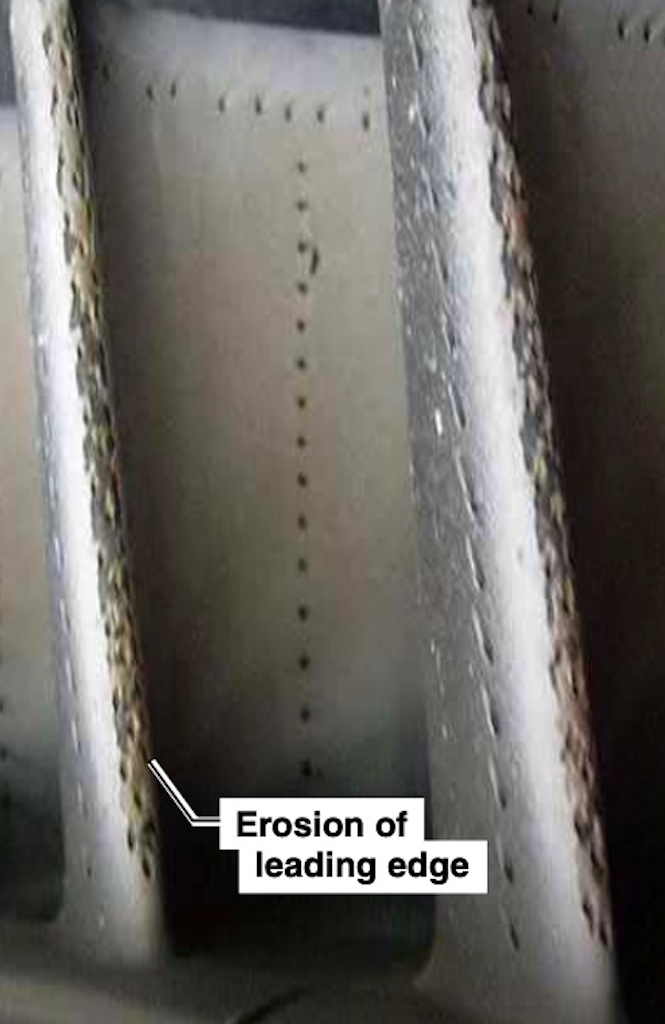
Turbine engines were originally designed to operate in a clear and dry air environment, but the airborne environment is often composed of elements other than the normal mixture of 78% nitrogen, 21% oxygen, and sparse amounts of carbon dioxide and hydrogen. In reality, the modern airborne environment is filled with an abundance of other compounds. This includes many forms of ice, freezing fog, lightning, birds, corrosive gases and aerosols, volcanic ash, sand and dust storms, rain, hail and ice crystals.
Engine contamination disturbs the airflow through the engine, affecting the overall performance and results in higher EGT. Turbine engines were not originally designed to operate in these contaminated environments. The flow of these contaminants can be immediately manifested by a decrease in engine performance, while other effects will be manifested by a gradual change in the engine’s performance. Some of these airborne environments must be avoided whenever possible. Other of these contaminants require decreased maintenance intervals to prevent unacceptable deterioration within the engine.
Sand, dust, dirt and harder particles like quartz or construction debris cause multiple negative effects on turbine powerplants. Compressor blades can erode, and molten silicates will stick in the turbine annulus, leading to loss of engine efficiency and surge margin. The accumulation of fine sand inside the engine can also damage turbine components or clog internal air passages for specific engine models. Turbine cooling systems will suffer damage, reducing component life. Lubricating systems can be contaminated. Support systems for electronics, heat exchangers mechanical systems and fuel supplies can be blocked.
Engine manufacturer Pratt & Whitney advises operators to proactively consider utilizing inlet barrier filters when operating in an airborne environment with tiny abrasive particles. Installation of intake and exhaust covers while the aircraft is parked for extended periods, especially in high wind environments, is highly recommended.
Flight operations near salt water or high pollution areas expose the turbine blades to a unique form of chemical attack called sulfidation. Every turbine engine uses fuel contaminated with sulfur, that when burned at high temperatures, emits varying amounts of sodium sulfate gas. This gas causes a corrosive deterioration of a turbine blade.
Airbus recommends performing regular engine washes to remove particles such as dirt, oil, sand and salt from the compressor. Pratt & Whitney Canada recommends desalination and desulfidation washes to slow down corrosion effects and borescope inspections to monitor engine condition. Depending on the engine type, you may need to do two different washes, compressor desalination and turbine desalination, to ensure thorough cleaning. How often you should do that depends on the environment where the aircraft is flying. Refer to your engine maintenance manual for more details on the frequency.
Volcanic ash is an example of the airborne contaminants that must be avoided whenever possible. Past encounters with volcanic ash have caused a total loss of thrust. A notable example occurred on Dec. 15, 1989 to a KLM Boeing 747 that encountered volcanic ash from Alaska’s Mount Redoubt. The obstructed air flow through the engines caused all four engines to lose power.
Ash particles are predominantly composed of silicates with a melting point of 1100 deg. C. When heated by the engine combustion section, these particles become molten glass that can coat fuel nozzles, the combustor and the turbine blades. This reduces the efficiency of fuel mixing and restricts air from passing through the engine. It also reduces the “throat area,” causing an even greater adverse pressure gradient in the burner and compressor discharge areas that will cause engine surges.
When ash enters the engine, it also causes erosion along the leading edges of critical components. Remember that each blade on the rotors and stators is essentially an airfoil whose shape has been specifically designed to maximize the compression of the air. The roughening of the surfaces over those airfoils causes the same effects as roughening of a wing’s surface. It causes extra drag and early boundary layer separation. This will lead to higher engine temperatures and reduced specific fuel consumption. It is economically unfeasible to smooth out the surface roughness on compressor blades caused by the abrasion.
In Part 3, we describe how engine manufacturers have worked to improve the efficiency and reliability of their powerplants.
Engine Limitations Are Not Mere Suggestions, Part 1: https://aviationweek.com/business-aviation/aircraft-propulsion/engine-l…