Peopling Pilatus
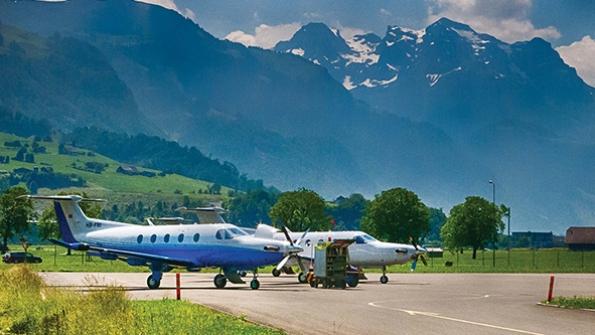
Credit: Kimberly Henneman
How does a company that designs and manufactures specialized, turbine-powered aircraft and is located deep within the Swiss Alps recruit a workforce with the skills necessary to compete on the world stage? The answer is multifaceted but begins with an educated population. When I posed a question in...
Subscription Required
This content requires a subscription to one of the Aviation Week Intelligence Network (AWIN) bundles.
Schedule a demo today to find out how you can access this content and similar content related to your area of the global aviation industry.
Already an AWIN subscriber? Login
Did you know? Aviation Week has won top honors multiple times in the Jesse H. Neal National Business Journalism Awards, the business-to-business media equivalent of the Pulitzer Prizes.