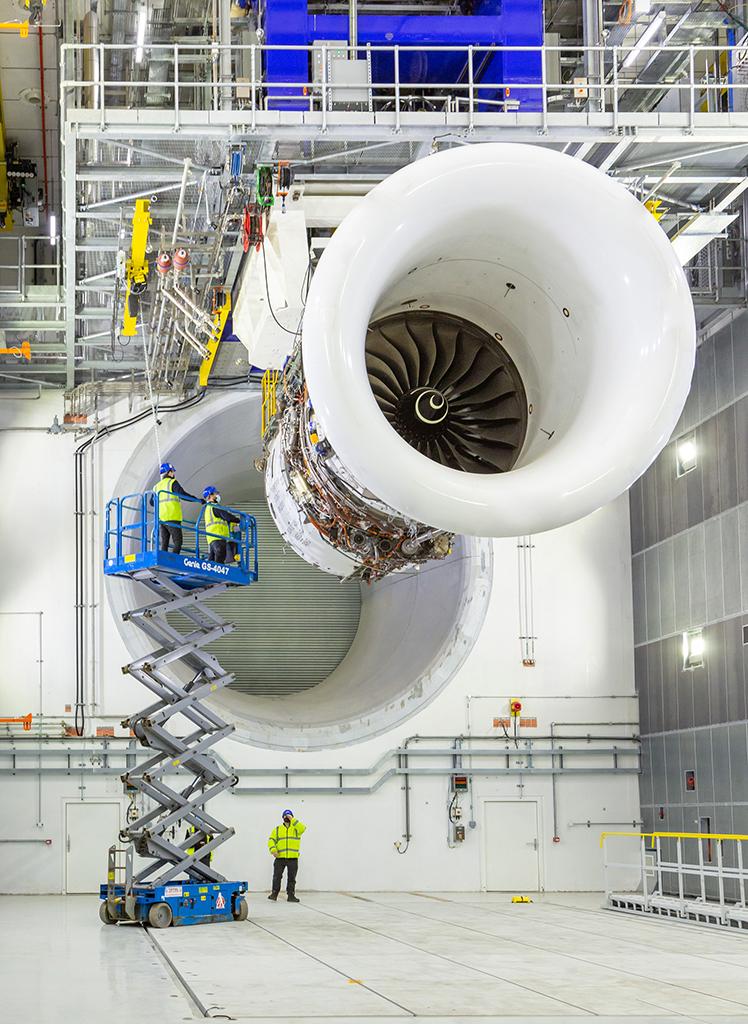
The UltraFan demonstrators will be tested in Rolls-Royce’s newly completed Testbed 80 in Derby. Commissioned in January using a Trent XWB-97 engine, the site encloses an area of 80,730 ft.2 (7,500 m2 ) between walls 49 ft. tall and 49 ft. wide. Constructed using 3,450 tons of steel and 290,525 ft.3 of concrete, the building is dominated by a 95-ft.-tall intake tower at its north end and a 123-ft.-tall exhaust stack at the south. The extra wall thickness was required to protect surrounding areas from an enormous X-ray machine that Rolls will use to internally inspect engines at the rate of 30 images per second while running in the testbed.

Rated at 87,000 lb. thrust, the test engine will have a 140-in. fan diameter, making it the largest aircraft engine yet developed. Although the engine does not yet have a firm application, Rolls says the demonstrator—which will run in early 2022—will pave the way for a range of fuel-efficient products later in the decade covering the 25,000-100,000-lb.-thrust range.
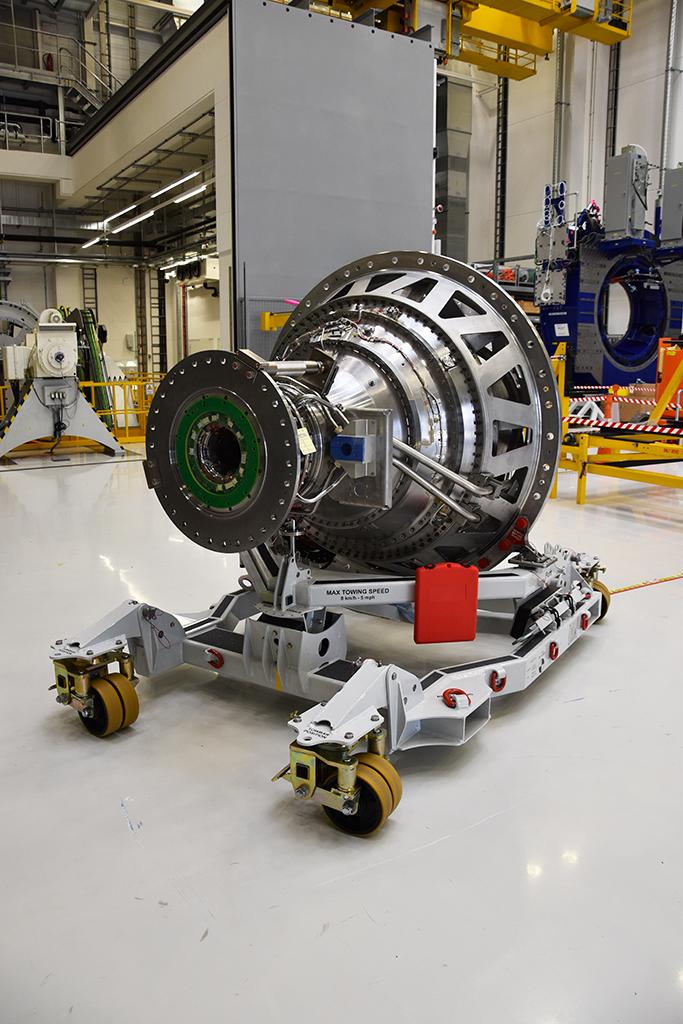
The power gearbox (PGB) at the heart of the new engine slows the fan while allowing the intermediate turbine to run at higher optimum speed conditions. The demonstrator configuration PGB ran to full takeoff power on a rig in Germany at the end of December 2020, transforming over 50 megawatts of power with a thermal efficiency level better than 99%. This unit, dubbed DP208, is pictured en route to the attitude test rig in the company’s Dahlewitz facility. The unit destined for the first UltraFan demonstrator is now under assembly and is designated DP211 in acknowledgment of Rolls-Royce’s heritage RB.211 engine family.

The UltraFan’s all-new core incorporates a low-emissions ALECSys (advanced low-emissions combustion system) lean-burn combustor, which has been tested in a Trent 1000 donor engine. Recent runs included tests with unblended sustainable aviation fuel (SAF) from U.S.-based World Energy. Testing with the SAF, refined in California, targets net reductions in CO2 life-cycle emissions by more than 75% compared to current jet fuel and has potential for further reductions in the future. Rolls says the UltraFan will be certificated for 100% SAF operation “out of the box.”

Lightweight composite material is used for the fan case to compensate for the higher drag of the wider 15:1-bypass-ratio fan. The first case for the initial demonstrator, UF001, is close to completion in the company’s Bristol, England, site, where accessory parts are being attached and final machining is taking place.

Multiple composite titanium blades are in production for the 18-blade shipsets that will make up the fans for each of the four UltraFan demonstrators. Each blade is made from 500 plies of Hexcel’s HexPly M91 carbon-fiber-reinforced epoxy prepreg that are automatically laid up before being cured in an autoclave. After precision machining and coating, a protective titanium sheath is bonded to the leading edge to protect the blade against erosion, foreign object damage and bird strikes.

As parts for UF001 start to arrive at Rolls-Royce’s “DemoWorks” in Derby, England, the company is also evaluating new assembly methods based on digital instruction systems. Engineers and mechanics are practicing putting replica components together—like the pictured key core modules—using representative tooling features and replica parts made from additively layered manufactured plastic. Resembling a giant multicolored popsicle, the pictured core includes the power gearbox mount at the top and the high-speed intermediate turbine system module at the base.
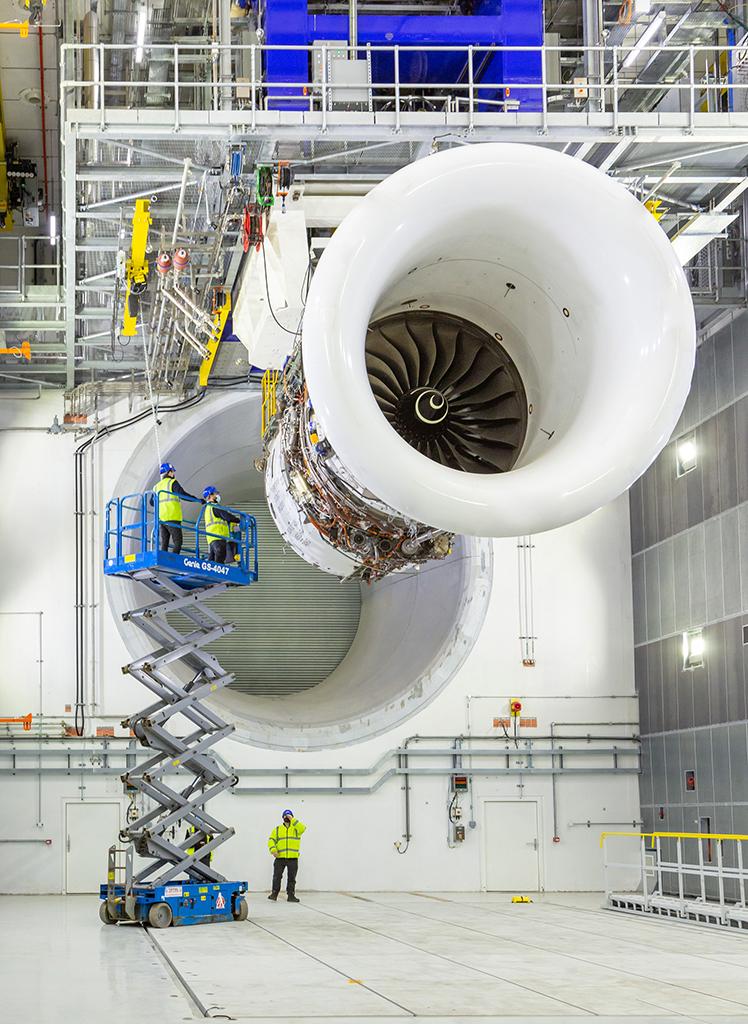
The UltraFan demonstrators will be tested in Rolls-Royce’s newly completed Testbed 80 in Derby. Commissioned in January using a Trent XWB-97 engine, the site encloses an area of 80,730 ft.2 (7,500 m2 ) between walls 49 ft. tall and 49 ft. wide. Constructed using 3,450 tons of steel and 290,525 ft.3 of concrete, the building is dominated by a 95-ft.-tall intake tower at its north end and a 123-ft.-tall exhaust stack at the south. The extra wall thickness was required to protect surrounding areas from an enormous X-ray machine that Rolls will use to internally inspect engines at the rate of 30 images per second while running in the testbed.

Rated at 87,000 lb. thrust, the test engine will have a 140-in. fan diameter, making it the largest aircraft engine yet developed. Although the engine does not yet have a firm application, Rolls says the demonstrator—which will run in early 2022—will pave the way for a range of fuel-efficient products later in the decade covering the 25,000-100,000-lb.-thrust range.
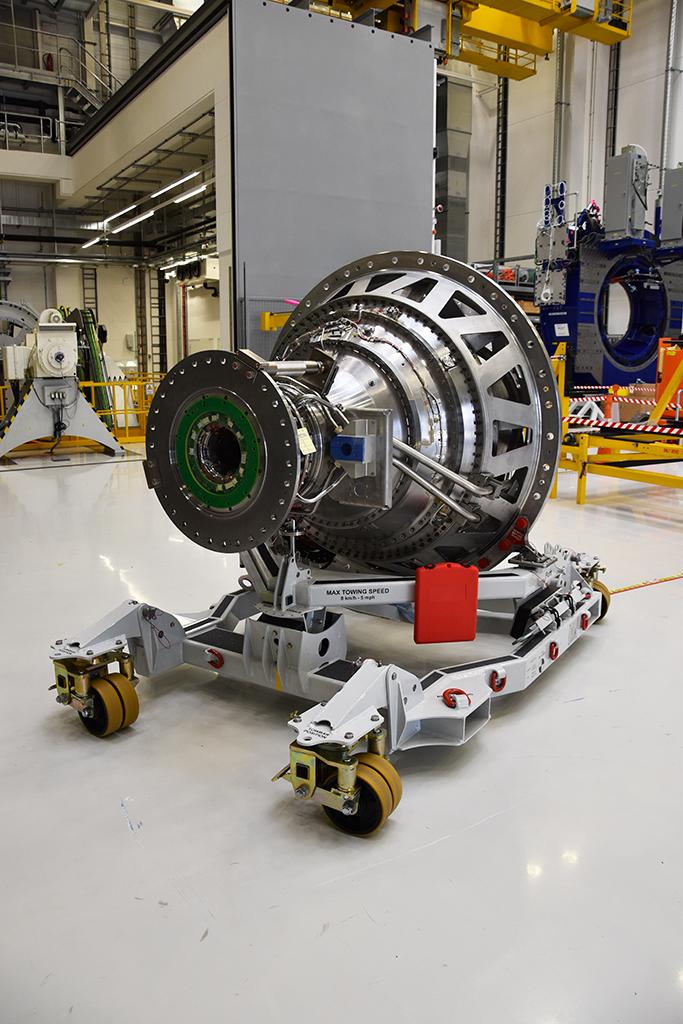
The power gearbox (PGB) at the heart of the new engine slows the fan while allowing the intermediate turbine to run at higher optimum speed conditions. The demonstrator configuration PGB ran to full takeoff power on a rig in Germany at the end of December 2020, transforming over 50 megawatts of power with a thermal efficiency level better than 99%. This unit, dubbed DP208, is pictured en route to the attitude test rig in the company’s Dahlewitz facility. The unit destined for the first UltraFan demonstrator is now under assembly and is designated DP211 in acknowledgment of Rolls-Royce’s heritage RB.211 engine family.

The UltraFan’s all-new core incorporates a low-emissions ALECSys (advanced low-emissions combustion system) lean-burn combustor, which has been tested in a Trent 1000 donor engine. Recent runs included tests with unblended sustainable aviation fuel (SAF) from U.S.-based World Energy. Testing with the SAF, refined in California, targets net reductions in CO2 life-cycle emissions by more than 75% compared to current jet fuel and has potential for further reductions in the future. Rolls says the UltraFan will be certificated for 100% SAF operation “out of the box.”

Lightweight composite material is used for the fan case to compensate for the higher drag of the wider 15:1-bypass-ratio fan. The first case for the initial demonstrator, UF001, is close to completion in the company’s Bristol, England, site, where accessory parts are being attached and final machining is taking place.

Multiple composite titanium blades are in production for the 18-blade shipsets that will make up the fans for each of the four UltraFan demonstrators. Each blade is made from 500 plies of Hexcel’s HexPly M91 carbon-fiber-reinforced epoxy prepreg that are automatically laid up before being cured in an autoclave. After precision machining and coating, a protective titanium sheath is bonded to the leading edge to protect the blade against erosion, foreign object damage and bird strikes.

As parts for UF001 start to arrive at Rolls-Royce’s “DemoWorks” in Derby, England, the company is also evaluating new assembly methods based on digital instruction systems. Engineers and mechanics are practicing putting replica components together—like the pictured key core modules—using representative tooling features and replica parts made from additively layered manufactured plastic. Resembling a giant multicolored popsicle, the pictured core includes the power gearbox mount at the top and the high-speed intermediate turbine system module at the base.
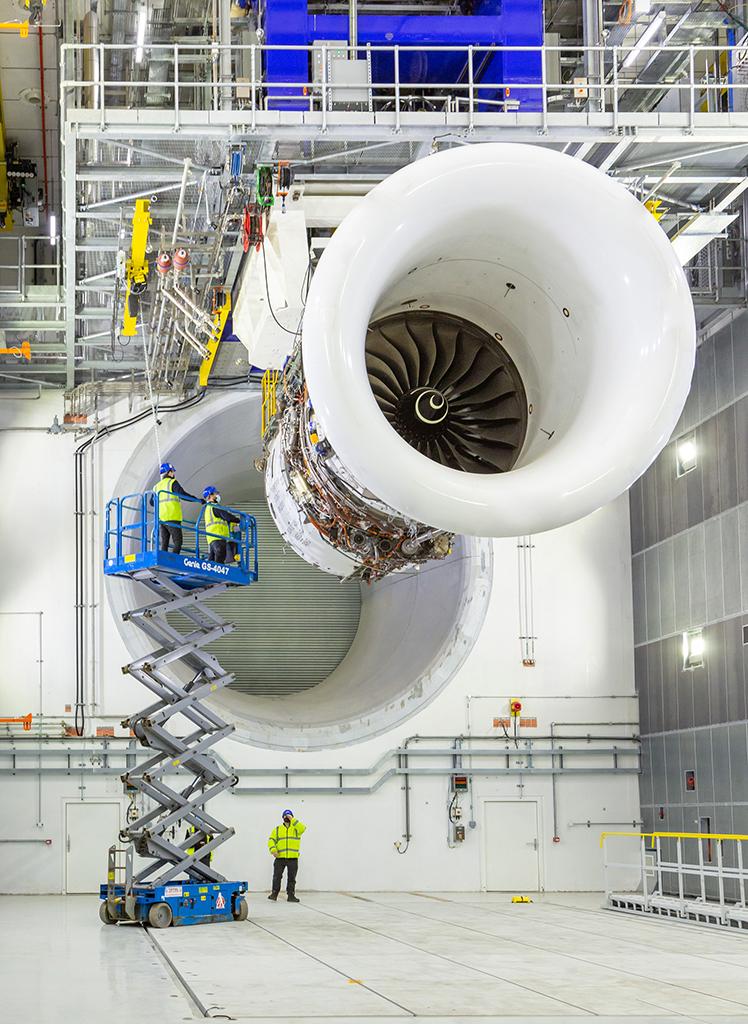
The UltraFan demonstrators will be tested in Rolls-Royce’s newly completed Testbed 80 in Derby. Commissioned in January using a Trent XWB-97 engine, the site encloses an area of 80,730 ft.2 (7,500 m2 ) between walls 49 ft. tall and 49 ft. wide. Constructed using 3,450 tons of steel and 290,525 ft.3 of concrete, the building is dominated by a 95-ft.-tall intake tower at its north end and a 123-ft.-tall exhaust stack at the south. The extra wall thickness was required to protect surrounding areas from an enormous X-ray machine that Rolls will use to internally inspect engines at the rate of 30 images per second while running in the testbed.
Almost exactly seven years after announcing plans to develop a completely new gear-driven commercial engine family, Rolls-Royce is bringing together the major components for the first UltraFan demonstrator (AW&ST Feb. 8-21, p. 19).