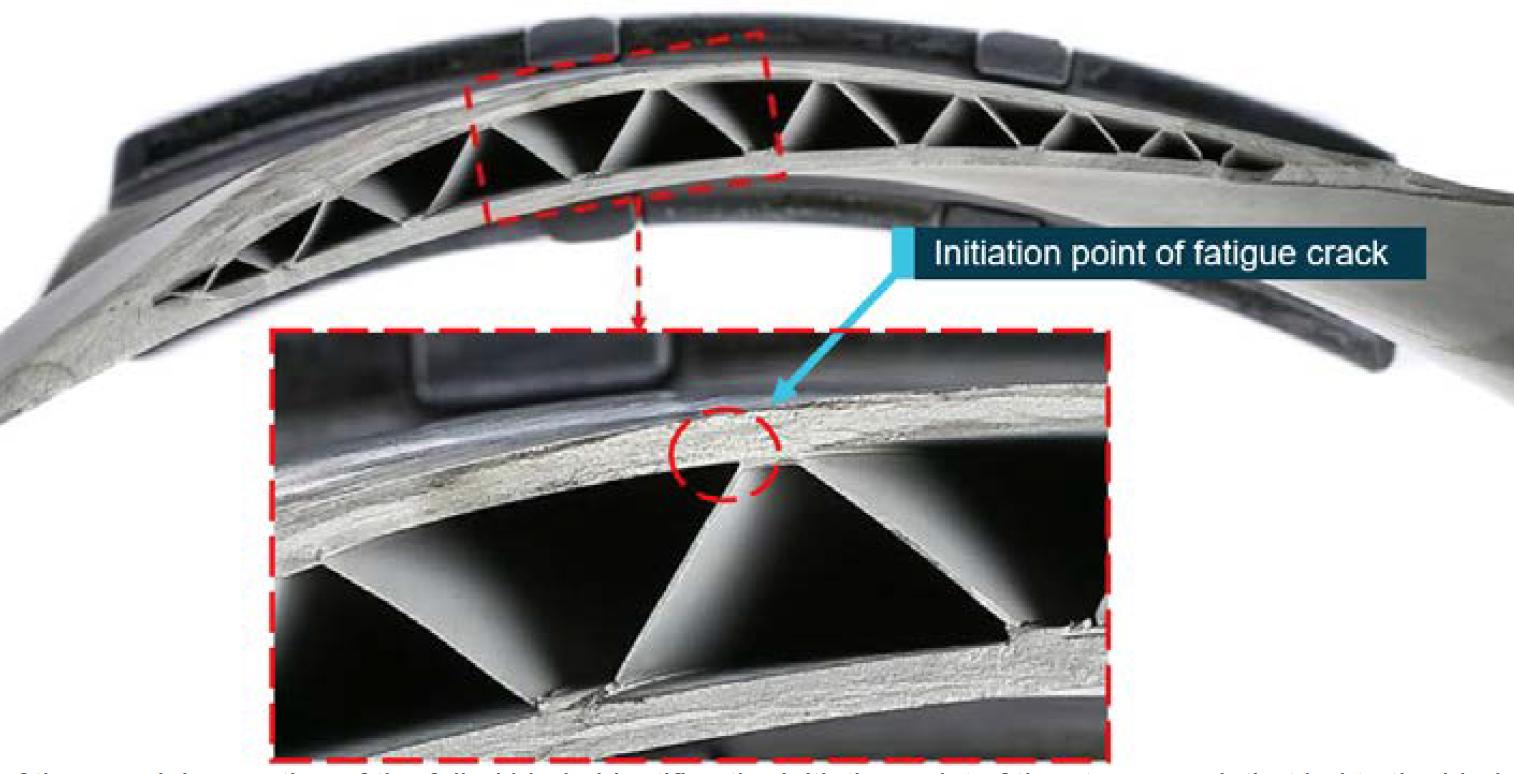
An anomaly in the fan-blade manufacturing process combined with insufficient inspection procedures set the stage for the June 2017 inflight failure of a Rolls-Royce Trent 700 powering an AirAsia X Airbus A330-300, the Australian Transport Safety Bureau (ATSB) found.
Rolls has revamped its inspection process for in-service blades and is modifying the blade’s design to reduce the risks of a specific pattern of crack development linked to multiple failures.
The incident occurred about 1 hr. into a scheduled flight between Perth, Australia, and Kuala Lumpur, Malaysia. The 11-year-old A330, 9M-XXE, experienced a no. 1 (left) engine malfunction that triggered several flight-deck warnings, including a no. 1 engine stall warning, ATSB’s final report on the incident, released July 7, said. The crew declared an emergency, assessed the situation, and decided to return to Perth rather than proceed to one of several closer, smaller airports—a move that ATSB concluded was appropriate based on the circumstances and the airline’s policies.
The damaged blade caused severe vibrations that were reduced, but not eliminated, by shutting the engine down. The aircraft returned to Perth and landed without further problems.
Post-flight examination found that nearly three-quarters of one fan blade was missing. Damage was evident on the inner cowling and some downstream engine components. Neither the engine mount nor the airframe suffered any visible damage.
Trent 700 blades are made by bonding three sheets of titanium alloy together to form a wide-chord shape with a hollow core containing a corrugation-style support structure. Investigators traced the blade failure to a fatigue crack that started in an “acute corner” of the part’s design where one of the support structures, or membranes, met the blade’s inner panel.
Previous fan blade failures traced to a manufacturing flaw meant that Trent 700 blades were subject to periodic inspections to detect internal cracking. But Rolls and investigators found the intervals—3,600 cycles since new for the initial inspection and every 2,400 cycles for repetitive checks—were too large to detect cracks and prevent them from leading to failures.
The AirAsia X blade, manufactured between December 2009 and February 2010, underwent an inspection in September 2014, at 3,062 cycles. It failed at 4,701 cycles.
Rolls reviewed nine Trent 700 fan-blade failures as part of its analysis, including both the AirAsia X incident and one that occurred in February 2018. Six were linked to “manufacturing issues” unrelated to the blade’s geometry, while three, including the AirAsia X failure, stemmed from stress on acute corners.
“Rolls-Royce identified that the complex manufacturing processes used in the production of Trent 700 fan blades can result in a variation in the membrane-to-panel geometry; in particular the acute corner radius,” ATSB said. “Thus, there was potentially a population of Trent 700 fan blades with acute corner radii that made them susceptible to early-onset fatigue cracking.”
The manufacturer has modified its inspection recommendations several times, reducing initial and follow-up check intervals to 1,200 cycles and revising the phased-array process so it detects smaller anomalies and ensuring all blades were inspected by the end of 2018. EASA mandated the inspections.
Rolls also analyzed its blade designs and found that “panel stresses of Trent 700 blades were relatively high in comparison to other blades in the [Trent] family,” ATSB said, but not “high enough to be the only contributor to the failure.” Rolls’s conclusion: the high panel stress combined with the “concentrating effects of the small acute corner radii” increases the likelihood of cracks forming at the radius location.
Rolls has “identified areas for improvement, such as introducing local panel thickening to reduce blade panel stress to a level that will mitigate the acute corner variations observed in production,” ATSB said. Modified blades are expected to be available by the end of 2021.
“Rolls-Royce are continuing to try to understand what manufacturing processes may influence the acute corner radii,” ATSB said.