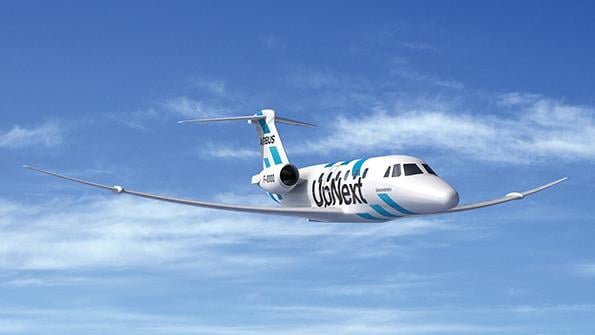
At the root of the wingtip extension, a semi-aeroelastic hinge is triggered in cases of strong turbulence.
One of the principles engineers follow when designing an aircraft is that it must withstand rare instances of extreme conditions. That approach is used in the design of the wing, a part of the airframe that may have to face exceptional turbulence. Engineers make the wing’s structure strong enough for those occurrences, adding weight in the process. Therefore, for most flights, the wing is heavier than necessary.
What if that design margin could be eliminated? That is exactly what engineers at UpNext, Airbus’ technology innovation arm, are endeavoring to do.
- UpNext’s “Extra Performance Wing” targets efficiency
- Morphing-wing concept to become a reality
The design of the OEM’s Extra Performance Wing combines the reduced drag of a high-aspect-ratio wing with the greater efficiency of an adaptive profile. Whereas a greater wingspan usually comes with increased weight, engineers will test features that should keep the weight unchanged.
They are making gradual progress toward the first flight of an Extra Performance Wing—on a modified business jet—aiming at a 5-10% improvement in fuel consumption.
UpNext relies on so-called agile methods, enabling fast evaluation of the technologies. The timing of the program makes it compatible with the launch of a next-generation single-aisle aircraft.
“All the technologies will be validated in a relevant environment by the end of 2024,” says Sebastien Blanc, UpNext technical director for the Extra Performance Wing. That stage corresponds to Technology Readiness Level 6, which OEMs usually take as the basis for a full product development.
UpNext has purchased a pre-owned Cessna Citation VII. The technology arm plans to replace the original wing with an extended, composite one measuring approximately 20 m (66 ft.) in span, including 2-m movable tip sections.
Increasing the aspect ratio reduces the wingtip vortex and therefore drag. However, as the wing must be able to withstand extreme turbulence, increasing the span generally calls for strengthening its structure. In turn, the weight grows.
“The overall objective is to make the greater aspect ratio neutral in terms of weight,” Blanc says. “That requires active control.”
At the root of the wingtip extension, a semi-aeroelastic hinge is triggered in cases of strong turbulence. That hinge frees the wingtip to flap and alleviates the loads induced in the wing structure by that turbulence. The need for reinforcements is eliminated.
The hinge is designed to be activated by a mechanism incorporating a drive-gear system and clutch. The electro-mechanical system, which is being developed by Curtiss-Wright, also will be able to position the wingtip to specific angles for various flight modes, as well as takeoff and landing. In addition, the hinge will be used to keep the wingspan compatible with airport infrastructures.
The demonstration wing’s trailing edge will be fitted with three flaps, each with four multifunctional trailing edges, or tabs, which can change position very fast. “Like a bird’s wing, the demonstrator’s wing will adapt to flight conditions: altitude, speed and aircraft weight,” Blanc says. The flaps can retract, thus modifying the chord. Also to make the morphing-wing concept a reality, tabs can move to alter camber.
Just as with the semi-aeroelastic hinge, the additional control surfaces also help curb wing load in demanding maneuvers and strong turbulence. Pop-up spoilers, to be found on the folding wingtips and possibly elsewhere, will contribute as well, Blanc says.
Another result of the additional control surfaces is passenger comfort, as they can limit vertical acceleration in turbulence, Blanc says. In addition, they can control the flutter induced by the more flexible wing, itself a consequence of the greater aspect ratio.
The Citation VII will be transformed into an uncrewed aircraft and the wing flight-tested remotely. “The idea is that such a breakthrough technology will be evaluated to the limits,” Blanc says.
Antennas and probes, to be used with the remote-control system, are being installed in Toulouse. Flight testing of the slightly modified Citation VII will involve on-board pilots in 2023.
The new wing then will be put in place. A lidar involving two lasers will be installed simultaneously in the cockpit, making the system able to anticipate turbulence 0.5-1 sec. ahead and move the control surfaces accordingly.
Set for the second half of 2024, the flight-test campaign is planned to last about 100 flight hours. It will take place in an area measuring 200 km (124 mi.) in radius from the French Air and Space Force base in Cazaux. Airbus test pilots will conduct the flight-test program from the ground.
The wing will be representative of a 52-m wing on a single-aisle aircraft, whereas the A320 family uses a 36-m wing. “All the learnings from the reduced-scale wing on the Citation VII may be applied to a future aircraft wing design, for any platform, using any fuel,” Blanc says. The data would be scaled up by using computational models, such as factoring in the difference in Reynolds number.