Opinion: What The COVID-Catalyzed Digital Transformation Has Taught Us
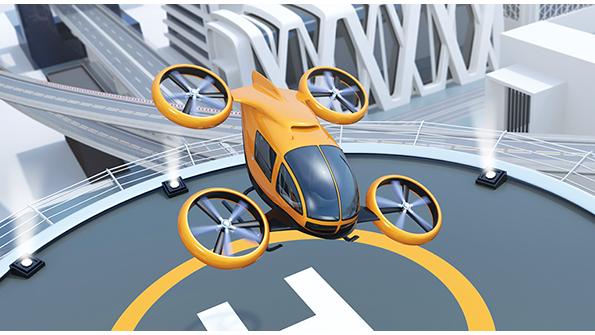
Of course, no one can plan for a pandemic or any crisis, for that matter. But the current pandemic has exposed structural flaws in the way we do business and has forced us into a massive remote-collaboration model.
When this happened, the aerospace and defense (A&D) companies that had already begun taking steps toward digitalization to improve product development, become more agile and introduce automation and traceability into their organizations learned that they had also reduced their risk profiles. Digitalization enabled these companies to quickly evolve and adapt. And the pandemic has only accelerated their transformation as they prepare for a recovery.
Digitalization empowers companies to innovate and at the same time address the more pressing trends facing the industry today. To illustrate the benefits, let’s look at the intense innovation going on in urban air mobility (UAM). Along with the global heavyweights, plenty of startups are vying to be first in UAM. There is no doubt that digitalization will be the key competitive advantage in bringing viable commercial offerings to market.
Embracing the comprehensive digital twin. The UAM platform represents unique design and manufacturing challenges; it consists of multiple disciplines and functions all interacting simultaneously. Design and engineering teams need to understand multi-domain solutions requiring complex trade-offs. A comprehensive digital twin, with multidisciplinary advanced simulation, provides critical data on how specific product attributes and domains interact with one another within the overall interconnected system.
The digital twin accelerates the design process by enabling the simulation and optimization of every aspect of the UAM vehicle before committing to a physical prototype. For example, the mechatronics of vertical takeoff and landing can be fully modeled, simulated and analyzed to ensure the most effective approach is achieved even within aggressive design schedules. The interactions between the mechanical, electrical and software domains can be fully explored and refined without creating a single physical model.
Equally important is the digital thread that weaves together the digital twin of the production environment, enabling numerous data processes across multiple domains or systems.
Moving toward digital manufacturing that supports additive. UAM vehicles need to be as lightweight as possible to save on fuel and battery life without sacrificing structural integrity. Moreover, many UAM platforms will be custom configured, so additive technologies will be key to UAM manufacturing. The digital thread for additive manufacturing enables companies to successfully implement additive manufacturing at an industrial scale to design and produce optimal structures. The result? Companies get the reliability and traceability that aerospace demands, while allowing manufacturing processes to adapt quickly to evolving customer requirements or design optimizations. You become more flexible while reducing time and costs.
“Remote collaboration” for maximum reach. UAM vehicles will soon emerge as a legitimate mode of transportation in our urban centers. To ensure that customer requirements, local laws and regulatory issues are addressed, an immersive 3D environment can bring together design teams from a variety of locations to conduct extensive design reviews as part of real-time collaboration. Immersive 3D also allows companies to explore design alternatives in ways they have never before been able to do—all from the comfort of home offices.
Augmented reality on the factory floor. As the manufacturing workforce in A&D responds to global shifts in demographics and cost pressures, workers must be able to ramp up quickly and take on new tasks. This is especially crucial in the emerging UAM market, where the workforce needs to build things right the first time to gain and keep a competitive edge. Digitalization enables design teams to replace 2D drawings and work instructions with 3D augmented reality, reducing the learning curve to realize productivity.
Preparing for the future with the digital enterprise today. To state it simply: Digitalization delivers benefits by fostering greater productivity, innovation and flexibility in both design and manufacturing. Now it is possible to bring new products to market faster and be more profitable in the process. And yes, it is possible to be ready to react quickly and adapt to the next crisis.
Dale Tutt is the vice president of aerospace and defense industry for Siemens Digital Industries Software.
The views expressed are not necessarily those of Aviation Week.