From Seals to Composites, Tracking Greene Tweed’s Flight
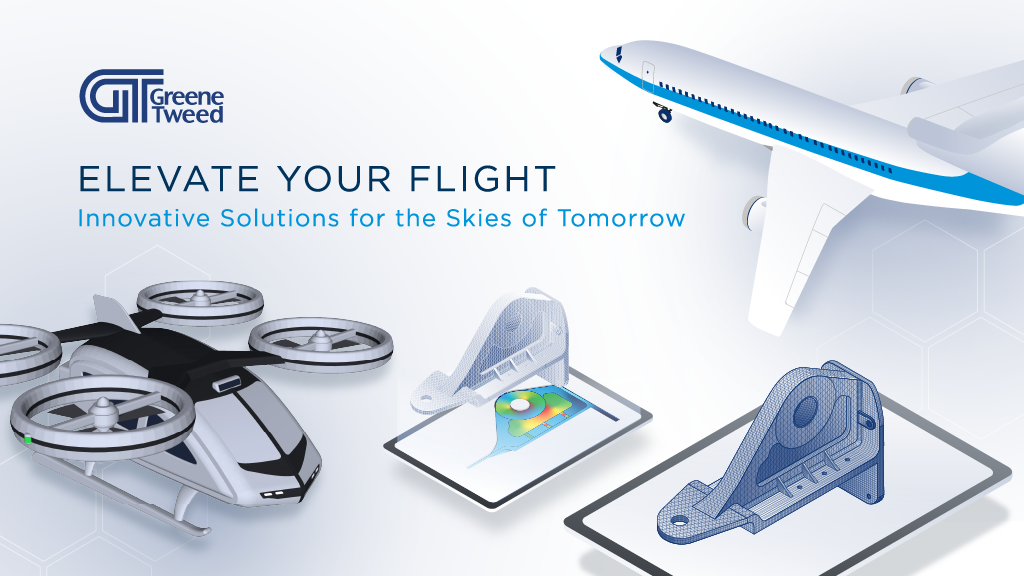
Think back to your last 10 flights. Chances are, on 8 out of those 10 commercial flights, at least one crucial component of your aircraft was built by Greene Tweed. That’s right – Greene Tweed’s sealing systems deliver certainty to an airplane’s critical components at 40,000 feet ‘when it can’t fail’ while our composite and structural components offer significant weight savings and energy efficiency.
“Our customers select us for our rich engineering heritage, decades of aerospace pedigree, and commitment to deliver efficiency, safety, and certainty. Our innovative products outperform and outlast the world’s harshest aviation environments with extreme temperatures, pressures, and aggressive fluids,” says Sébastien Dubois, Director, Aerospace and Defense Strategy at Greene Tweed.
Seals of Certainty
It all began six decades back, when Greene Tweed’s AGT® rings were chosen to ensure that PanAm, Eastern, and United fleets landed smoothly. Soon, the US Air Force F-4 Phantom program specified the AGT® seals throughout the aircraft. Since then, the 160-year-old company has pushed the limits of seal technology to engineer several more designs, such as Advanced Concept T-ring (ACT®), L-Cap, Fireproof Hydraulic Seal (FPH Seal™), Metal Spring Energized, and a host of other sealing solutions. From landing gears and braking systems to flight controls and engine systems, these seals don’t just ensure low leakage, but also withstand extreme environments in applications where failure is not an option.
Fly Lighter with Xycomp® DLF™
When any aerospace application demands materials lighter and stronger than metals, Greene Tweed’s thermoplastic composite Xycomp® DLF™ (Discontinuous Long Fiber) delivers. Designed to replace complex metallic components for aerospace, defense, space, and industrial applications, this material offers superior resistance to fatigue, vibration, and impact, while providing up to 50 percent weight savings over traditional metallic parts. With every pound shed through the adoption of Xycomp® DLF™ composite, aircraft(s) become more fuel efficient, thus reducing operating costs. GE Unison, a division of GE Aerospace, for example, replaced its metallic Engine Build Up (EBU) bracket with Greene Tweed’s net-molded DLF carbon/PEEK EBU brackets to gain 86 percent weight savings while reducing machining and assembly operations.
More than 400,000 DLF™ Components are currently in service across 12 commercial aircraft platforms, including complex contour shapes with molded-in features. Components made of Xycomp® DLF™ have successfully replaced metals in very complex-shape applications, such as Variable Bypass Valve Door.
Ready for Advanced Air Mobility
As the aviation industry bets on bringing electric advanced air travel to the masses in the next few years, Greene Tweed is teaming up with some of the biggest Urban Air Mobility (UAM) manufacturers to accelerate their new and emerging platforms. Leveraging 60 years of experience in serving major aerospace customers, its lightweight thermoplastic composite Xycomp® DLF™ components and innovative sealing solutions are playing a crucial role in powering the Advanced Air Mobility (AAM) revolution.
That’s not all. Greene Tweed is developing innovative materials and sealing solutions that can withstand sustainable aviation fuels and hydrogen’s complex properties to reduce carbon emissions and pave the way for a greener future. They are also looking into custom-engineering components and seals for electric aircraft as well as supersonic and hypersonic travel.
The possibilities are endless, says Sébastien Dubois, “As new technologies emerge and aircraft designs evolve, we’ll innovate and adapt, developing new materials, processes, and technologies to meet the stringent requirements. For us, these new platforms are opportunities to showcase Greene Tweed’s expertise and play a critical role in shaping the future of aerospace.”
Learn More: https://www2.gtweed.com/aviationweekwebads
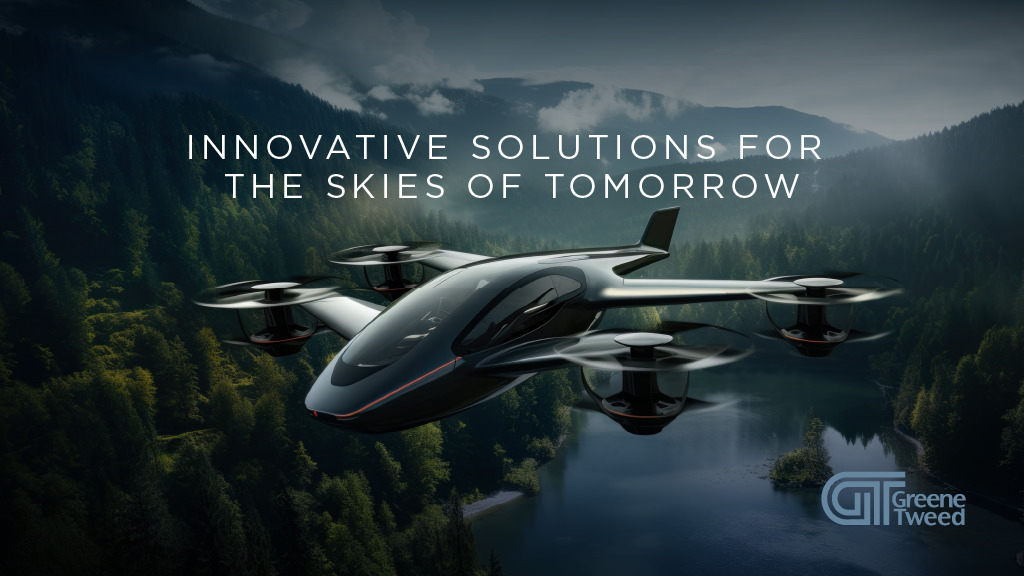