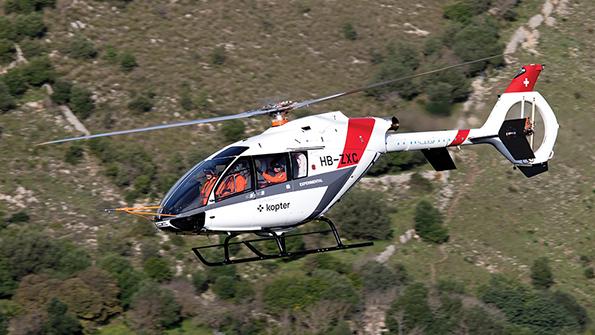
Switzerland’s Kopter Group believes it can shake up the light-single-engine rotorcraft market with its SH09 helicopter.
As a newcomer in an industry with tall barriers to entry, the fledgling company is making major strides in flight-testing progress as it aims to bring its distinctive helicopter to market in 2020.
“The market is big,” says Kopter CEO Andreas Lowenstein, “and bigger than what the forecasters are saying.”
- Kopter close to finalizing configuration of SH09
- Single-engine IFR capability planned for 2022
- Close relationship established with KAI in South Korea
Lowenstein, a former Eurocopter executive, says the rotorcraft market is an “offer-driven market . . . if you come up with the right product at the right cost, safety, payload and economic performance, and if the equation is right, you can resize the market.”
He points to the Leonardo AW139 twin-engine medium rotorcraft as an example, which entered a market previously dominated by Airbus AS365/EC155 Dauphins, Sikorsky S-76s and Bell 412s.
“When the AW139 arrived, it was a real game changer,” he says. “Suddenly the market was 1.5-2.5 times bigger than in the past. I feel if we can do it right, we can provoke the same effect.”
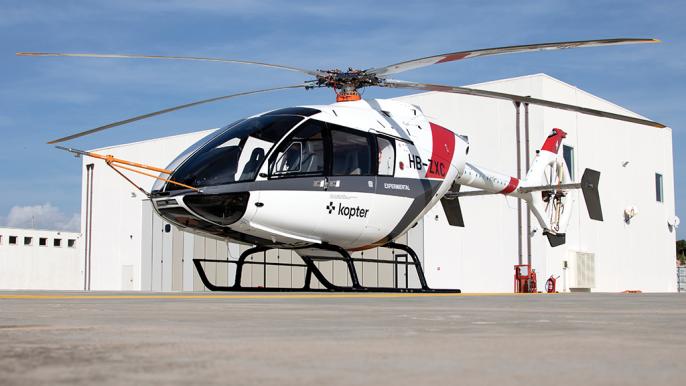
The vision is not too farfetched as the SH09 is entering a market which has been arguably starved of innovation for decades. Airbus’ H125 Ecureuil, or AStar as it is known on the U.S. market, is the reference point for the SH09, as is Bell’s 407.
The 407 is a more powerful derivative of Bell’s 1960s-era LongRanger while the H125 was born from Aerospatiale’s AS350, which first flew in the 1970s. Both have undergone iterative upgrades over the years, receiving uprated engines and new avionics.
The Honeywell HTS900-powered SH09 already appears to have secured some market share, with 70 firm orders and more being saved up for announcement at Heli-Expo. Lowenstein says the company has “solidly sold” the first three years of production output, with some customers now ordering for the fourth and fifth years.
“People are waiting for this aircraft, and we are seeing bigger operators in the EMS (emergency medical services) and tourism, being extremely interested,” says Lowenstein.
He also notes that the customers who previously would have been in the market for a twin-engine helicopter in the class of Airbus’ H135 and the Bell 429 are looking at the SH09 because of the improved economics associated with a single engine.
Kopter already has secured a site for future final assembly in the U.S., at Lafayette, Louisiana, beginning in 2025 and made some inroads into the Asia-Pacific market (AW&ST March 11-24, 2019, p. 40).
In October, the company signed a framework agreement with Korea Aerospace Industries (KAI) for marketing, sales and potential assembly of the helicopter in South Korea.
Lowenstein reports the Koreans are potentially interested in the SH09 as a training platform for the military, which could lead to a “joint industry project to cover Korean needs.”
“Today we have working groups [with KAI] progressing on a program which has a number of phases looking at what markets we can tackle, work on industry and about potential technology transfer,” he explains.
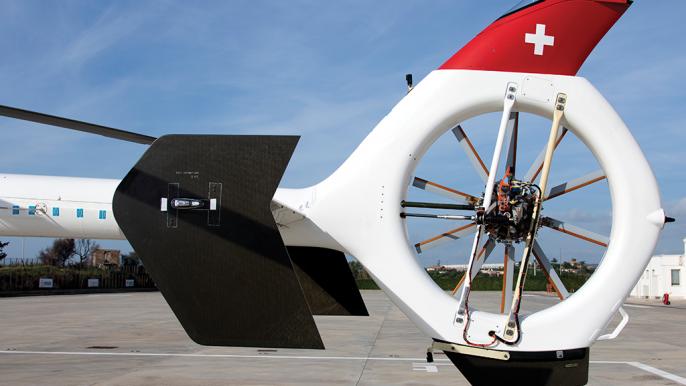
Lowenstein says the SH09’s hidden benefit has been its size. The helicopter offers a cabin not dissimilar in size to its twin-engine competitors, capable of seating up to eight passengers with a single pilot. In the rear under the tailboom, large clamshell doors provide access to the rear cabin to load a stretcher or baggage. Loading at the rear can be done with the engines running, thanks to the shrouded Maestro anti-torque system.
Up front, the current prototype, P3, is using a Sagem-developed avionics suite, but production aircraft will use the Garmin G3000H system, which allows the aircraft to be single-engine IFR-ready (instrument flight rules) once development of a four-axis autopilot is complete and certified. The company’s roadmap for this work foresees the SH09 being IFR-ready in 2022. IFR-capable single-engine helicopters are coming back into fashion, in part prompted by the U.S. Navy’s need for an IFR-certified training helicopter, but industry is already seeing growing interest from the EMS industry, particularly in the U.S.
Development of the SH09 has undergone fits and starts since the concept was unveiled in 2011 by the then-Marenco Swisshelicopter. An initial prototype, P1, which flew in 2014 was a “proof of concept,” recounts Michele Riccobono, Kopter’s chief technical officer and head of flight operations. P2, which flew in February 2016, took the concept a little further, but it was P3, which took to the air in November 2018, which the company says represents a “reset” in terms of design and development. Both P1 and P2 have been withdrawn from use.
Testing did not start well, however, when it was discovered through nondestructive testing that the castings of the upper housing of P3’s main gearbox had major defects. Engineers noted shrinkage, porosity and even areas that had been repaired by welding with the wrong filler. And none of the issues had been reported by the supplier. The gearbox is critical as it also features four load-bearing arms that connect it to the helicopter’s airframe.
“If I have to list the important jeopardizing issue for the SH09 development, it is the gearbox. . . . The aftermath cost us close to nine months of delay,” says Riccobono.
Although the supplier was fired immediately and a new one found, it would take months before the new components would be ready. The decision was made to fly with a limited flight envelope with the best of the castings, and several of the worst were broken as the company worked to define load limits.
“We had to convince ourselves first that it was safe enough to fly in a limited envelope with the flawed casting,” says Riccobono. “Once they saw how we approached it, EASA (the European Union Aviation Safety Agency) gave us the clearance.”
The casting was instrumented and the limitations in the flight envelope were severe. Even during takeoff, the crew could not apply lateral cyclic, so the aircraft had to take off and land sliding sideways.
“With that gearbox, we achieved a lot,” says Riccobono. “We reached 11,300-ft. density altitude and a speed of 125 kt., and we were able to fine-tune the aerodynamics.”
Retrofitting the gearbox with a revised upper housing provided by the new supplier in September was a “relief” says Kopter’s chief test pilot, Russ Grant. “We could finally start flying with the pilots flying the helicopter rather than the helicopter flying the pilots,” he adds.
“If we had not spotted the issues, most likely we would have had a serious accident,” says Riccobono, pointing out the defective castings only could carry one-third of the expected load.
Internally, the SH09’s main gearbox differs from other helicopters, as it uses an architecture in which the planetary stage employs stationary planet gears and a rotating ring which is connected to the main rotor mast. This contrasts with most light helicopters, which use a fixed ring, with the main rotor mast connected to planet gears rotating around a sun gear. Kopter says its patented design makes it easier to lubricate the planetary gears and bearings as one oil-jet nozzle can be provided for each gear. The gearbox is less likely to jam in the event of planet-gear failure.
Since the gearbox retrofit, the flight-test team has been steadily increasing aircraft weight to 2.6 metric tons, moving toward the planned maximum takeoff weight of 2.85 metric tons.
Flight testing is underway in Pozzallo, a small heliport on the southern coast of Sicily. The area is blessed with open unrestricted airspace and much better weather than Kopter’s Swiss home, where restrictions mean flying cannot take place even during lunchtime. During December, the engineering team began testing a new rotor head and main rotor blades with the aim of installing them in January, bringing the aircraft closer to its final production standard configuration.
Test pilots say the aircraft is flying well with low vibration, a comfortable ride and low pilot workload, but in some corners of the envelope “it shows some weaknesses,” says Grant. “It is a case of finessing those corners of the flight envelope.”
The company is targeting certification this year under the EASA’s CS27 standard for small rotorcraft, with Kopter planning to introduce additional capabilities through the notification of the design change process.
The first certification step will be to have the aircraft approved for visual-flight-rules operations to a density altitude of 16,000 ft. and a temperature operating range of -10 to 35C. The company then plans to extend that temperature range with cold-weather trials in Alaska and then hot-and-high flying in Colorado. These trials will be performed by production-standard prototypes PS4 and PS5, with PS4 envisioned to fly later this year.
Other upcoming changes include a new fuel tank configuration. Currently the aircraft uses tanks made of Kevlar, with two fitted under the cabin and one each in the rear cabin walls for a total capacity of 750 liters. However, drop tests revealed the tanks could not sustain the impact, prompting the company to adopt a new configuration developed by Safran’s Zodiac’s business. The new configuration uses fuel bags and concertina fuel lines that can cope with the drop-test impact.
The SH09 also will be equipped with a cockpit voice recorder as standard equipment to support post-accident analysis. Such equipment is not standard in this class.
Work is now underway to gear up for production in Switzerland. The company’s facilities at Mollis will be big enough for the initial production phase of around 25-30 aircraft per year. Architects are putting finishing touches on plans for a new 24,000-ft.2 facility that will join the company’s geographically separated facilities under one roof. The aim is to have the facilities ready for 2022 for an envisaged ramp-up in production.
Lowenstein says the company wants to stay under the radar and not attract too much attention from its larger competitors. “There is no reason to excite everybody today . . . but I think it is difficult to do much better than what we are doing, and we are a number of years ahead,” he says. c