Digital Certification Management
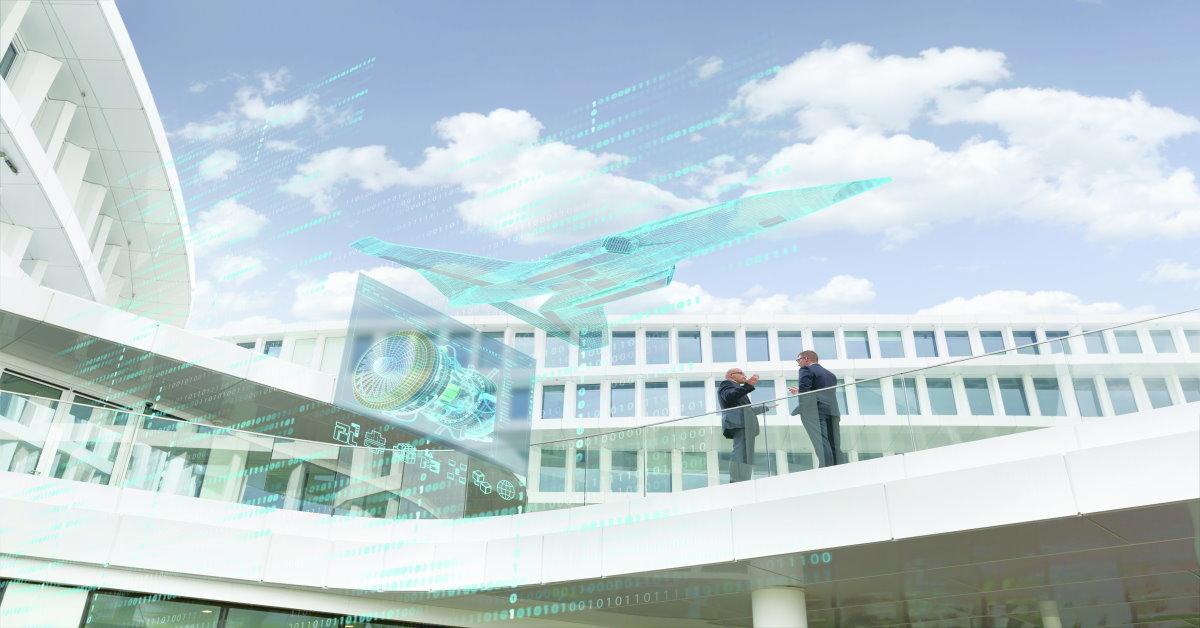
Executive summary
Proving airworthiness can be frustrating. Just ask any organization that must do so regularly. Locating and providing proof their products will perform in accordance with standards, rules and laws in various regions is a daunting task. In the aerospace industry, safety is everything and every rule and design requirement is based on the possibility of what can or has gone wrong. These rules exist to prevent death, injuries, crashes and any number of catastrophic incidents. Therefore, there are rigorous standards in place to ensure anything that can take off can also land safely.
Everything begins and ends with airworthiness
Airworthiness touches everything, including manufacturing, quality and the entire supply chain. The seemingly endless, fundamental questions all center on safety and how to design to specification to achieve airworthiness. The engineers must show the airplane meets design criteria, demonstrate the strength of the structure, and prove it has the handling and stability needed to be airworthy. These standards are met by demonstrating compliance, such as proof by design, analysis, simulation, test and ultimate verification by the applicable government agency, which in the United States is the Federal Aviation Administration (FAA). The process of aircraft certification can be overwhelming simply because many organizations neglect to take proactive steps to make it less so. Meanwhile, costs associated with increasingly complicated certification are equaling or exceeding the costs of development. Imagine spending nearly 50 percent of your cost of development and production to prove the product is safe and will work. Airworthiness certification should be a parallel activity from design through production, not a separate one, and it should not wait until the end of the design phase. Unfortunately, many organizations tend to put fulfilling airworthiness requirements into a separate activity and lose sight that it's loaded into every aspect of the aircraft program.
Consider these challenges:
- Established procedures for testing have been developed over generations. However, examples such as Siemens' eAircraft (hybrid-electric aircraft) don't necessarily align with these conventional protocols. Since the certification standards continue evolving, it's essential to invest in the right testing, simulation, verification and validation tools to ensure compliance and meet any new standards
- The owner and operator have the responsibility to consistently prove the aircraft remains airworthy and certified for flight. This includes certifying those working on and operating the aircraft, such as mechanics and pilots
- Aftermarket repairs or modifications often require seeking information on the design and/or maintenance specifications. However, what if it isn't available? Aircraft are used for decades, so vital information may not be available and engineers with firsthand knowledge could have sought employment elsewhere, retired or passed away. The solution is to go backward, which can be a laborious challenge. Sometimes the only other airplanes available for reference are ones on a military base or in a museum. This forces mechanics and engineers to figure out from scratch how to make a repair or modification work. Stories of cannibalizing or reverse-engineering older aircraft for parts are all too common, costly and extremely inefficient
- Original equipment manufacturers (OEMs) may want to keep some proprietary information private to capture the support market. Lack of access to data means owners, maintainers and operators may lack certain knowledge to properly fix the aircraft
Digital certification management
A comprehensive digital certification management system allows companies to manage their data and navigate the aircraft certification process with greater efficiency. Using digital certification management throughout the engineering review, test, check and equipment qualification phases proves the right disciplined processes were used and there was accountability and traceability throughout the lifecycle.1 Digitalization is growing exponentially in the manufacturing and production process and is a key pillar in the certification and verification process, too. Due to the volume and type of data required to support airworthiness in the initial and full rate production phases, managing that data effectively is a must. But where's the data? It could be on a shared drive, local computer desktop or even on a piece of paper in a desk halfway around the world. Compiling and collecting technical data by searching files and tracking down engineers and designers can eat up tens of thousands of work hours, driving up costs and delaying product releases and maintenance activities. Storing documents in a file in someone's desk doesn't cut it anymore, especially since it could be in many desks across multiple company and supplier sites.
- Digital certification management solves one of the issues customers face – the need to scrounge for materials and compile technical documentation at the end of the process. SharePoint document management software and Excel spreadsheet software can house data, but they can't be used to manage the verification process like a digital certification management solution can
- Digital certification management not only provides the opportunity to save time and money, but it reduces the possibility of bad publicity, such as when fleets are grounded. A reliable digital certification management system has a record to prove the aircraft met airworthiness requirements and can be used to trace back who made the part, if it was analyzed and who signed off on the approvals
- In certification, there's multiple data types. It's crucial to keep track of the original manufacturing plans, specs, drawings, materials and standard hardware as repairs and maintenance parts may not be in the original design. The number of variants can become daunting as the use of one nonoriginal part alters what can be used going forward Integrated digital program management
If almost half of the cost of development and production programs are spent on validating the product's safety and reliability, companies will need a comprehensive, integrated digital program management system to reduce costs and remain competitive. Although it is difficult enough even if all goes according to plan, problems in engineering production and throughout the process will occur. This exacerbates the impact on safety. Amid the safety concerns and headaches associated with potentially grounding a fleet, companies and investigators can leverage the digital thread of the certification process to look back to see how it met requirements. The digital thread1 makes it easier to determine who made the affected parts and if they were designed, analyzed and/or tested correctly.
- Integrated digital program management ensures that searching and traceability in reporting is tailored to all the disciplines of the airworthiness community. Technical publications, parts lists, assembly and maintenance instructions and all products that go out to the field for regular service or major repairs are ensured to be up-to-date
- Integrated digital management keeps the latest iterations and changes available and allows rotating crews over decades of managing the care of an aircraft to ensure the right parts align with those currently in use
One step in streamlining airworthiness certification is implementing integrated program planning2 (IPP), which allows manufacturers to manage and link requirements and define, plan and schedule numerous work breakdown structures (WBS). If you design an aircraft, what are the processes for designing and building it? What are the requirements? What kind of tests will need to be conducted or have been conducted? IPP links back to the customer's specifications and the governing airworthiness authority. It ensures everyone throughout the product lifecycle is checking off the steps to satisfy requirements, including tests and simulations, manufacturing, inspection, usability, documentation and maintenance. Adopting IPP can also help win bids. If selected, managing the process is more efficient with fewer chances for incurring overruns and costly delays. Aircraft certification data is also more readily available and easier to locate—the right versions of the right iteration keeps the process flowing smoothly. This integrated digitalized level of planning brings all disciplines together, breaking down silos and reducing extensive searches for information, all of which leads to a comprehensive environment used to prove airworthiness.
Continuing airworthiness
The aftermarket can be expensive. Owners and operators of aircraft have an entire supply chain that supports maintenance. However, what happens when a supplier goes out of business and is not making the parts that need to be replaced? Manufacturers can use a digital certification management system to consider an aircraft's long-term viability. Whether it's the manufacturer or owner-operator maintaining the aircraft, they must know how to realistically maintain it for decades despite likely supply chain changes. It's not uncommon for companies and military depots to spend thousands, sometimes millions of dollars, delivering repair parts only to find they don't work. Then they must spend more money trying to reverse-engineer it while the aircraft remains out of service. Also, some structural parts on planes flying beyond their expected life limits weren't designed to be interchangeable or even replaced, especially with respect to full sized hole and fastener patterns. Bottom line: Even though OEM personnel and those operating the aircraft change over time, all this information must be kept straight. The aerospace industry should continue to adopt and advance condition-based and predictive maintenance methods to minimize the cost of owning and operating aircraft, reduce downtime and improve ongoing airworthiness initiatives. Unfortunately, with the advancements in technology and use of antiquated and increasingly unreliable methods to track reliability, this results in more downtime due to unnecessary maintenance, which not only increases costs, but more importantly can put the safety of the aircraft at risk.
Managing the impact of change
An aircraft's design and safety are like a house of cards. If you change one thing or move one piece, it can impact hundreds or thousands of other things. Aerospace maintenance and repairs likely won't occur in a single location and a spreadsheet is ineffective at recording all the changes. It can't provide an impact and root-cause analysis. Seventy-to-80 percent of the total cost of ownership of an aircraft is in the maintenance burden so accessing correct information is critical. By reducing or optimizing maintenance, this lessens the burden while increasing aircraft availability. Maintenance has become such a significant, long-term investment that manufacturers are starting to make it part of the acquisition package. This has opened access to data they can use for future design and development. Identifying all the risks are critical, especially as aerospace systems continue growing in complexity. Manual processes are becoming obsolete as the challenge of managing and tracing the relationships among millions of components becomes impractical outside of a model-based systems engineering (MBSE) environment. Many times, aircraft manufacturers and maintainers can substitute original hardware items or standard parts when availability fluctuates. Manufacturers familiar with these types of substitutions will typically develop lists of acceptable alternative parts. However, if not published correctly in the service publications or parts catalog, a mechanic may try to locate an exact replacement part while an alternate may be more readily available. Managing the airworthiness process within the digital thread enables the maintainers to enhance the verification and validation processes to ensure safety and reliability, such as:
- Tracking modifications
- Keeping a record of suitable parts, but not original parts, being used
- Conducting predictive maintenance and troubleshooting issues effectively
- Closing the loop between designed reliability and demonstrated reliability in the field
Airworthiness goes beyond the design and continues through the maintenance and repair phases. The digital thread puts every aspect of aircraft design, manufacturing, maintenance and repair in a single integrated process that can close the loop on failure reporting, analysis and corrective action system (FRACAS). This integrated digital process helps identify the predicted failure points and provides feedback to the required activities to ensure aircraft safety and reliability. With a functional digital twin3 of this system, owner-operators can take data from the assets in the field and determine if the aircraft or part is maintaining its reliability goals. If not, further analysis is conducted, and the maintenance schedule is changed.
Using big data for maintenance planning
How can maintainers use a significant amount of data from an aircraft to improve aerospace maintenance and repair procedures? Big data and Internet of Things (IoT) information can be used to identify all the data from an aircraft. But it's not a matter of taking more than 800,000 data points, giving it to data scientists and hoping they'll find the areas of impending failures. At its core, you need a model that can be used to identify, analyze and define the data. This includes external factors like weather, temperature and other environmental conditions. For example, the dry, extreme temperatures of Phoenix in the summertime will impact parts differently than frigid winter conditions in Alaska. Safety and reliability tracking are too complex for traditional manual processes. A fully integrated digital enterprise solution ensures aerospace companies can use digital tools to develop their aircraft systems and predict the associated risks. The key is to link everything in design and development to predictive maintenance, verification and validation.
Conclusion
A major safety crisis is potentially emerging as two paths converge:
- Many experienced engineers have left or are getting close to retirement. Meanwhile, the upcoming maintainers don't yet have the experience or intimate knowledge of the platforms of the more seasoned artisans
- The number of major disciplines is increasing as aircraft are becoming more complex, thereby pushing the demands for an integrated environment
Although manufacturers and owner-operators are using digital tools when designing, building and maintaining aircraft, they're just not using it for airworthiness. Digital certification managements is both a tool and a process that can help maintain airworthiness, ensuring continuous safety and reliability. As aircraft continue to increase in complexity and airworthiness rules evolve, manufacturers must use the best and most comprehensive tools to demonstrate they are complying with all the standards, rules and regulations that are in place.
References
1. Reimer, Dave, "How the digital thread transforms verification management," 2017. https://community.plm.automation.siemens.com/t5/Digital-Transformations/How-the-digital-thread-transforms-verification-management/ba-p/431699
2. Siemens Digital Industries Software, Integrated program planning and execution https://www.plm.automation.siemens.com/global/en/industries/aerospace-defense/integrated-program-planning-execution.html
3. Siemens Digital Industries Software, Digital twin https://www.plm.automation.siemens.com/global/en/our-story/glossary/digital-twin/24465
About Siemens Digital Industries Software
Siemens Digital Industries Software, a business unit of Siemens Digital Industries, is a leading global provider of software solutions to drive the digital transformation of industry, creating new opportunities for manufacturers to realize innovation. With headquarters in Plano, Texas, and over 140,000 customers worldwide, we work with companies of all sizes to transform the way ideas come to life, the way products are realized, and the way products and assets in operation are used and understood. For more information on our products and services, visit siemens.com/plm.