Starting Small: Can Hydrogen Propulsion Grow Out Of Its Initial Niche?
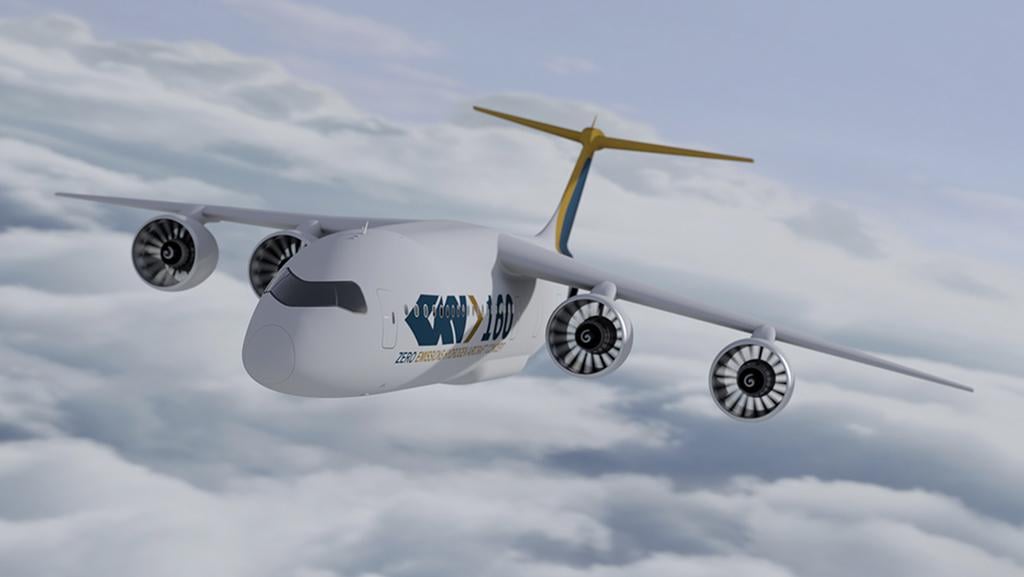
GKN developed the concept for a 160-seat airline to show the scaling potential of the H2Gear powertrain.
Credit: GKN Aerospace Concept
When Universal Hydrogen closed its doors in June after failing to secure more funding, it raised questions about the viability of introducing zero-emission hydrogen propulsion to commercial aviation by first retrofitting regional turboprops. Others have rallied in defense of the strategy to start...
Starting Small: Can Hydrogen Propulsion Grow Out Of Its Initial Niche? is part of our Aviation Week & Space Technology - Inside MRO and AWIN subscriptions.
Subscribe now to read this content, plus receive full coverage of what's next in technology from the experts trusted by the commercial aircraft MRO community.
Already a subscriber to AWST or an AWIN customer? Log in with your existing email and password.