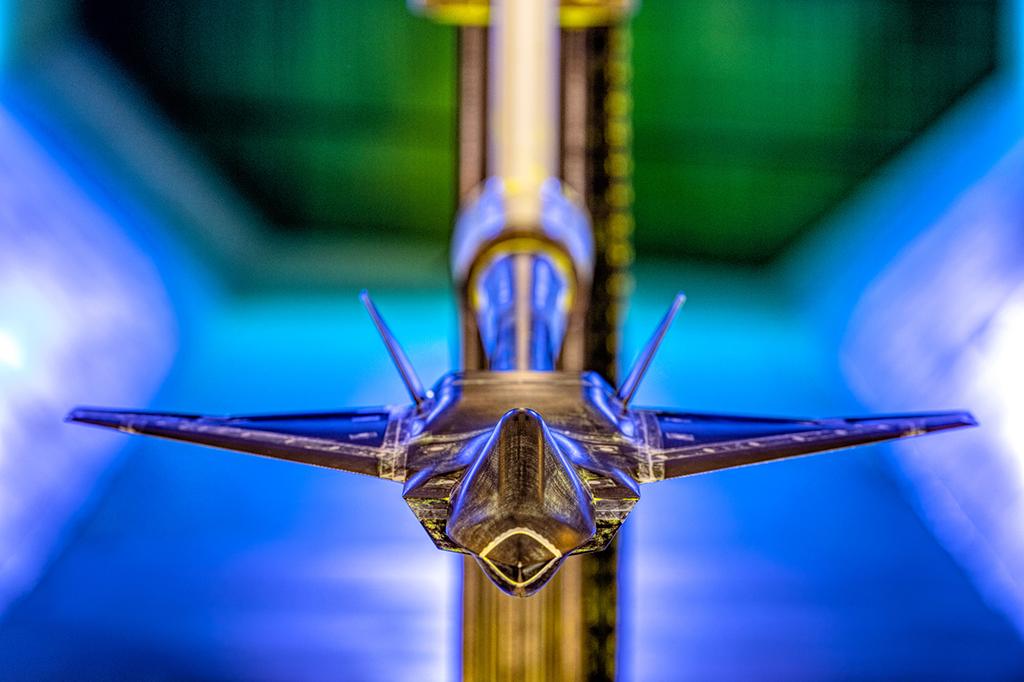
The UK’s Tempest program is leveraging a range of digital design technologies as it seeks to bring a so-called sixth-generation fighter into service. This wind-tunnel model is itself a digital product—manufactured using 3D printing—and was designed and tested in a digital environment before it ever existed in the physical world. This physical model was tested in a wind tunnel at BAE Systems’ site in Warton, England. Data from the trials will feed in to later iterations of the aircraft’s final shape.

Although this image looks at first glance to be a digital illustration, it is in fact a photograph of one of the Tempest program’s wind-tunnel models. The coloration is the result of a technique called surface oil flow visualization, in which fluorescent powder is mixed with either oil or kerosene—depending on the airspeed during the relevant phase of wind-tunnel testing—that is applied to the model beforehand. Following the test, the model is illuminated with ultraviolet light, with the resultant markings helping design teams understand flow separation and determine the transition point between laminar and turbulent flow.

As the use of digital technologies expands, both in aircraft design and onboard functionality, new concepts of operation are beginning to emerge. One area of active investigation involves supplementing the capability of the pilot with a series of digital assistants. BAE Systems, in partnership with small businesses and academia, has been looking at technologies such as a “wearable cockpit”— a means of piloting an aircraft, configurable to the individual, using augmented and virtual reality technology developed primarily for the video game industry—and at a series of artificial intelligence (AI)-enabled tools that could take on some of the pilot’s workload. These may one day exist as an avatar that might be visible in an aircraft cockpit, and capable of interacting with a human pilot.

Other future-fighter programs are investigating novel digital cockpit concepts. The pan-European New-Generation Fighter (NGF) project entered a preliminary development phase following signing of a concept study contract in January 2019. Last December, Spain joined the Franco-German program, which is part of an overarching Future Combat Air System incorporating current fighter aircraft, unmanned systems, cruise missiles and satellites. The program also includes a network that extends data-sharing and other connectivity and integration with land and maritime domains. The amount of information available to the pilot will rise substantially once such an operational concept becomes a reality, so new ways of managing data will be needed. The NGF concept study includes research work on redesigning the human-machine interface and examining how AI can be incorporated into next-generation cockpit operations.
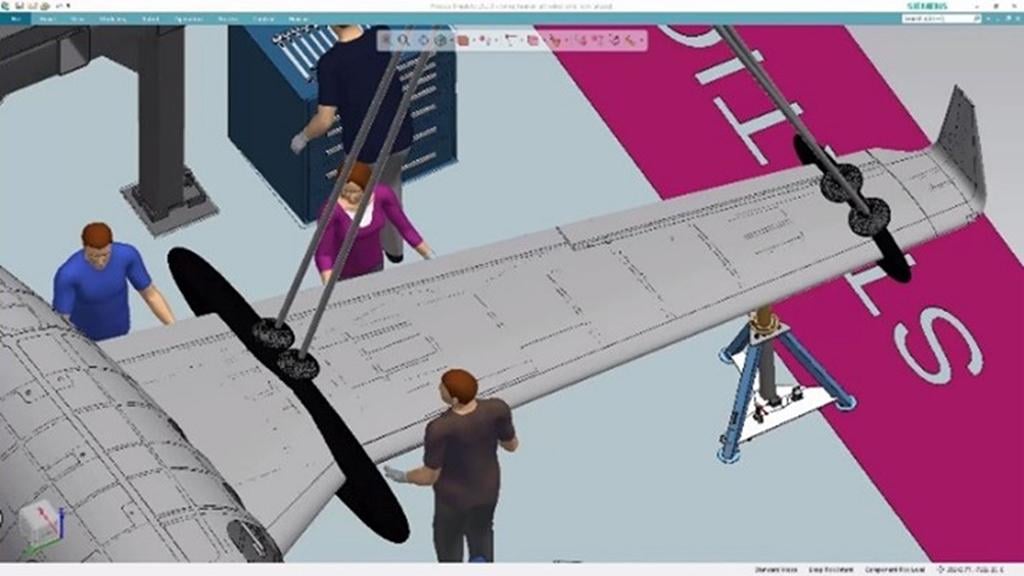
The concept of a digital twin has been around for long enough to now be a deeply embedded part of advanced design programs. By creating a virtual simulacrum of the project, design elements and programmatic changes can be implemented quickly and with limited cost, tested for viability in the virtual environment and only brought to the physical manufacturing stage if computer-run testing confirms their utility and viability. The concept also allows developers to “shift left” which means introducing manufacturing and maintenance considerations at a far earlier stage of the program than possible with traditional development. In this way, late design changes can be implemented without imposing lengthy or costly delays, and the customer will receive a more capable, up-to-date product. As pictured, the digital twin of a production process is being used to simulate the factory floor, ensuring viability of proposed production methods before physical construction begins.
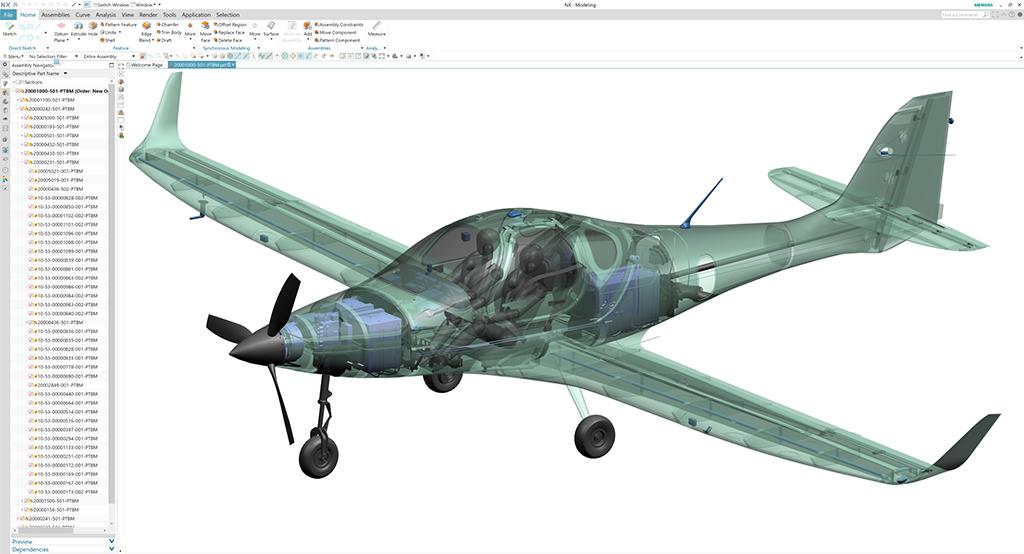
Agile product development processes can enhance program management and enable projects to proceed at a much greater pace by interleaving previously separate processes. Additionally, the concept of sprint development—breaking each program into smaller, more manageable chunks that can be worked through rapidly—can further streamline the process. Digital tools such as the NX software suite developed by Siemens (and in use by clients including Bye Aerospace Inc., whose model is pictured), allow for the incorporation of sprints and other accelerations to the design, simulation and manufacturing phases.

One obvious way in which digital technologies are enhancing design projects is in automating the process by which design changes are mapped and managed across every phase. Siemens is offering capabilities that allow design teams to automatically track changes made in one domain of the program and ensure they are applied throughout development. The system links the program’s different elements so that a change made to a CAD model is tracked digitally to ensure it is applied to test articles, test planning and all program deliverables. If a change needs to be reversed, or an enhancement is later shown to be detrimental to outcomes, the system ensures amendments are applied to all stages of the program.

Mechanical computer-aided design (MCAD) and its electronic sibling electronic computer-aided design (ECAD) are both widely deployed across multiple industries. Managing change is vital within both, but changes in one medium will need to be tracked and implemented in the other. That requires systems capable of automatically synchronizing data across both domains, but which can also highlight those changes to designers and other project workers in a way that aids quick and easy understanding without overburdening them with too much information. As pictured, two Siemens programs—Capital and NX—work together so that changes are presented clearly to an electrical engineer for review.

Examples of change management across digital and physical domains have already begun to migrate from research situations and onto production lines. At Dassault Aviation’s plant in Biarritz in southwest France, technical staff working on the Dassault Falcon 6X fuselage are able to view assembly instructions on a virtual-reality headset. Data are extracted from the digital twin mockup developed by Dassault for the 6X. The mockup was created using the 3Dexperience platform, a suite of software tools developed by Dassault Systems. The company has been at the forefront of CAD and digital project management software development since the 1980s, when it released the first iteration of its computer-aided 3D interactive application suite of applications, which the company says, is in use by over 220,000 customers in more than 140 countries across multiple industries.

Virtual-reality or augmented-reality headsets are proving increasingly popular across different elements of aircraft design, production and maintenance. As pictured, a mechanic working at Dassault Aviation’s military support department in Merignac, in southwest France, carries out maintenance on a Rafale fighter while viewing instructions on a headset. (The instructions are only visible in the headset but have been added to the image to visually explain the concept.) Deployment of this tool followed a 2018 test program carried out by France’s defense procurement agency at two air bases, which involved maintainers carrying out procedures on the Rafale jets and their Mk. 16 ejection seats. As well as projecting instructions and information, the headsets allow maintainers to contact back-office experts for real-time diagnosis and advice during complex procedures.

The first fruits of a collaboration among more than 40 British companies, and further deepening an extended collaboration between the UK’s defense industry and the motorsport sector, the factory of the future opened last year by BAE Systems at its Warton site is exploring new ways humans and machines can work together in aviation design programs. Technologies described as “cobotic and flexible robotic” are intended to eliminate the use of heavy cabled tooling and will allow the facility to quickly transition from producing one platform or product to another.

We tend to think of digital technology as involving miniaturization and virtualization—tools that exist in the digital ether or are accessed through ever-smaller networked devices. But there are some areas where digital tools are vital parts of huge new infrastructure projects. Rolls-Royce’s Testbed 80 was opened in Derby, England this year, and the company says the £90 million ($125 million) facility is the world’s largest indoor aerospace testbed. Monitoring of engines under test involves taking some 200,000 data points per second, across more than 10,000 parameters, while an X-ray machine records 30 images every second.
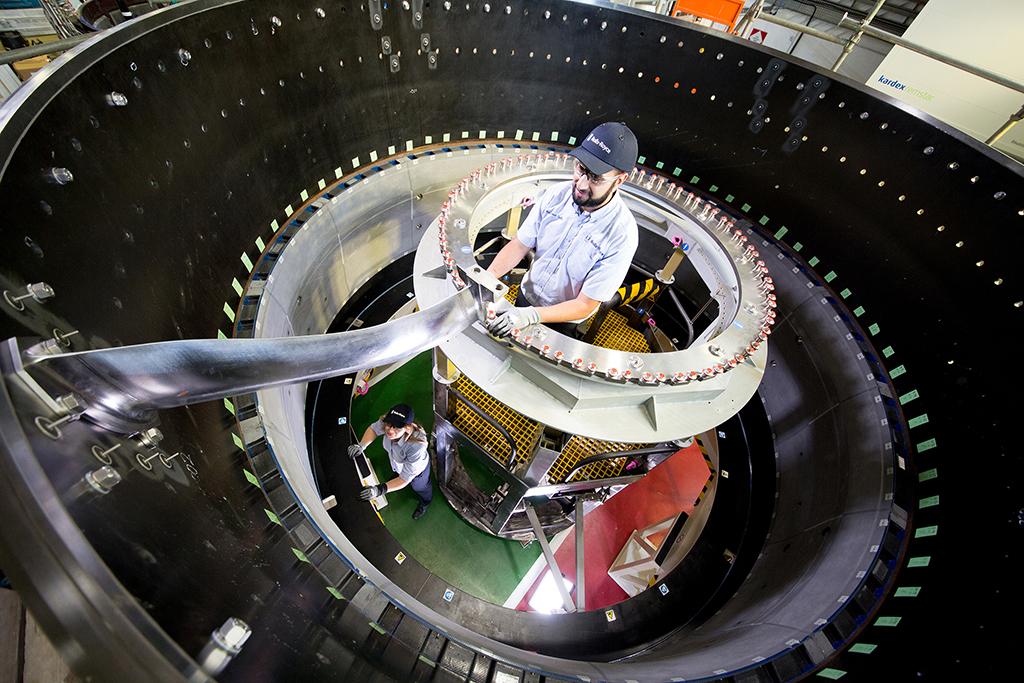
The huge investment in Testbed 80 has been made necessary, in part, by Rolls-Royce’s UltraFan program. A demonstrator unit of the new engine is being built at present and is expected to begin tests at Testbed 80 next year. Envisioned as being 25% more efficient than the first Trent engine, parts of the development program have already set aerospace records: during tests near Berlin, the UltraFan power gearbox reached 64 megawatts in August. The company has also announced it is developing a range of miniature maintenance, inspection and repair tools, including “snake robots” to work inside engines, and automated repair technology to enable repairs of components that at present are scrapped, as part of the UltraFan project.
As aircraft become more connected, with their subsystems increasingly expected to be accessible not just to pilots and others on board but also to analysts, technicians and operational support staff working in other locations, the role of digital technologies is becoming ever more fundamental. Those technologies are not just changing the way aircraft operate; they are influencing every aspect of aircraft design. That includes optimizing components for weight and efficiency—producing shapes that would not be possible to fabricate without using digital design and additive manufacturing technologies—integrating different elements of the build process in ways that enable designers to revise the physical product as well as supporting documentation and more. As these technologies mature, new areas will open up to exploration and research, with ideas that seem novel today—such as holographic digital assistants for the pilots of the future—likely to take their place in future programs, much as digital twins and augmented-reality maintenance systems have transitioned from being cool science projects a few years ago to essential frontline tools today.
Comments