Composites May Be Key as Aircraft Propellers Become More Complex

Propeller manufacturers are increasingly turning to composites as new designs incorporating larger numbers of blades emerge for both new products and retrofit.
“Hartzell has decided to focus exclusively on [the development of] composite blades and spinners at this point in time,” says J.J. Frigge, president of Hartzell Propeller in Piqua, Ohio. “Composite-blade propellers can enable a higher blade count than aluminum-blade propellers due to the lower weight and corresponding lower moment of inertia.”
As he explains, a higher blade count can enhance performance, especially on higher-horsepower aircraft, while in many situations, low-speed performance—takeoff and climb—is increased significantly.
Composite blades, says Frigge, also offer a maintenance advantage. While time between overhauls for carbon-fiber and aluminum propellers is typically the same, composites have the advantage of being restored to factory-new shape between overhauls. “With aluminum blades, material removed during overhaul cannot be restored,” he notes. “This reduces the useful life of aluminum blades to three to four overhauls. But carbon-fiber blades offer unlimited restoration.”
Hartzell’s carbon-fiber blades incorporate a nickel-cobalt, electroformed leading edge, which Frigge says is harder than aluminum, greatly reducing water and foreign object damage.
He adds that the demand for propeller upgrade packages is growing. For example, he says Hartzell is offering five-blade composite propeller systems as an alternative to the heavier, four-blade aluminum systems on the Pilatus PC-12, King Air 200 and 350, Piper Meridian and the entire Daher TBM series.
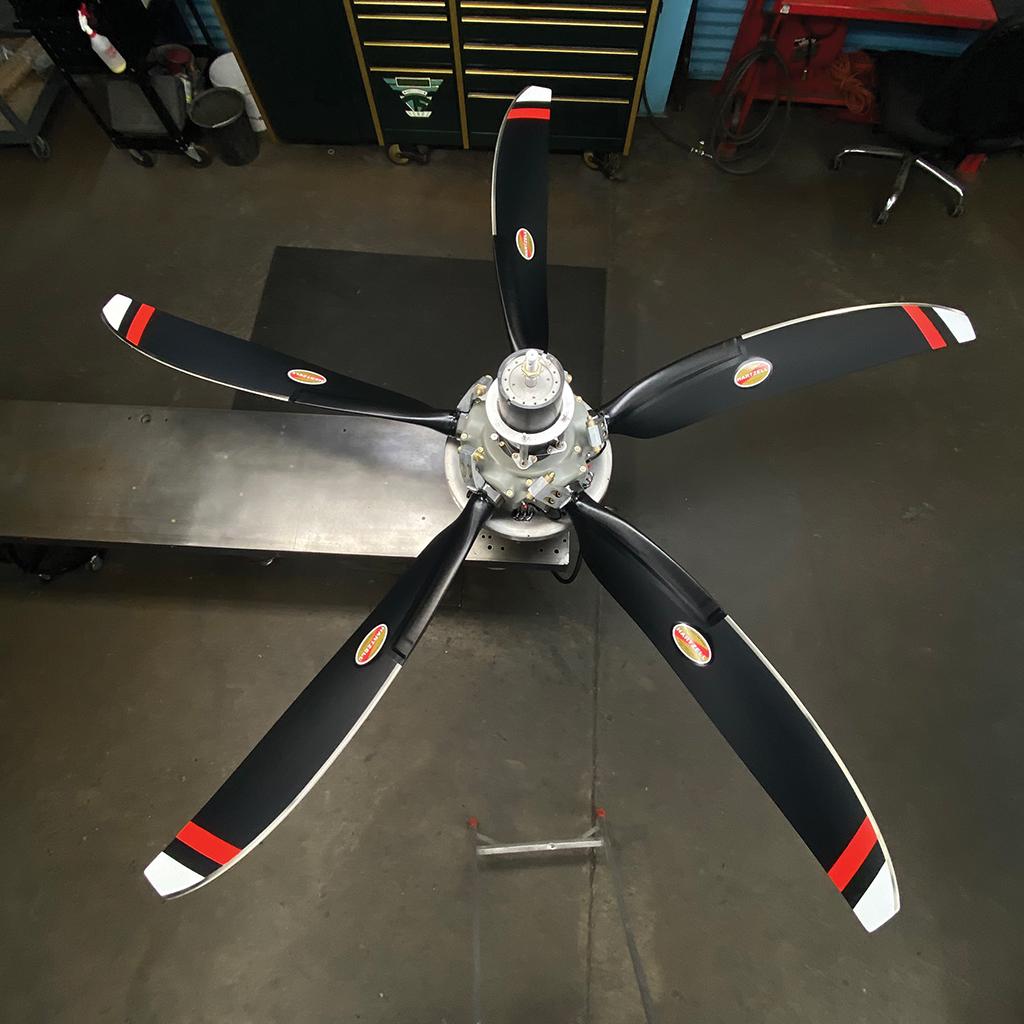
Frigge states that lighter-weight propellers will be critical for electrically driven aircraft to offset added battery weight. “Electric propulsion will be a huge potential growth area for decades to come,” he says. “We are talking with numerous companies engaged in electric propulsion projects about how we can help them. And most of them want composite blades.”
“Increasing the number of blades allows more traction for a given propeller diameter,” says Jean-Francois Chanut, general manager of propeller systems and president at Ratier-Figeac/Collins Aerospace Mechanical Systems in France. “Using composite or new, advanced materials are key to reduce the overall weight of the components, such as the blades.”
In that regard, the OEM has developed and produced the NP2000 propeller, an eight-blade composite system used on the Airbus A400M, Lockheed Martin C-130H and Northrop Grumman E-2C/D Hawkeye. Collins Aerospace markets its propeller products under the Hamilton Sundstrand and Ratier-Figeac brands.
Chanut also notes that the combination of new, lighter materials and advanced aerodynamics optimizes the weight and propulsion efficiency of the propeller system—reducing the overall energy required for a given flight profile. “Whether the energy is from fuel, hydrogen or electricity, this efficiency translates directly into fewer greenhouse gas emissions, which is what we are targeting,” he says.
At Wichita-headquartered McCauley Propeller Systems, most development efforts are focusing on blades, hubs and actuating components, according to John Dandurand, McCauley’s general manager. “As the most complex components of the propeller system, these areas hold the largest opportunity to improve the key aspects of performance, noise, [time between overhauls] and weight,” he points out.
Dandurand says there is increasing demand for composites, mostly applied to blades, which comprise the majority of the weight of multiblade systems. In addition, he notes that composite blades are not limited by forging constraints and therefore enable greater flexibility in the design process.
“Composite propeller blades can be produced from a variety of materials, ranging from legacy wood and fiberglass construction up to carbon-fiber and resin designs,” he says. “This range of material options and properties can be adapted to meet specific operating needs.”
Nonetheless, Dandurand does not see conventional aluminum propellers going away anytime soon. “They continue to be a popular choice, and for many operators provide the right mix between performance and price that will continue to cement aluminum propellers as a mainstay for years to come,” he says.
While carbon-fiber composites are more costly to produce than aluminum props, the cost differential has narrowed some, Dandurand adds. “That is likely to continue as material costs and manufacturing methods benefit through increased volumes and scalability,” he remarks.
Jonathan Chestney, technical director at Dowty Propellers, says that since the Brockworth, England-based manufacturer introduced composite blades for the Saab 340 airliner in the early 1980s, fibers, resins and manufacturing techniques have evolved. Composites have remained a “material of choice” for blades, he says.
“Composites bring multiple benefits to blades,” says Chestney. “The ability to locate fibers only where strength is required ensures that weight is minimized, on top of the excellent strength-to-weight ratio of carbon composites. Repairs can be additive, and fatigue performance is excellent, maximizing life.”
Chestney agrees that cost challenges remain—not just those involving the composite materials but also the manufacturing techniques. He stresses that costs are also rising for high-performance metals. “The ever-increasing recognition of the environmental and health effects of some of the established metal treatments risk higher costs,” he points out. “Careful consideration of all factors is still necessary in material selection as the goalposts continue to move.”
Steel and aluminum alloys continue to remain prevalent in today’s propeller designs, Chestney says, but the “derivatives are changing” as aircraft needs evolve. Cost, weight and sustainability demands, he says, may push design decisions in any one of multiple directions.
“The value of lower weight is seen to be increasing as complexity is added to propulsion systems,” Chestney explains. “This paves the way for more exotic materials to be employed that would previously have been cost-prohibitive.”
At the same time, advances in manufacturing techniques—particularly additive—are ensuring that “structural optimization can be enhanced without the penalty implied by subtractive machining techniques,” he notes.
Maximizing the performance of propellers requires “consideration of all parts of the propeller and its integration” with the aircraft, Chestney says. However, he stresses that the blades have the greatest influence and therefore demand the greatest attention. Still, he says maximum benefit can only be achieved by focusing on all aspects. For example, enhancements in hub design can reduce the spinner diameter, he says, which is potentially important to match aerodynamically with a smaller nacelle made possible with electric drive.
“The blade, both in terms of aerodynamic profile and construction, is the single most important driver, and emphasis is on achieving the best possible aerodynamic shape that is also manufacturable,” Chestney says. “Dowty has its own family of aerofoil shapes that achieve maximum efficiency with shapes that are manufacturable with fiber-reinforced composites. Recent research has focused on ensuring that this efficiency is maintained within the proposed aircraft installation, utilizing the latest computational fluid dynamics techniques.”
Along with composites, Dowty has addressed erosion issues, an area in which work continues. For instance, it has applied a polyurethane coating which Chestney says has “dramatically increased” erosion resistance. “Dowty has been working with UK manufacturers on proprietary additives, such as nanoparticles, which can enhance erosion resistance, while retaining other key properties of the base materials,” he notes.
One of the latest developments involving composite propeller blades was focused on NASA’s Mars Ingenuity helicopter. Developed by Arlington, Virginia-based AeroVironment, its blade design had to address lift in the Martian atmosphere, which is considerably less dense than Earth’s. Ingenuity uses two counter-rotating rotors, each driving a twin-blade propeller. Weight per blade is just 1 oz.
Ben Pipenberg, AeroVironment’s aeromechanical engineer and lead engineer on the Ingenuity program, points out that atmospheric density on the surface of Mars is about equivalent to 100,000 ft. above sea level on Earth. That creates issues for stability and control, because the aerodynamic damping is also reduced.
Another issue is the speed of sound on Mars, which is about 30% lower than on Earth. “The reduced speed of sound on Mars means we run into compressibility issues, such as drag divergence, out of the tips of the rotor, at a lower [revolutions per minute (RPM)] than we would otherwise,” Pipenberg says. “Ingenuity’s blades are designed to operate at a tip Mach number of 0.76, so our maximum RPM is limited to operation below that speed. The result is that we needed large rotors that spin fairly fast while also being extremely light.”
Surviving the thermal cycles—between -125C (-193F) and 115C (239F)—as well as ultraviolet light and Martian dust also needed to be accounted for in material selection and design.
“One of the less apparent problems we ran into is that launching a helicopter on a rocket is actually really challenging,” Pipenberg says. “Almost all of the load-limiting cases Ingenuity encountered are due to the vibration experienced right after launch and the forces that are much higher than the helicopter experiences during flight on the surface of Mars. Designing the rotor blades and hubs to take those types of loads into account while still remaining light enough to fly was a top priority.”
The rotor blades on Ingenuity, Pipenberg explains, are fabricated from several types of carbon-fiber composites molded over a machined Rohacell foam core. The blade design uses high-modulus and unidirectional spar caps to react to bending loads and provide a very high first-flap frequency required for crisp control response. A very thin spread-tow skin—the carbon-fiber upper and lower surfaces of each blade’s solid foam core—are less than 0.002 in. thick. The spread-tow-style fabric is thinner and lighter than a standard weave. The materials are pre-pregged with a cyanate ester resin from Toray Advanced Composites, specifically designed for extreme environments like those found in space and on Mars.
“There were a few fabrication processes we developed specifically for Ingenuity, but for the most part we relied on materials which already have a proven spaceflight heritage,” Pipenberg says. “All of the composite materials we used are readily available on the commercial market.”
Although the carbon-fiber materials are fairly similar to those normally used for terrestrial propeller blades, they are, Pipenberg notes, much thinner laminates than standard woven materials. “The cyanate ester resin matrix is more unusual,” he explains. “They are specifically formulated to survive the harsh environment in space. They resist micro-cracking and UV degradation, have low water absorption and outgassing and can handle extreme temperatures without issue.”
The obvious question, then, is to what extent the technology employed by AeroVironment to design Ingenuity’s propeller blades for the harsh Martian environment is transferable to fixed- and rotary-wing aircraft on Earth.
“I think that some of the materials and fabrication techniques could definitely be useful for rotors and propellers on Earth,” Pipenberg ventures. “The high-modulus carbon-fiber materials and spread-tow skins can result in extremely lightweight components with excellent mechanical properties.”
According to Artie D’Onofrio, president of New England Propeller Service in East Haddam, Connecticut, more propeller OEMs are migrating toward composite blades, as the weight-savings and performance efficiencies of multiple-blade designs become apparent. Still, he cautions that at least for now, composite propellers come with their own maintenance issues.
“We’re talking about a new type of propeller blade that most mechanics have never had an opportunity to repair,” he notes. “As the OEMs use more composites, there will be a huge learning curve among the mechanics, which, in fact, is going on right now. For example, they will have to learn what is an acceptable state of repair and what is not, and once this is determined, how to repair it.”
The other major issue, D’Onofrio says, involves the fact that composite repair is more time-consuming than aluminum repair, especially in cases of debonding. For example, if there is a nick in an aluminum propeller’s leading edge, all the mechanic has to do is use a file and other tools to smooth out the edge. This can usually be done in the field and does not take long.
“Similar damage to a composite blade may require removal for repair at an outside shop or having to order special materials,” D’Onofrio points out. “Also, a lot of composite materials and bonding chemicals have a limited shelf life, so the repair facility may not have the inventory on hand to do the repairs.”
Looking ahead, D’Onofrio expects that composites will continue to make inroads in propeller-blade designs. “There will be a new revolution in propeller technology, especially if more aircraft are electrically driven,” he says. “The electrical propulsion systems under development today will add weight, which means that lighter propellers will have to be used—even lighter than we have today.”