Customized, Titanium Presses With Closed-Loop Technology
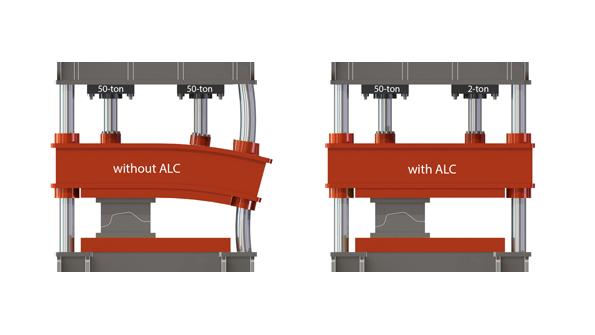
Credit: BECKWOOD PRESS
Beckwood Press Co. will supply Ducommun’s Parsons, Kansas, facility with two new highly customized presses for hot-forming titanium, one with closed-loop monitoring. The first new 200-ton press will hot-form titanium parts for several aircraft, including the Boeing 737MAX. The press will use...
Subscription Required
This content requires a subscription to one of the Aviation Week Intelligence Network (AWIN) bundles.
Schedule a demo today to find out how you can access this content and similar content related to your area of the global aviation industry.
Already an AWIN subscriber? Login
Did you know? Aviation Week has won top honors multiple times in the Jesse H. Neal National Business Journalism Awards, the business-to-business media equivalent of the Pulitzer Prizes.