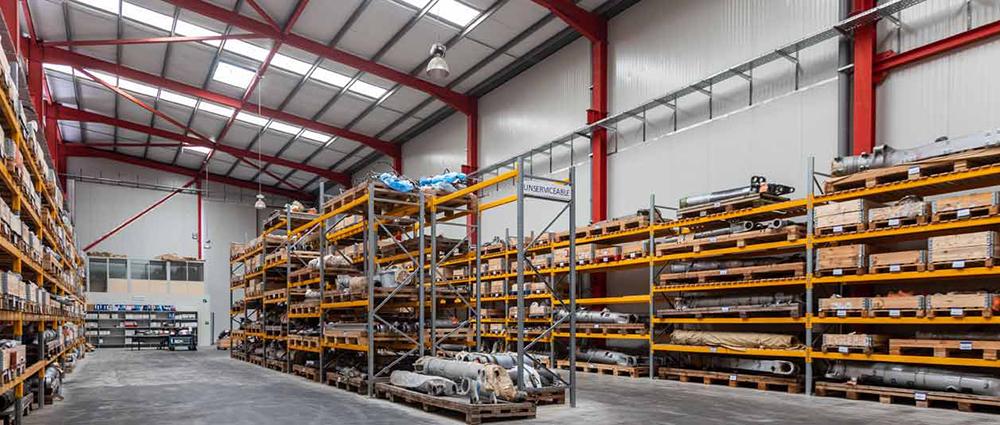
Revima has implemented new technology, equipment and capabilities to expand its service offerings.
At Aviation Week’s MRO Europe event on Oct. 18, it announced that it has deployed a predictive optimization solution to improve its supply chain operations. The software from Lokad uses probabilistic forecasting and differentiable programming, which Revima will use to reduce turnaround time for APU and landing gear repairs, as well as optimize inventory costs for spare parts.
According to Olivier Legrand, president and CEO of Revima Group, the software combines the latest artificial intelligence technology with data scientists that screen the data to provide ‘augmented intelligence’ for aviation.
“Aviation has been promised inventory optimization solutions since I started my career over three decades ago. However, every time, aviation proved too hard: too many parts, too many processes and too little volume,” says Legrand. “With Lokad, we have finally found a partner that can integrate the aviation expert knowledge of Revima’s teams right into our systems.”
Revima says the software’s forecasting capability can be applied to demand, lead time and scrap rate to cope with the high uncertainty and variability in aviation. Meanwhile, it says the software’s differentiable programming enables it to automatically extract patterns from complex supply chain processes in MRO.
At its subsidiary Revima Engine Parts Repair, located near Paris in Saint-Ouen-l’Aumône, it has devoted 20,000 ft.2 of new space to use for extended repair capabilities of turbine components, APU components and exhaust systems. The new repairs include platinum coating for aluminization diffusion coating of blades and vanes; sheet metal work for large exhaust components on CF6-80, CF6-50, PW2000 and PW4000 engines, as well as ATR 42 and 72 aircraft; and pipes and manifold systems repairs for CFM56-5A and -5B engines.
Revima Engine Parts Repair has also expanded its APU component repair capabilities to Pratt & Whitney Canada products, including APS500, APS1000, APS3200 and APS5000 models. In the coming weeks it will develop repairs for sealing parts of LEAP-1A and -1B engines.
To support these new repairs it has invested in new equipment, including robotic arc welding equipment for restoring abradable areas of cold section compressor components and hot section turbine stages; a full integrated atmospheric plasma spraying booth to spray ceramic coating; and a five-axis CNC milling machine for large parts.
“Despite two years of uncertainties, we have invested in the future in our site near Paris airports and major aviation key-players, to provide the best services to engine repair and airline maintenance shops,” says Jeremy Goossens, General Manager of Revima Engine Parts Repair.