More than the sum of the parts
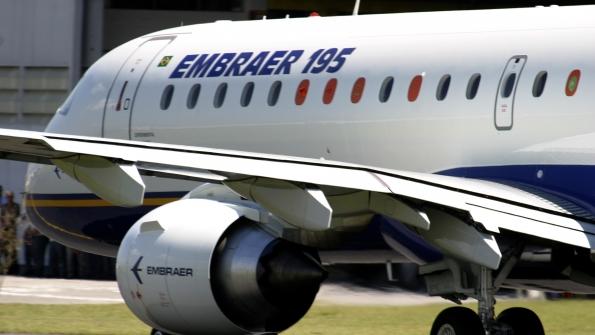
Credit: Embraer
When an airline decides to either switch or extend its aircraft fleet, it needs to ensure that it has the right amount of stock in place to support however many aircraft it is taking on. This initial provisioning can cover everything from small parts to complete spare engines, from rapidly-used...
Subscription Required
This content requires a subscription to one of the Aviation Week Intelligence Network (AWIN) bundles.
Schedule a demo today to find out how you can access this content and similar content related to your area of the global aviation industry.
Already an AWIN subscriber? Login
Did you know? Aviation Week has won top honors multiple times in the Jesse H. Neal National Business Journalism Awards, the business-to-business media equivalent of the Pulitzer Prizes.