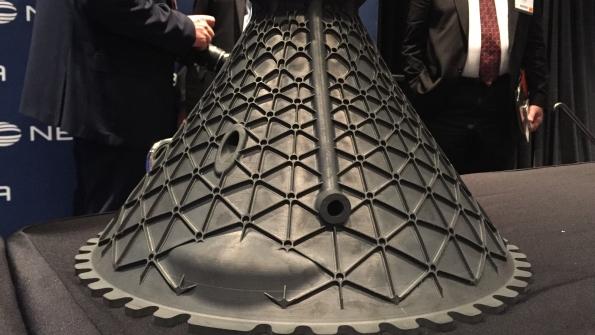
Credit: Guy Norris
The concept of printing metallic parts for aerospace applications in place of traditional forging and casting may be in its infancy, but General Electric says the coming revolution in additive manufacturing for aircraft engines is approaching quickly and on an unprecedented scale. “It is the...
Subscription Required
This content requires a subscription to one of the Aviation Week Intelligence Network (AWIN) bundles.
Schedule a demo today to find out how you can access this content and similar content related to your area of the global aviation industry.
Already an AWIN subscriber? Login
Did you know? Aviation Week has won top honors multiple times in the Jesse H. Neal National Business Journalism Awards, the business-to-business media equivalent of the Pulitzer Prizes.