New Robotic Repair Technologies At AFI KLM E&M
November 23, 2016
Vertical Engine Pits
Vertical engine pits were created within the KLM's Schiphol Airport facility to service the GEnx 1-B engine, and more will be created as needed. The construction consisted a 4x13x4 meter pit built into the concrete and took four months to complete. Overall, AFI KLM E&M services over 1,800 CFM and GE engines.

Engine Repairs
In February 2015, the Schiphol facility completed its first GE GEnx-1B “Quick Turn” engine shop visit.

Electron Beam Welding Technology
Electron Beam Welding technology (E-Beam) was developed by AFI KLM E&M to repair the bevel gear shaft forward thread, called Repair 005, and can be performed within the standard repair window - eliminating the need for a part exchange/rotable, and is available for most of the CFM56 engine family including the -5A, -5B, -5C and -7B. This technology enables repairs, therefore reducing the need to purchase new parts, and minimizes scrap material. Low heat is used so the part is only minimally distorted compared to other welding methods.

EB Welding Repair for the Compressor Discharge Pressure Seal
The repair is also available for turbine rear frame patch repair (CF6-80C2/80E), combustor inner liner aft flange replacement (CFM56), tang replacement fan mid-shaft (CF6-80C2/80E) and the compressor discharge pressure (CDP) seal F1 land replacement (CF6-80C2/80E).

Air-Plasma-Spraying Robot
In 2015, AFI KlM E&M, as part of the MRO Lab program, used virtual, offline programming applied to its air plasma spraying (APS) process, which aims to prevent damage, increase hardness and achieve certain diameters.

APS Programmed Reduced Manual Risks
Previously, the APS process was done manually, but now through the programming process, it can be set up once in 1-2 weeks. This change reduces safety risks by removing the technician from ultra-high temperatures and metal powders.

Laser-Cladding Robot
Laser cladding involves feeding powder into a laser beam and selectively applying it to a designated area. According to Martin Plantinga, AFI KLM E&M laser cladder operator and developer, one of the items that cannot be recycled is the residual dust, which is filtered and then disposed of. The additive manufacturing process possess high welding quality with low heat input, resulting in minimum shrinkage.
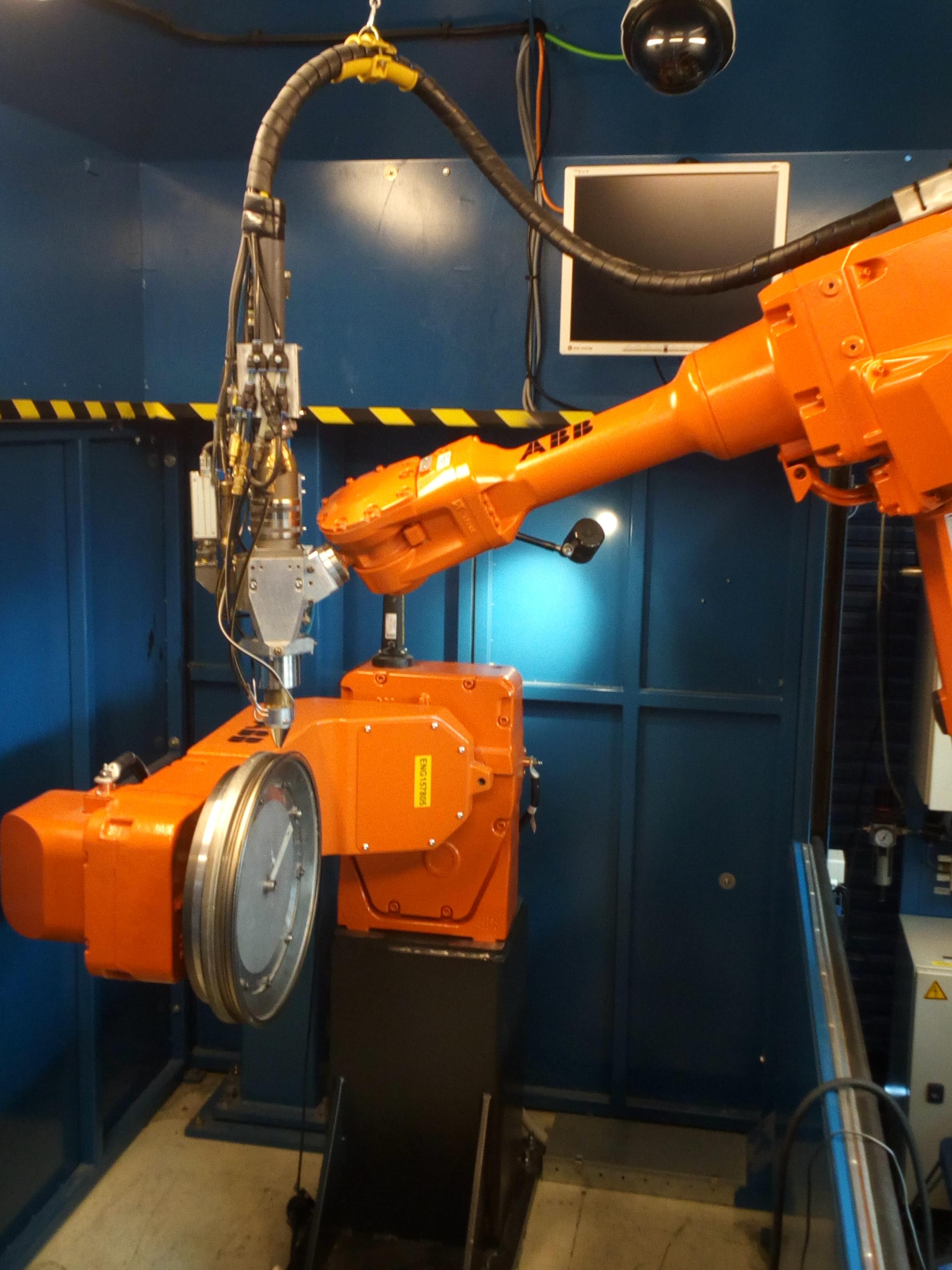
Laser Cladding 3D
The laser cladder also can be used as a metal 3-D printer, and its programming is based on 3D models. The program can run offline or outside of the work environment. The new robotic machine envelope has container walls that can slide, so the material or part can be moved from one side to the other without being exposed. The machine is powered by the Trumpf 1006D HL and is used for rail restoration of the LPT Case and several seal teeth repairs.
Inside MRO toured Air France Industries KLM Engineering and Maintenance (AFI KLM E&M) facilities at Schiphol Airport in Amsterdam. AFI KLM E&M and its MRO Lab program have developed new repair processes using robotics in the workshops and hangars to service the Airbus A380 and A350 and Boeing 787.
*This article was updated at 7:30 AM Central November 28