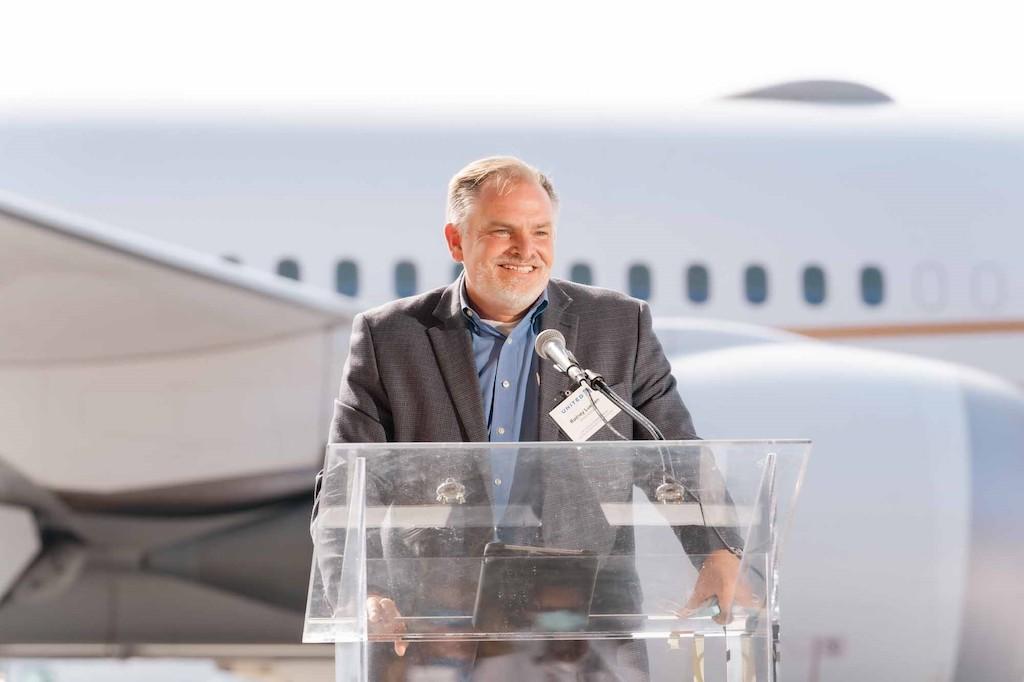
In an impromptu 10-minute interview on Dec. 8 at Los Angeles International Airport, Rodney Luetzen, United Airlines’ VP line maintenance, talked with Aviation Week Executive Editor Lee Ann Shay about the operator’s plan for the holidays and fleet growth. Luetzen officially started that role in July and previously served as managing director of line maintenance.
With the recovery underway and the fleet ramping up, how is this affecting line maintenance at United?
When we went through COVID-19, we enticed people to leave the company and take the early out program, so we lost roughly 1,500 employees through that exercise. As we turned around and started to revamp the airline, we grew quickly. That put a lot of pressure on our resources when it comes to manpower, so we quickly had to revamp our hiring process. We've hired more than 400 technicians in the past three months, so we’ve been pretty successful considering all of the competition out there for A&P technicians.
With the holiday season coming up, what kind of forward planning have you done for that?
We actually start a week before a holiday because a lot of our technicians want to take the holiday off. So for Thanksgiving, we started a week before the actual holiday to start mitigating risk for aircraft that we didn't want to have out of service during the holiday and aligning resources with the plan. We’ve been doing this for the last three or four holidays. It seems to work really well to get ahead of that wave of outages and that wave of work. Holidays are when you make your money, so you want to have as many airplanes in the air as possible and you want to want to make sure you're managing your out-of-service exposure.
United Airlines was an early adopter of digitalization and using iPads for line maintenance work. How has that affected the operation?
If you talk with technicians, they'll probably tell you it's the best thing the company's ever done for them. It gives them all the information they need at their fingertips. They can quickly identify an issue, pull up a troubleshooting procedure, identify a part, order it and in some cases the part gets delivered to the airplane. So it has streamlined their work and made them more efficient. It also has minimized our turn times. It’s a beautiful tool. We all carry it and we all embrace it. I mean, I was flying on an airplane monitoring an airplane out of service in Chicago—via mobile. That’s pretty cool.
What are the biggest challenges that you face?
Our biggest challenges is managing resources—have the right people and the right parts in the right place. As the airline has grown back, we've exposed locations to different fleet types that they maybe didn’t fly historically. So we need to make sure our parts are synched up with our flying.
This is really about aligning our growth with the fleet plan. We still need to stay conservative when it comes to cost and maintaining our CASM (cost per available seat mile) that's relatively flat as you grow the airline, but we want to make sure that we have the right infrastructure, the right hangar allocations, the right resources throughout the network. If you think about it, the growth plan is basically building another airline on top of what we have today. But we are taking advantage of what we have today, right? A lot of the resources are baked in.
As the airline ramps up this huge growth, are there things that will be changing for line maintenance?
One of our initiatives is called the line maintenance ecosystem. It's really about aligning resources in a plan so that you don't have much churn through the course of a day or an evening. You'd have to have the right people lined up to do the work. You have to have the right parts. You need the right tooling. You have an executable plan when it comes to hangars and things like that. Our initial focus is on parts. We have what's called a pre-draw setup. So if you have a planned maintenance event and you know you need a widget, you have that widget delivered to the airplane. It’s about giving our overnight staff a fighting chance to execute on the RON (remain overnight) plan.