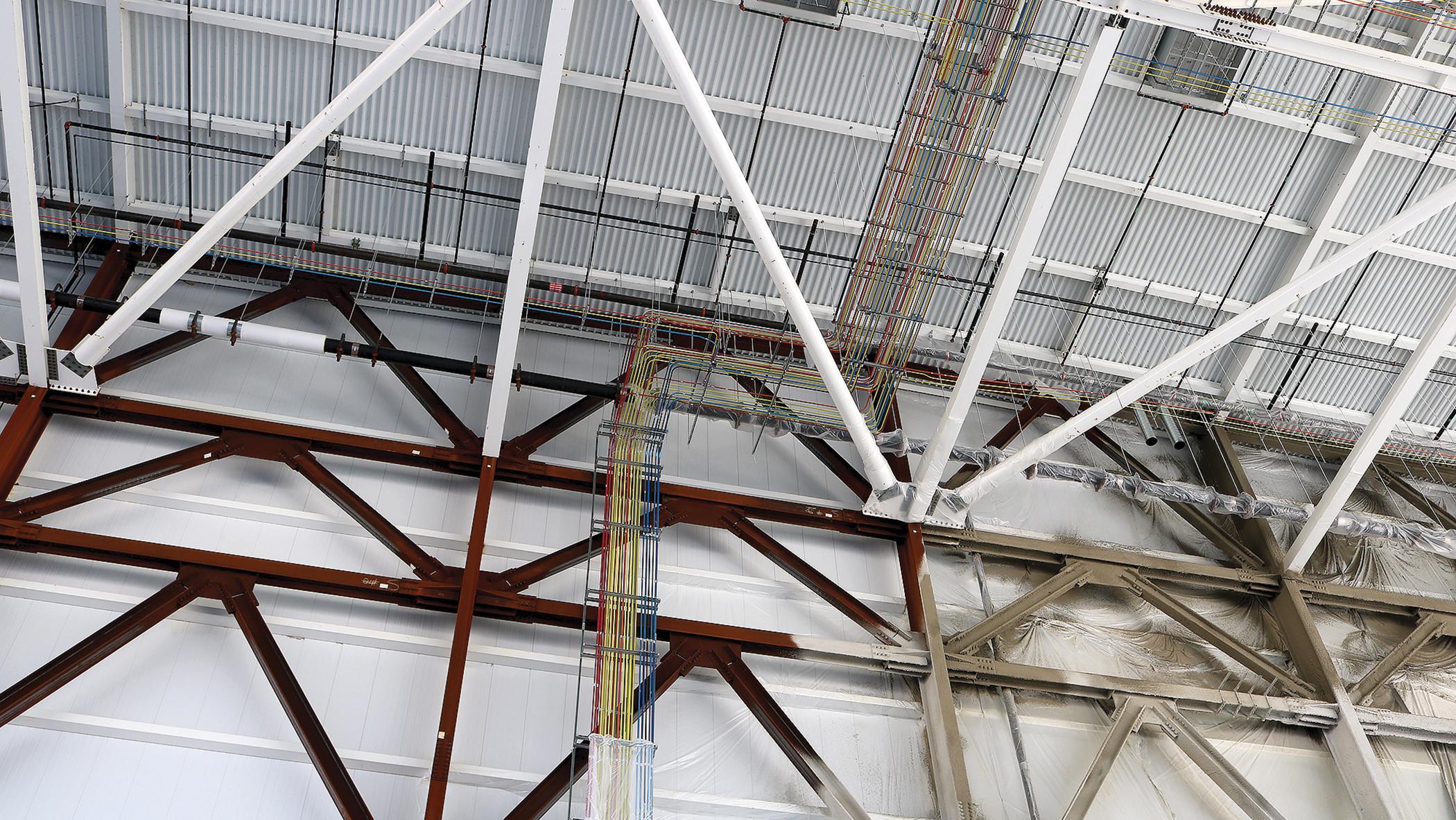
As MRO operations increasingly becoming more digitalized, modern aviation maintenance technicians (AMT) are more reliant on technology to access information and collaborate with colleagues. However, connectivity inside an aircraft hangar can be spotty, a major pitfall for AMTs attempting to communicate digitally or test GPS and satellite communication systems.
KonectaUSA, a specialist in cellular amplification systems, says the problem starts with the typical building materials used for aircraft hangars. Mike Bozyk, design engineer for KonectaUSA, says the metal construction materials in many aircraft hangars can isolate and block radio frequency (RF) transmissions. LEED-certified products such as heavy tinted-glass windows used to improve environmental efficiency can also block cellular signals. Bozyk says further challenges result from the fact that many aircraft hangars are located near airports, where there is a lot of RF interference.
“All avionics technicians that work on planes call each other on their cell phones or use their phone or tablet to look up something. They use a lot of cellular,” Bozyk says. “It’s all about accessing their systems, their networks, and sometimes they just need to communicate with another tech for coordination. They need cellular connectivity to do their jobs.”
Connectivity challenges can become expensive quickly in the case of regularly testing GPS and satellite communications (satcom) for safety. When hangar materials block these signals, the aircraft have to be moved outside for testing.
“Major airlines tell us that it costs about $1,400 to move a plane outside their hangar to test their GPS-satcom,” says Dave Schlange, co-founder of KonectaUSA. “Multiply that by hundreds of times a month in larger facilities, and that adds up to a great deal of money.”
To combat these connectivity challenges, KonectaUSA uses distributed antenna systems (DAS) to amplify signals. This typically entails placing one or more antennas outside the hangar—usually on the roof—to capture the outdoor signal from cellular towers and transmit it over cable to amplification units inside the facility. Those amplification units then transmit a stronger signal to antennas placed inside the hangar that rebroadcast it to cellular devices and those using them.
According to Brad Leonard, co-owner of KonectaUSA division KonectaGPS, the company has performed installations of cellular amplification solutions in three facilities for a large international MRO provider that was having issues with cellular coverage.
“They have had hundreds of DAS systems installed in their facilities, from every vendor imaginable and every carrier, but there is no way to inventory or track how they are performing,” Leonard says. “When the carrier changes something on their networks, nobody is notified, and DAS in the hangars stop working, so they end up with cellular reception problems again.”
Leonard notes that the systems KonectaUSA installs in these environments not only provide connectivity for all four major U.S. cellular carriers but also enable remote monitoring so KonectaUSA can keep track of how a system is performing throughout the facility, provide reports and issue software updates remotely.
Through the active DAS hybrid KonectaUSA installed at the aforementioned MRO customer, Leonard says it is able to “provide strong, simultaneous signal amplification across all the carrier networks.” He adds: “We can keep track of all their DAS systems on a single portal and remotely monitor changes in the network so we can make adjustments when needed in response to what is happening in the RF environment.”
KonectaUSA has previously installed cellular amplification systems for aircraft hangars of various sizes, and Bozyk says each project must be customized to accommodate unique design elements and considerations. “We’re mounting these server antennas in the ceiling of the hangar, and there are cranes, air duct handlers, lighting and all kinds of things that could cause interference, so we have to take a lot of this stuff into consideration,” he notes.
Some situations require special considerations, such as hurricane-rated mounts for antennas in regions that experience severe weather. Bozyk says KonectaUSA also needs to work with an MRO’s maintenance schedule so aircraft can be moved out of the hangar to avoid potential damage.
“There’s a ton of coordinating when working in the hangar. Sometimes a plane will be in its slot, and if it’s on jacks, it can’t be moved,” Bozyk says. “We use scissor lifts and boom lifts in the hangar to install the cables and internal antennas. As we don’t want parts to drop onto the plane, we have to coordinate and make sure the plane is out of the slot when we are doing the installation.”
Once the system is installed, KonectaUSA performs testing to make sure the cellular signal is strong and not interfering with GPS and satcom signals. According to Bozyk, the faster the deployment can be done, the better. Hangar installations typically take 2-3 days, with additional time required depending on facility size or other back-office areas also needing connectivity.