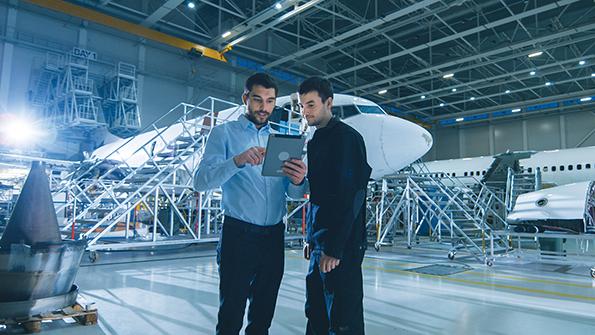
Accenture research found only 8% of aerospace industry executives were highly confident in their mix of supply chain digital talent.
There is no shortage of mixed messages on the state of the commercial aerospace industry.
We are in the best of times with the International Air Transport Association expecting airline revenue passenger kilometers to increase by 98% in 2022. We are in the worst of times with supply chain and workforce challenges affecting deliveries and the bottom line. We have good news from my colleagues at Accenture Research, who found 79% of industry executives expect increased MRO spending in the next 12 months. But we also have bad news from these same executives, who see MRO spending subsequently flattening.
As it navigates these cross-cutting tides, the industry is coalescing around digitalization as a path to efficiency and growth. Increasingly, it seeks “digital precision” through the targeted, value-driven application of data insights and automation to improve aftermarket speed, quality, experience and profitability. Yet digital success, like life, is complicated. Digital technologies can create new aftermarket opportunities but require practical steps in data, digital architectures and talent to realize their promise. The data and industry sentiment tell a similar story. The chances of a digital transformation succeeding remain lower than the chances of winning a coin-flip. Companies that succeed focus on practical, pragmatic paths to a measurable business outcome.
The aftermarket holds digital opportunity—and opportunity to over-promise. The aftermarket has structural, human, operational and data characteristics that may limit this promise. The aerospace digital talent pool has an extremely deep end of engineering, but it rapidly shallows in other areas critical to aftermarket success. In Accenture’s recent Commercial Aerospace Insight Report, we found that while 72% of aerospace industry executives were highly confident in their mix of engineering digital talent, only 8% said the same of their supply chain talent. For aftermarket providers, closing this gap requires going beyond “getting more digital skills” and pivoting to a practical approach that precisely targets skills to areas of industry need.
The aftermarket is at the head of three important digitalization trends. The first is automation. From the use of artificial-intelligence-powered robotic inspection to robotic process automation software that could increase the efficiency of part ordering, automation is an important tool for increasing efficiency and mitigating labor shortages across the aftermarket. In this context, “digital skilling” can be focused on training shop-floor teams on specific digital tooling within the context of their current work. While this population may gradually build a broader depth of digital skills, near-term investment can focus on specific skills that pair with job-specific automation.
The second trend is the market-facing sale and integration of software products. From AnalytX to Skywise, Ascentia, Aviatar and others, analytical products are reshaping the aftermarket as stand-alone offerings and as parts of integrated service offerings. Here, aftermarket providers find themselves at the opposite side of the digital skills spectrum. These new offerings require not only software developers but also experienced designers, product managers, service designers and other staffing that ranges far from the shop floor. OEMs and aftermarket providers have taken multiple approaches to “get more digital talent” in this segment, from building separate dedicated digital organizations to tapping into the engineering workforce and creating digital product teams. The success of any of these approaches remains unclear, as OEMs and aftermarket providers alike seek consistency in retaining and building these kinds of talent.
The third trend centers on the internal use of data science to meet functional business challenges from the overhaul shop to aftermarket finance. These skills blend deep process understanding with facility in analytical tools and data-driven decision-making. Like software development, this is not a natural combination in the average aftermarket organization. Here, “upskilling” efforts can focus on infusing more analytical depth and familiarity with analytical tools and data management into the existing functional base. The Aerospace Industries Association’s recent workforce research supports this approach, with digital, analytics and related skills high priorities for workforce investments.
MROs are invested in the promise of digital tools to use the precision of data, analytics, software and automation to reduce cost, improve service levels and create new growth opportunities. Yet organizations do not instantly acquire digital precision like a martial arts download in The Matrix. Precision requires pragmatism, which starts with people. Moving from a mindset of “getting digital skills” to understanding how automation, software and analytics require different skilling approaches is a first step on the path to achieving digital precision and pragmatic value creation.