IAMA Calls For Changing Future Of Aircraft Modification
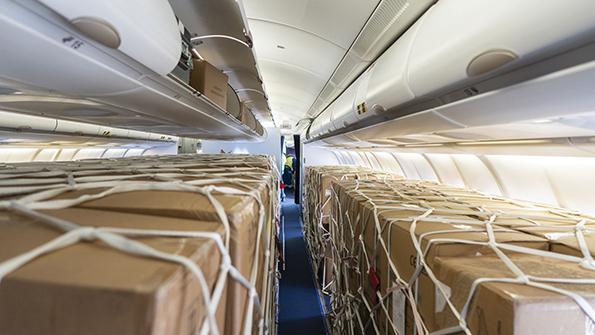
The pandemic crisis has shaken the aviation world as almost no other has. The golden outlook the aviation industry projected at the end of 2019—from airframe manufacturers, suppliers, MRO and modifiers—has since been replaced with the need to navigate very uncertain weather.
However, some things are certain: Changes will have to be made across the travel ecosystem to regain trust, and the industry must be well-prepared for a similar future eventuality.
These changes must be timely. And within each aircraft, every change needs aviation authority approval—which leads us to aircraft modification by supplemental type certificate (STC). Whether we’re talking about touchless cabin solutions, inflight lavatory disinfection, cabin layout adaptations, social-distancing solutions, inflight entertainment and connectivity upgrades or any other optimization—they will all need approval. It is time for the aviation industry to make this process change happen, and I envision this effort leading to a new customer-focused aftermarket ecosystem.
Aircraft modifiers around the world are tasked to design and develop the relevant installation documentation for authority approval. In our new environment, where solutions must be rapidly matured, cost-effective, agile and innovative, the most pressing concern is: What do operators consider important when modifying aircraft? This is particularly relevant when the next step in an aircraft’s life cycle is uncertain, including where the aircraft may—or may not—operate next.
My team at the Independent Aircraft Modifier Alliance interviewed aircraft owner and operator representatives to learn their specific needs around aircraft modification. Our findings reflect the increasing importance of a customer-centric approach. Though aviation authorities worldwide define mandatory requirements for the approval of a modification, standardized requirements throughout the whole value chain are rarely defined.
Owners and operators told us that their highest-ranking needs are effective communication, risk management and reliable after-sale service. In 2019, the International Air Transport Association published its “Best Practices Guide—Cabin Interior Retrofits and Entry-into-Service Program.” It examines the challenges of managing complex multisupplier modification projects from an airline perspective.
Since then, we’ve focused on this major concern regarding proper communication among all integration stakeholders. Modifiers are expected to provide such services in a structured manner, including predictable risk management to ensure on-time, on-budget modification projects—right up to reliable prototype overlays. Particularly during times of rapid innovation, where new materials and techniques often find their way onto aircraft, strong communication among stakeholders and with regulators is paramount, since no certification blueprint for such novel modifications yet exists.
The second-most important need after communication is reliable after-sale service. Although the continued airworthiness instructions provide approved methods to reliably operate a modified aircraft, there are many situations in which modifier support is crucial. These include component improvements, software updates, accidental damage repair or spare-parts availability. Aircraft owners in particular concurred with this requirement. When the modifier is not available to support changes during aircraft lease transfers, owners can face huge challenges. Transfer of usage rights, customized adaptations, modification removal or its validation by another authority are where these challenges arise.
It’s clear that the solution to these demands is to be customer-focused. In uncertain times, an aftermarket offering that provides airlines real choice for the safe integration of innovative products, while maintaining the predictability and reliability of STC projects and after-sale support, would provide a significant upside for operators. Isn’t it time for such new customer-centric, cross-stakeholder cooperation, with rules that ease the difficulties and ensure competition?
Can you envision a new aftermarket ecosystem emerging where the community truly works together to meet customer demands at every level? Where passenger surveys directly feed innovation ideas? Where rapid feedback loops spur incremental improvement within the design process? Where regulators work alongside manufacturers and modifiers to develop worldwide best practices, ensuring the safety and integrity of new methods and products? Where all stakeholders have reliable and secure data interfaces for safe integration? Can you imagine digital collaboration across all stakeholders to optimize the entire modification process—from product definition to approval and after-sale support? I can.
Nicole Noack is managing director of the Independent Aircraft Modifier Alliance.