Clearing SAP From The Runway: The Transition Towards Safer Refuelling

Easy access to international travel is a feature of modern-day life, and the usually vibrant global aviation sector has been deeply affected by the response to the COVID-19 pandemic that has placed restrictions on all but essential travel.
COVID-19 and its economic impact will understandably dominate the agenda for the foreseeable future, but the industry remains focused on the resumption of routine operations and implementing new safety measures.
One of the most pressing areas concerning aviation safety right now is regarding aircraft refuelling systems and the elimination of filters that use superabsorbent polymer (SAP) material.
Identifying the issue with SAP-based filtration
Similar to the absorbent material used in diapers, SAP is in place to prevent water, in the unlikely event that it is present in aviation fuel, from getting into the aircraft. However, it has been shown that when SAP reaches saturation point, it can leak a crystal-like gel into the system, causing problems of its own.
SAP migration has resulted in eight reported incidents, one of the most notable being a 2010 flight by a major airline which lost control of both engines, resulting in a forced landing at twice the normal speed.
The airline approached Shell Aviation as an independent, third party expert to investigate the incident, which concluded that SAP contamination was the cause. While the aircraft ultimately landed safely, this was a call to action for the industry to remove SAP-based filtration.
In 2017, an IATA Special Interest Group determined that SAP-based filters are not suitable for use in aircraft refuelling systems. The Energy Institute (EI) subsequently concluded that they should be phased out by the end of 2020.
Since then, the challenge for industry has been to find a solution that can be certified and retrofitted in time for the 2020 deadline, at a suitable cost point.
Pioneering an industry solution for safer refuelling
Having invested $962m in research and development in 20191 and as one of the few energy companies with a dedicated R&D centre for aviation, Shell has been at the forefront of developing SAP-free alternatives.
"Safety is fundamental to the way Shell operates, at every level of our business, and we are committed to leading the industry's move away from filter monitors that contain SAP and can cause operational issues in aircraft engines", says Thomas de Boer, Head of Operations at Shell Aviation.
Shell teamed with filtration specialists FAUDI Aviation in 2015 to find options to replace SAP. The result is Shell Jet Protection; a 100% SAP-free solution that has been extensively tested by Shell and qualified to EI1598. The technology has also become the first SAP-free system capable of utilising existing filter monitor vessels to be adopted into standards by the Joint Inspection Group, the world-leading organisation for the development of aviation fuel supply standards.2
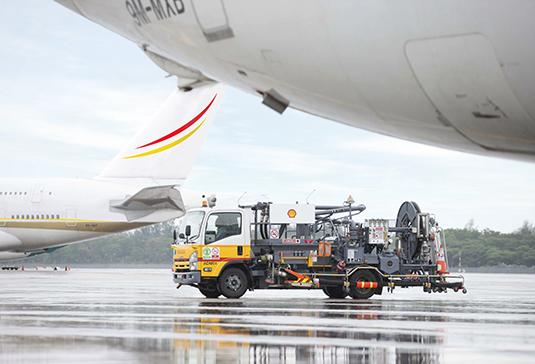
Shell Jet Protection uses a combination of Dirt Defence Filters and a separate AFGUARD® Electronic Water Sensor. The physical SAP-based water filter is replaced with an AFGUARD® electronic sensor that continuously monitors the refuelling, turning off the fuel flow on the rare occasions when water is detected.
"Through Shell Jet Protection, we are able to put a permanent end to concerns about the associated risks of SAP contamination in jet fuel", de Boer says.
The filtration is remarkably fine, de Boer explains, removing particulate down to around 1 micron—with the smallest particles that are visible to the human eye being around 40 microns.
100% SAP-free by the end of 2020
As a result of its forethought, Shell is likely to be the only company able to offer an effective alternative to SAP-based filtration by the December 31 2020 deadline. Shell Jet Protection is set to be operational at all Shell-managed refuelling locations by the end of this year.
Estimated to last some five years—an improvement on the SAP-based filter's annual replacement—the filters can be easily retrofitted at a relatively low cost, which is crucial at a time when the aviation industry is still struggling as a result of the COVID-19 crisis. It also importantly creates less waste.
While the EI recommendation is not mandatory, it is advised that operators and manufacturers implement SAP-free filtration to ensure maximum safety and reduce their liability risk, and de Boer implores the industry to follow suit. Even though we are going through a major crisis because of COVID-19, safety can never be overlooked.
"Shell Aviation urges the industry to prepare for this change, placing safety at the forefront of their operations", concludes de Boer.
1Shell Sustainability Report 2019
2 In August 2020, the Joint Inspection Group (JIG) issued Bulletin 130 which introduces Dirt Defence Filtration (DDF) in conjunction with Electronic Water Sensor (EWS) technology into JIG Standards. Bulletin 130 specifically relates to the FAUDI Aviation DDF and AFGUARD® EWS used in Shell Jet Protection.