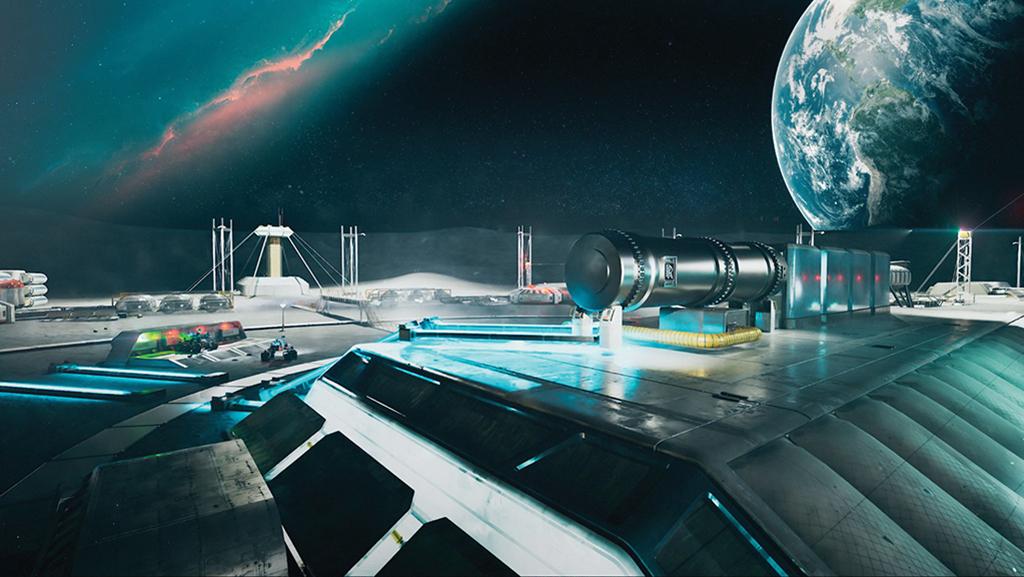
Rolls-Royce is focusing on NASA’s 40-kW surface power requirement for its initial microreactor design to support lunar outposts from 2030 onward.
Credit: Rolls-Royce
As new forms of nuclear energy increasingly feature in future space propulsion and power options, Rolls-Royce is accelerating plans to leverage decades of know-how in the nuclear submarine sector to develop next-generation microreactors for a wide range of space exploration roles. Nuclear power is...
Rolls-Royce Ramps Up Microreactor Work For Lunar Exploration is part of our Aviation Week & Space Technology - Inside MRO and AWIN subscriptions.
Subscribe now to read this content, plus receive full coverage of what's next in technology from the experts trusted by the commercial aircraft MRO community.
Already a subscriber to AWST or an AWIN customer? Log in with your existing email and password.