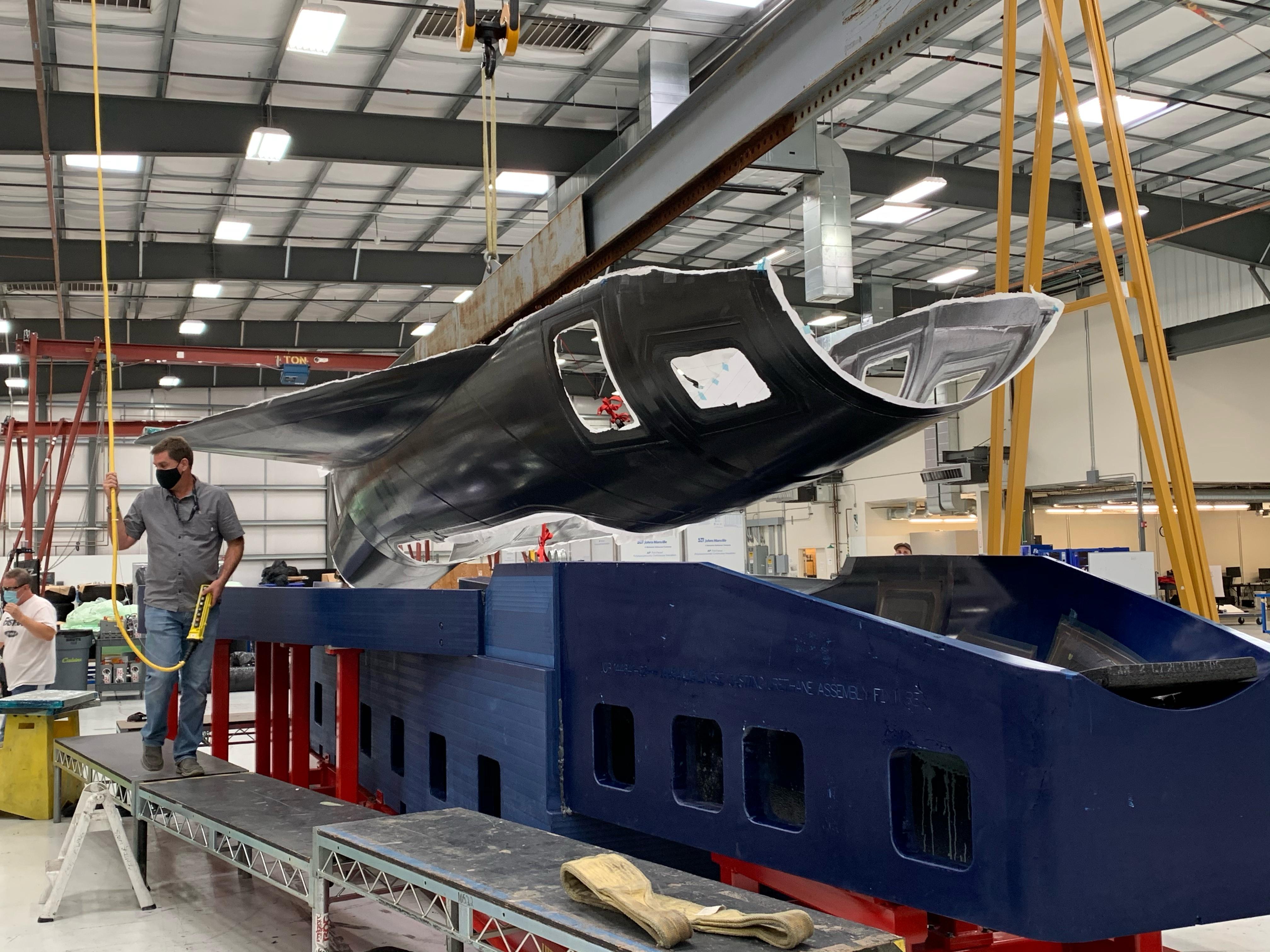
LOS ANGELES—Guidance, navigation and control (GNC) software for Stratolaunch’s Talon-A hypersonic flying testbed has passed a preliminary design review and is being readied by developer Draper for loading next year into the vehicle’s flight control computers.
The Talon-A is a fully reusable, autonomous, liquid rocket-powered vehicle designed to test hypersonic payloads at flight speeds up to Mach 6. Measuring 28 ft. in length with an 11.3-ft.-span delta wing, the Talon A will be capable of recovering for an autonomous horizontal landing as well as taking off horizontally under its own power.
But Stratolaunch, which has begun building the first structural elements of the Talon-A at its facility in Mojave, California, primarily will air-launch the vehicle from beneath its six-engine carrier aircraft—currently being readied at the same site for the resumption of flight tests in early 2021. The twin-boom mother ship is expected to enter operational service as a hypersonic test platform in 2022.
Draper, a not-for-profit research and development company, says development of the Talon-A precision guidance flight control software builds on experience gained over decades of work on spacecraft and hypersonic vehicle programs. Ranging back as far as the production of guidance computers for NASA’s Apollo spacecraft to GNC software for later programs such as Sierra Nevada’s Dream Chaser spaceplane, the company’s work in atmospheric hypersonic flight also has recently broadened with U.S. government flight test and interceptor missile contracts.
“We’ve certainly leveraged what we learned from those programs in terms of how to do really precision GNC on agile, fast vehicles,” says Kimberly Slater, business area lead for Commercial and Civil Space at Draper. Although guidance software for space vehicles is required to handle objects moving at far greater velocities, the complexities of atmospheric hypersonic flight at Mach 5 or above present significant challenges for GNC, she adds.
“Space vehicles go even faster, but they’re in the vacuum of space so they’re missing things like all of the drag and friction from the humidity and gases in the atmosphere. When you think about the flight dynamics of re-entering the atmosphere, you picture the space shuttle or Dream Chaser coming through this fireball during a critical phase of flight. So these hypersonic vehicles in some sense are flying in that massive heat environment,” Slater says.
Having previously used model-based engineering (MBE) methods for refining GNC software for other programs, Draper is applying the same process to the Talon-A. “We’ve been looking at the dynamics of what that [environment] does to the vehicle structure and what it does to controllability. These are interesting questions and really hard problems to solve. So that’s where we leverage everything we know about hypersonics, space, atmospheric conditions and extreme environments. Then we apply the foundational knowledge we have with GNC to build it for these kind of exciting, novel systems,” Slater says.
“The MBE simulation systems are a pivotal part of our design process because we can take away a lot of the risk with the flight element,” Slater says. “We can model systems and simulate them with really fantastic accuracy. We can model what that particular environment will look like and test out the software and iterate on that dozens of times until we think we’ve got the best precision and the best safe approach to that mission. This way, by the time our customers get to one of their prototype missions, they can have a lot of confidence in that first flight.”
The Talon-A work also is an extension to Draper’s growing hypersonics portfolio, which over the past two years has grown to include at least two U.S. military research, test and development efforts. One of these, covering the preliminary design and prototype demonstration of an air-breathing hypersonic interceptor missile, involved working with Virginia-based SPARC Research under a contract awarded in 2018.
Draper also has been working with Sandia National Laboratories, the U.S. Army Combat Capabilities Development Command Aviation & Missile Center and other government labs to develop the GNC system for the U.S. Navy’s hypersonic Flight Experiments FE-1 and FE-2. The tests, conducted in November 2017 and March 2020, evaluated the Block 0 Common Hypersonic Glide Body that will form the basis for the Army’s Long Range Hypersonic Weapon and the Navy’s Intermediate Range Conventional Prompt Strike missiles. Lockheed Martin and Raytheon are now transitioning the rocket-powered glide vehicle to an operational configuration under recently awarded production contracts.
As hypersonic test activity looks to increase for both military and commercial applications, Draper expects to continue its partnership with Stratolaunch on additional vehicles. “They see us as their GNC partner,” Slater says. “We’ve done some advising for them on other projects, but right now our big task with them is GNC for Talon-A. But the expectation with them is that we would support their vehicle as it evolves and certainly the next evolution of Talon-A once they get past the test prototype.”
Beyond Talon-A, Stratolaunch plans to develop the Talon Z, which will target faster test conditions up to Mach 10. Weighing up to 65,000 lb., the larger vehicle will offer longer-duration flights that could potentially see the vehicle boost to 500,000 ft. altitude and cover ranges up to about 800 nm. Like Talon-A, Talon-Z is being designed to enable external payloads, including bolt-on propulsion or flow-path experiments, as well as fin-like structures for boundary layer transition and other investigations.
Beyond the Talon testbeds, Stratolaunch ultimately hopes to develop the Black Ice spaceplane, a small, space shuttle-type vehicle that could provide an air-launched reusable transport capability to orbit.