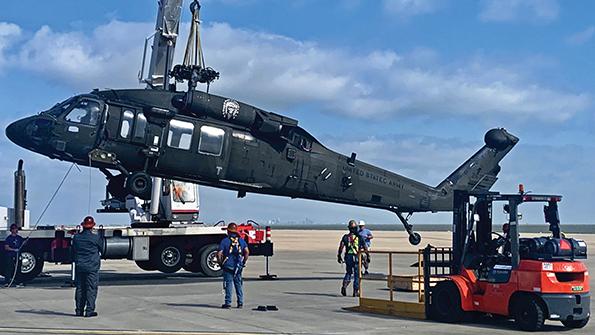
The U.S. Army is embarking on an initiative that may revolutionize the maintenance process for current and future aviation systems. The service is partnering with the Wichita State University National Institute for Aviation Research to create a Sikorsky UH-60L digital twin.
The idea is to convert all the 2D UH-60L specifications into 3D parametric models. Researchers completely disassembled one UH-60L to create a virtual model. The L model UH-60 has not been in production for the last 15 years, meaning some of the parts are expensive to purchase or obsolete.
- Service begins receiving UH-60L digital-twin files
- Building on commercial aviation experience, the Army looks for best ways to use advanced manufacturing
Once there is a digital twin, the Army will have 3D computer-aided design files that can be fed into a computer numerically controlled (CNC) machine to produce spare parts. Many industries have also incorporated digital-twin technology to predict equipment performance.
“This will allow the Army to source parts that are out of production as well as use advanced techniques such as additive manufacturing to produce parts,” says John Tomblin, senior vice president for industry and defense programs at Wichita State and executive director of the National Institute for Aviation Research.
The Army has received the first 3D-model files for the UH-60L digital twin, which include over 200 models of parts that constitute the horizontal stabilator. The remaining model files for structural components will be scanned and delivered by December 2022, according to Joyce Myers, U.S. Army Aviation and Missile Command (AMCOM) chief data and analytics officer.
The goal is to develop a prototype that will eventually transition to existing platforms and inform digital engineering requirements for future equipment. While this is a significant first step, the Army cautions that the new digital twin is representative of a single aircraft, not the entire fleet.
This new way of thinking about aviation sustainment may change how the Army buys aircraft. The Army could potentially acquire the intellectual property rights for digital twins of the Future Attack Reconnaissance Aircraft and Future Long-Range Assault Aircraft. If this is what it decides to do for future and legacy programs, the digital twins could help the service provide specifications to vendors for individual parts that have been obsolete—potentially reducing the cost of retrofitting older-model aircraft.
Another AMCOM priority is to make the maintenance process easier for soldiers on the battlefield. Imagine flying a U.S. Army UH-60L over South Korea when a bird strikes the rotor blade, causing it to break. Instead of waiting for a replacement to eventually make its way through a lengthy logistics process, the Army hopes the pilot can instead ask another soldier in the unit to manufacture a new rotor blade on the spot.
The Army is not there yet technologically, but advanced-manufacturing breakthroughs may help reach that goal. A key AMCOM initiative is to continue updating the Army’s advanced-manufacturing policy for aircraft parts, components and support products.
The service issued the initial advanced-manufacturing policy for Army aviation last May and immediately began working on an update, AMCOM commander Maj. Gen. Todd Royar tells Aviation Week. The initial policy prevented aviation units from implementing advanced-manufacturing practices without AMCOM’s direction. Instead, the soldier would pitch the idea to a liaison engineer who would check if the idea was sound.
The second iteration of the policy document, signed in April, further defines testing and evaluation standards. AMCOM worked closely with major airframe and engine OEMs to inform the Army’s advanced-manufacturing process and take advantage of the commercial sector’s experience with the technology.
Royar says it is too early to estimate the cost savings from advanced manufacturing, but this is not stopping the service from coming up with ideas on how to best implement the technology, including the UH-60L digital twin.
As the service explores the potential of advanced manufacturing to maintain and sustain its aircraft fleet, the new policy aims to strike a balance between escalating costs, readiness improvements and safety.
“Our policy provides a deliberate approach to ensure airworthiness and safety while determining where research and efforts may best supplement the supply chain and improve performance while balancing cost,” Royar says.
Comments
It does already work for non-critical parts like fairings or simple things like brackets. But producing aerospace-grade, safety-critical components like a rotor-blade requires more than 3D shapes and a 3D printer. It requires qualified people working in a certified production organization in a certified production environment, with monitored quality assurance processes.