
The radome on this Fokker F100 suffered significant damage, losing its structural integrity.
Aircraft radomes are precisely constructed to optimize radar system performance while protecting against environmental hazards. The slightest change in their physical characteristic such as excessive layers of paint can adversely affect radar system performance.
A radome is similar to your nose. It sits in front of our face, and when it gets “punched” it is going to hurt. Given their position at the very front of the aircraft, radomes are vulnerable to hail damage, bird strikes, lightning and static discharge. It is lamentable that this important aircraft structure, which protects important components of our aircraft, receives so little discussion in pilot training manuals for proper pre- and post-flight inspections. It is not uncommon for training manuals to simply state, “Radome: check for condition.”
Damage to a radome may induce a cacophony of seemingly unrelated failures that can cause excessive pilot workload. On July 1, 2010, a Swiss International Air Lines Fokker F100, registration D-AGPH, took off from Warsaw enroute to Zürich. During the climb through 7,135 ft. AGL, the crew heard an impact sound from the nose bottom of the fuselage. The crew interpreted this sound as a probable bird strike. Moments later the captain’s airspeed indicator began to fluctuate +/- 20 kts. The master caution light illuminated along with its warning sound. The MFD also displayed the airspeed comparator, no Autoland and rudder limiter alerts.
The flight crew abandoned the climb and reduced the airspeed to 200 kts to avoid causing additional damage to the aircraft. The first officer continued as the pilot flying because the instrument indications on his panel were compatible with the standby instruments. Thereupon the flight crew checked operation of the cabin pressurization system and decided to return to Warsaw. They informed the controllers of the malfunctions of some aircraft systems likely caused by a bird strike, then performed the checklists for the abnormalities contained in the Quick Reference Handbook.
The landing approach to Runway 33 was performed with the autopilot and autothrottles engaged. The power levers were moving into the forward and aft position despite slight speed fluctuations on the other instruments. During final approach, the windshear alert triggered at 120 ft. The flight crew performed a go-around; when reaching 3,000 ft., the pilot flying needed to disengage the authothrottle due to pronounced malfunctions that would not maintain the required airspeed.
A duty officer who was close to the threshold of Runway 33 informed the controller that he observed damage to radome, information that was then communicated to the flight crew. The flight crew concluded that the windshear warning was caused by disturbed airflow around the pitot tube which was also causing the airspeed fluctuations on the captain’s airspeed indicator, likely related to the damaged radome. The flight crew decided to ignore the next possible windshear warning and performed the second approach with the autothrottle disengaged. The aircraft landed without further damage.
Water Ingress Of Radome Structure
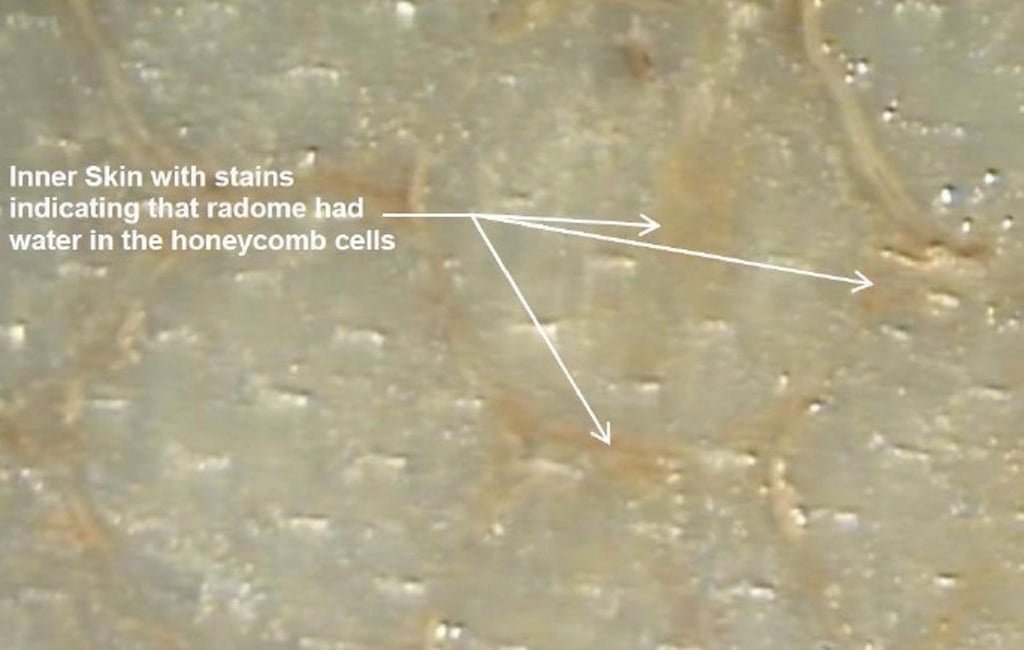
Subsequent investigation by Poland’s State Commission on Aircraft Accident Investigation discovered significant delamination to interior components of the radome caused by conditions that allowed water ingress into the interior plies of the composite structure. The entrapped moisture experienced multiple freeze-thaw cycles that degraded the bonding between the fiberglass epoxy composite structures.
Investigators noted that the radome had experienced previous bird strikes which created localized microcracks in the laminate structures. Microcracks would allow moisture ingression into the internal laminate structures, especially the honeycomb core. An area which appeared to still be bonded after the incident was removed for analysis. When the inner skin was removed, water poured out of the honeycomb cells. The inner skin exhibited residue that was left behind from trapped moisture.
After a bird strike the airplane maintenance manual (AAM) requires an inspection of the internal and external surfaces of the radome for cracks, delamination and indications of core damage. The investigation report noted that the AMM manual does not require the use of a moisture meter to inspect the interior components after a birdstrike. As a result, the repair of the radome after several bird strike did not reveal weakening in the composite construction.
Composite Construction
A radome must endure a spectrum of challenging environmental conditions. It must protect the vital components in the nose of the aircraft in extreme temperatures, at speeds approaching 500 kts, while enduring the punishing hits from rain, hail and lightning, not to mention bird strikes.
Radomes are typically manufactured from a combination of composite materials. For instance, the radome on the F100 utilizes a core of honeycomb sandwiched between protective layers of fiberglass. A bonding resin is used for adhesion between the components. The exterior surface is treated with specialized paints to minimize rain erosion and static build up.
In Part 2, we discuss damage caused to aircraft radomes by water entry and static discharges.