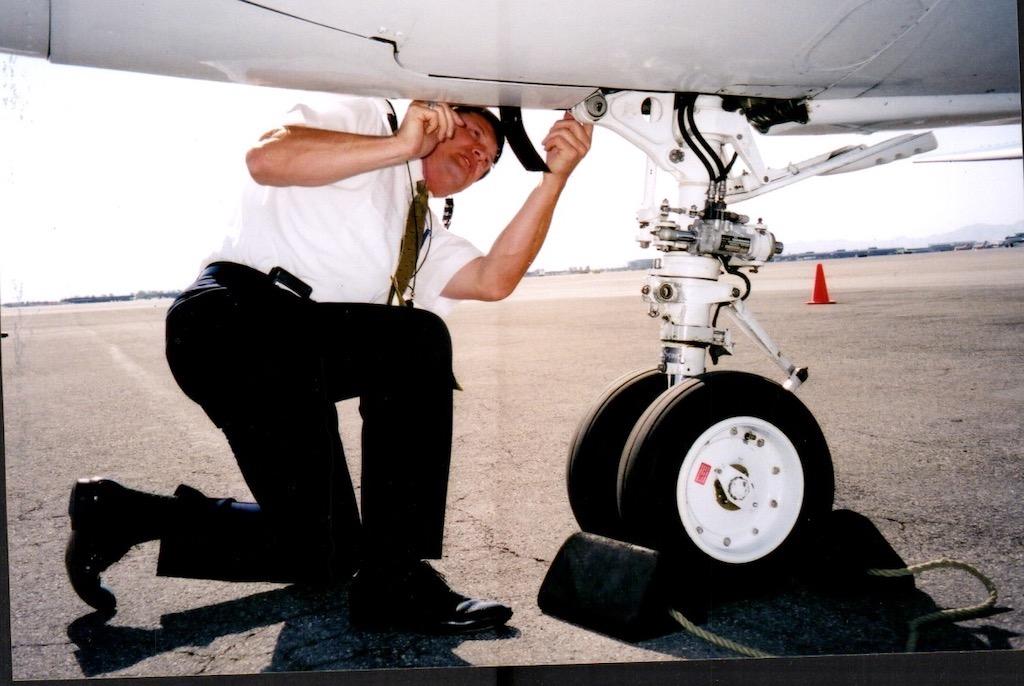
Pilots should coordinate closely with maintenance technicians to detect and correct time-limited components such as brake pads and tires nearing their limits at the home base versus at a distant airport.
When freezing precipitation has happened overnight, carefully check an aircraft’s engine inlets if you do not utilize engine inlet covers.
As pilots, we have been instructed to verify that the engine cowl and inlet are clear of ice and snow and that the fan rotates freely during our walkarounds. This is not easy on many business jets, particularly in the case of high-mounted engines. It is possible for precipitation to pool on the bottom of the engine inlet and freeze the engine fan. It only takes a small amount of frozen liquid at the bottom of the inlet to prevent rotation of the engine fan blades.
Unfortunately, a frozen fan can result in expensive engine damage if an engine start is attempted. During the start sequence, the N-2 (i.e. “high-pressure”) shaft is free to turn, but the fan will not. If fuel is introduced to the engine during the start sequence without enough air flowing through the engine, temperatures in the combustion section will quickly soar, resulting in damage to the hot section of the engine and the necessity for subsequent maintenance action.
The duration of the over-temp as well as the over-limit temperatures are important to note, since those will dictate the post-incident inspections and actions that must be done by maintenance technicians.
Attentively monitoring the engine start process is equally important to prevent this from happening. “Catching” the lack of fan rotation early in the start sequence before the introduction of fuel and aborting the start before engine temperatures begin to rise will minimize the damage.
If the aircraft has been cold-soaked, the battery may need to be warmed to a minimum specified temperature prior to start. If you know the aircraft is going to be cold-soaked, remove the battery and store it in a warm place.
The flight deck avionics may need to be warmed. The warm-up may take up to 30 min. The auxiliary power unit (APU) will accomplish this task more rapidly than the engines on the ground. If the APU is inoperative, the engines will need to be at a mid-range N-2 value in order to provide enough hot air through the bleed air system. You must ensure that the instruments are operating properly.
Beware of Frozen Liquids
If your aircraft will remain overnight with air temperatures that drop considerably below freezing, it is important to remove liquids from the aircraft that could freeze, burst their containers and then, upon thawing, allow liquids to escape into various parts of the aircraft that are not protected against a variety of failure modes. This especially pertains to the water lines in the lavatory. If the pipes break, the water will seep into the underbelly of the aircraft.
Why should we worry about some water in the underbelly? On May 9, 2007, a Dassault Falcon 20 was descending toward London Stansted Airport after a flight from Gander, Canada, when a lateral flight control restriction became apparent. The captain applied corrective trim, but the warning indication reappeared.
During descent, the latter flight control problem had become worse. While in a left turn, the bank angle continued to increase, and when it reached 45 deg., the captain disconnected the autopilot with the intention of flying manually.
The captain found that roll control was excessively stiff when rolling to the right. Full force by the pilots was applied to both control wheels in an attempt to recover lateral control, but no movement was possible. The captain was only able to make turns through the gentle use of rudder. He accordingly restricted the bank angle to a maximum of 10 deg.
The flight crew notified air traffic control that they had a jammed flight control and were only able to make shallow left turns. Thanks in part to extraordinary airmanship, the aircraft landed safely at the airport, and all seven occupants exited without injury.
During the investigation, a significant volume of water (at least 20 liters, or 4 gal.) was discovered below the floor panels in the forward fuselage. The water had frozen in flight and caused a restriction to the movement of the aileron trim actuator.
UK Air Accidents Investigation Branch Bulletin 2/2008 said the water in aircraft bilges could have come from a variety of sources, to include leaking plumbing, condensation and leaking seals. It seems likely that the water must have built up in the fuselage over time.
Dassault believed that a more likely source of the water in question was minor leaks in the area of the icebox drain over an extended period of time. The manufacturer had received notification of three previous events similar in nature to that experienced by the Falcon 20 flight crew.
To prevent this problem from reoccurring, operators were reminded that drains must be checked during the aircraft daily inspection, as well as checking both manual and automatic drains.
Check Mechanical Items
Obtaining non-scheduled maintenance at an outstation can unexpectedly ground an aircraft and restrict its availability. This can be caused by a myriad of issues, including worn components such as brake wear indicators or tires. Depending on the complexity of the corrective maintenance, the local fixed-base operator (FBO) may not have the personnel, equipment, training or authorization to perform the required actions.
Even something as simple as having the correct jack pads for your aircraft can add additional waiting time. You are now dependent on the host FBO for use of its facilities while you do the brake change (if the FBO allows that). There will be the added costs of transporting your maintenance technicians along with the required parts to the outstation location. In the interim, it may be necessary to purchase additional airlift at the last minute for your boss, and this is likely to be expensive. The extra costs can quickly build up.
A wise maintenance supervisor will have a proactive system of checks to catch any of these “wear and tear” items so they can be replaced prior to dispatch, rather than having them reach their replacement condition while on the road. This is especially important if the aircraft is being dispatched to smaller airports with limited maintenance facilities.
The sage expression “Prior Planning Prevents Poor Performance” needs to be a core value in a flight department, we recommend in Part 3 of this article.
To read Factors That Affect Aircraft Availability, Part 1, click here.