Monthly Program Profile: Cessna Denali
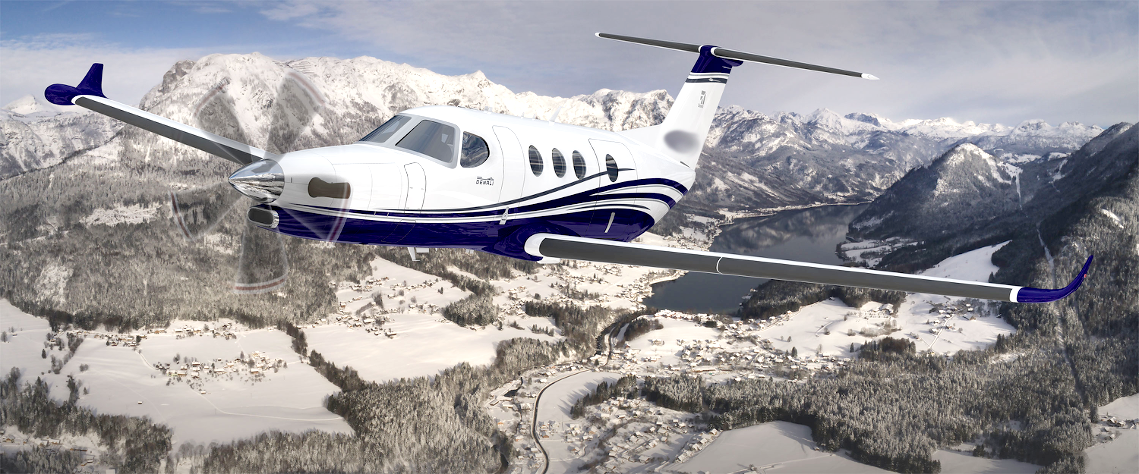
The Cessna Denali is a single-engine turboprop airplane being developed by Wichita, Kansas-based Textron Aviation. Unveiled in July 2016, the clean-sheet airframe will be powered by GE Aviation’s in-development Catalyst turboprop engine.
According to Textron, the maximum passenger capacity of the Denali will be between 8 and 11 passengers. Those passengers will be accommodated in a flat-floor cabin that is promoted as being the tallest and widest in its class, and which has a length of 16 ft. 9 in., width of 5 ft. 3 in. and height of 4 ft. 10 in. Additionally, the airframe’s cargo door has a height of 4 ft. 3 in. and width of 4 ft. 2 in., with additional storage space for baggage located in the nose. Other features of the Denali’s cabin include an in-flight-accessible baggage compartment and a refreshment center located in the forward portion of the cabin, as well as an optional belted and externally serviceable lavatory.
Textron currently markets two configurations for the Denali, an executive layout that has six seats in the cabin, as well as a high-density configuration that increases the number of cabin seats to nine. Another characteristic of the Denali’s cabin is its 6,130-ft. cabin altitude at 31,000 ft., a figure that is also promoted as being class leading.
The pilot(s) will operate the Denali using Garmin’s G3000 avionics suite that includes three 14-in. diagonal, wide-screen liquid crystal displays (LCD) and a pair of touchscreen control panels.
Other standard avionics features include dual air data computers, attitude heading reference systems, Garmin flight management systems (FMS) and transponders.
Those transponders have automatic dependent surveillance—broadcast (ADS-B) In and Out capabilities, while the FMS utilizes “dual WAAS [wide area augmentation system]-enabled GPS receivers for navigation.” Also standard is a digital audio system, synthetic vision technology, terrain awareness and warning system (TAWS), traffic alert and collision avoidance system (TCAS I) and weather-avoidance radar, while an optional feature of the Denali’s solid-state weather radar is “turbulence detection and volumetric scanning.”
Mission and Performance
Based on single-pilot operations and while carrying four passengers at the airframe’s high-speed cruise speed, the Denali is projected to have a range of 1,600 nm. Other performance figures that have been released by Textron include a maximum cruise altitude and speed of 31,000 ft. and 285 kt. true airspeed (KTAS), respectively.
Variants
When carrying its full-fuel capacity, the Denali is expected to be able to carry a payload of 1,100 lb., while the trailing-link landing gear and size of its tires enable operations from runways that are unimproved.
According to Textron, the clean-sheet Catalyst engine has a power rating of 1,300 shp and time between overhaul (TBO) of 4,000 hr. With regard to Catalyst’s components, it is promoted as being the first turboprop engine to utilize 3D-printed parts, a manufacturing approach that reduces part count, weight and, consequently, fuel burn.
Specific engine components include a four-stage, axial single centrifugal compressor that has a pressure ratio of 16:1, with that ratio marketed as being higher than competing engines and lowering the engine’s specific fuel consumption.
Beyond the compressor, another part of the Catalyst engine that is described as being compact is the reverse-flow combustor. That component, along with the engine’s “advanced fuel nozzles,” make combustion more efficient, with the amount of emissions and soot produced being substantially reduced in comparison to other in-class engines. The Catalyst powers a five-blade, composite, digitally controlled McCauley Blackmac Carbon propeller that has ice protection and is capable of being put into a reversible pitch position.
Controlling the Catalyst is a dual-channel, full authority digital engine and propeller control system, with the pilot’s controls reduced to a single power lever that incorporates detents. That single lever is part of the engine’s integrated propulsion control system, which is described as automatically optimizing a number of engine parameters, including the bleed valves, fuel flow, propeller pitch and speed and variable stators.