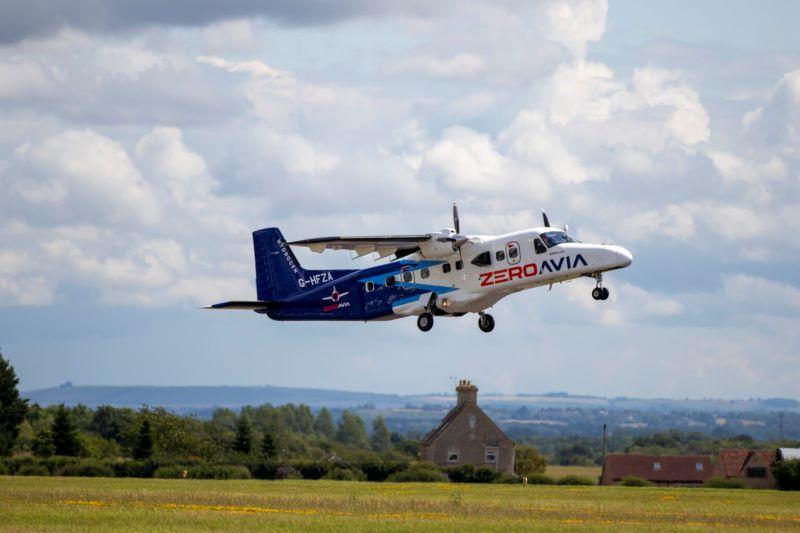
Credit: ZeroAvia
Zero-emission propulsion pioneer ZeroAvia has completed the initial flight-test campaign with a Dornier 228 fitted with a prototype of its ZA600 hydrogen-electric powertrain. The company will now finalize the design for certification of the powertrain and its installation on the initial application...
Subscription Required
This content requires a subscription to one of the Aviation Week Intelligence Network (AWIN) bundles.
Schedule a demo today to find out how you can access this content and similar content related to your area of the global aviation industry.
Already an AWIN subscriber? Login
Did you know? Aviation Week has won top honors multiple times in the Jesse H. Neal National Business Journalism Awards, the business-to-business media equivalent of the Pulitzer Prizes.