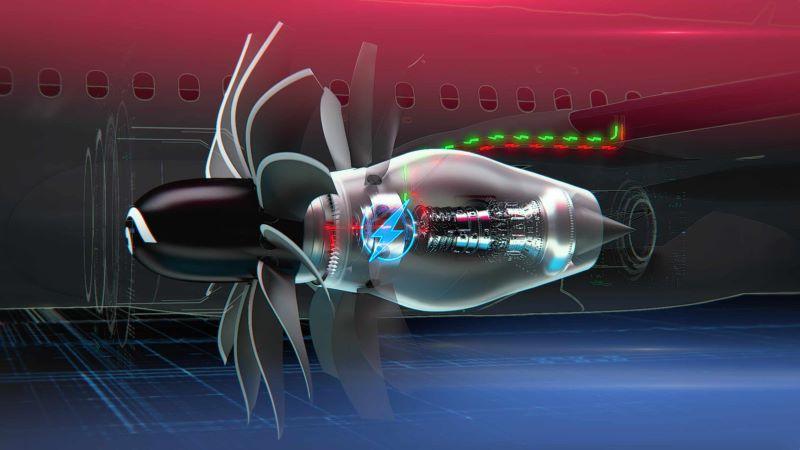
Credit: GE Aerospace
GE Aerospace has won a Phase 2 contract under NASA’s Hybrid Thermally Efficient Core (HyTEC) program which will contribute to next-generation single aisle engine technology in development for GE/Safran joint venture CFM International’s RISE (Revolutionary Innovation for Sustainable Engines)...
Subscription Required
NASA GE Compact Core Contract Paves Way For RISE Engine is published in Aerospace Daily & Defense Report, an Aviation Week Intelligence Network (AWIN) Market Briefing and is included with your AWIN membership.
Already a member of AWIN or subscribe to Aerospace Daily & Defense Report through your company? Login with your existing email and password.
Not a member? Learn how you can access the market intelligence and data you need to stay abreast of what's happening in the aerospace and defense community.