Integrated Program Planning And Execution
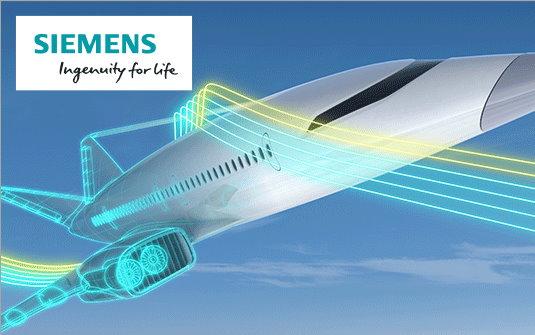
Enhancing the bid process and program management
Today's aerospace and defense companies want to improve their program planning and execution so they can provide accurate and complete bids that enable them to reduce bid and proposal expenses and control program costs and schedules. Improving program performance directly impacts the probability of winning new business, and embracing program discipline results in fewer unexpected increases in program costs during execution.
Although the importance of an accurate bid during the proposal phase and control of program costs and schedules during execution has been well recognized for decades, most aerospace and defense organizations rely on disconnected software tools to plan and manage programs. Most enterprises commonly rely on Word documents, Excel spreadsheet software and various scheduling tools. As a result, gaining a clear view of what is happening within a program is nearly impossible, and that is a major factor in a high percentage of program failures.
Siemens Digital Industries Software provides a systems approach to program planning and execution by integrating cost, schedule and technical requirements in a fully planned, resourced and budgeted program management solution. Thus, it increases the probability of executing programs that adhere to cost and schedule requirements by maximizing the re-use of bid and program artifacts. It provides an integrated system to manage all program artifacts, including cost, schedule and technical requirements, and provides complete traceability to all such artifacts as shown in figure 1. Now, due to the complete traceability of program artifacts, the impact of a change can be easily evaluated, and appropriate action can be performed in a rapid and accurate manner. Since all artifacts are under configuration management, a complete history is maintained, enabling a historical review of approved changes to the program artifacts.
Providing a standard bid library
Maintaining historical program data based on best practices and lessons learned can help companies quickly fulfill a specific bid for a request for proposal (RFP) or internal project. Therefore, we enable users to create a standard bid library that has information on a number of company-defined filters. For example, one filter could be platform type, such as single aisle, twin aisle; another filter could be the certifying country or union like the United States, Canada, the European Union (EU) and China, and yet another filter could be airlines such as United, Delta, American and Southwest. Filters can be based on any factor that impacts any of the artifacts that make up the bid, such as scope of work, requirements, processes, risks/opportunities, deliverables, engineering bill-of-materials (eBOM) and logical or functional architectures. In this manner, we can configure a new program based on the filters that maximize the commonality across bids and recognize that many factors impact a bid. Figure 2 illustrates the standard library, the use of filters to create a program, and the ability to compare it to the customer's request. By bidding and performing work in a consistent manner, customers will realize improved program execution while ensuring that program requirements are being met.
Generating complete program-specific plans
To organize all the data that impacts a bid and subsequent program execution, Siemens uses the work break-down structure (WBS), which is a hierarchical and incremental decomposition of a project into phases, deliverables and work packages. Since the WBS is hierarchical, it provides clear structural organization of all program management artifacts. The lowest level of the WBS, the work element, is the level at which work tasks are scheduled and managed. The work element is home to all work packages and is the level at which all the information resides that is required to define, budget and determine the start and end date of the work. Figure 3 shows how all information is related directly or indirectly to the work element.
Integrated program planning and execution (IPP&E) provides the ability to generate a complete program-specific plan (technical requirements, work breakdown structure, risk/opportunity, cost estimate, integrated master plan and policy/procedures defining standard work, planning eBOM, logical structure, etc.) from a library based on program experience.
Important elements in IPP&E include identifying, reviewing, positioning and incorporating risk and opportunity into the program plan. IPP&E enables you to use a standard risk and opportunity library to capture company experience, and add, delete or revise those risks and opportunities for a specific program while providing a complete history of all changes.
To implement IPP&E, Siemens has developed a detailed business process map. The process map enables customers to start with a well-defined process, which can be modified as needed to best support their process. This process map promotes better execution and spending less time on developing process breakdowns and allows Siemens to provide a consistent level of service delivery. Figure 4 illustrates a high-level summary of the complete IPP&E business process. This shows the ability to manage a standard bid library as well as generate a specific program bid from the standard library. You can also add bid items that are unique to the program or that were not already in the standard library. Calculating the bid cost and management of earned value is supported through integration with third-party pricing and earned value management system (EVMS) software. No matter how good a plan is, issues will arise during execution that require rework or additional tasks as part of a recovery plan. All of these updates can easily be incorporated while maintaining the complete history of the changes.
Implementation
Siemens provides a complete implementation catalyst to help you accelerate your return-on-investment (ROI) and achieve program execution excellence. It provides documentation of the detailed business process, step-by-step implementation instructions and Teamcenter® software configuration data. A sample data set is provided as well as a detailed script to execute the business process, enabling customers to set up an environment in which their employees can conduct hands-on process walkthroughs.
Conclusion
Siemens' IPP&E solution provides closed-loop integrated program management, bid management and a risk management system that is tightly woven into a core product lifecycle management (PLM) function. Ultimately, the IPP&E provides terrific time-to-value for your program management investment.