Digital Engineering for Space
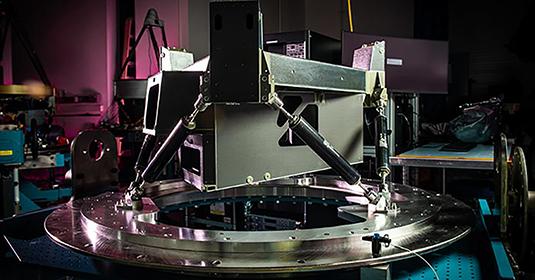
How digital twins of future physical systems speed development
They call it digital engineering, and it’s part of the Department of Defense’s strategy for agile production of the technologies needed to stay ready for anything.
The approach takes every part of a system’s lifecycle – design, testing, manufacturing and operations – and renders each, in digital detail, in a virtual environment. Using realistic modeling and simulation, digital engineering saves time and money by exposing potential problems and identifying opportunities to optimize long before real-world production begins.
“In today’s rapid-development environment, we’re using keyboard strokes and digital media to design and build digital twins of future physical products,” said Matt Magaña, vice president, Space Systems for Raytheon Intelligence & Space, a Raytheon Technologies business. “This influences everything from our systems engineering processes, what and how we buy from the supply base, the way we test systems, the way we manage our programs, to how to build the right manufacturing environment and when to test payloads – all for maximum efficiency.”
Digital engineering was at the center of WorldView Legion, a system of Earth-observing satellites that Raytheon Intelligence & Space helped create for Maxar Technologies. The Space Systems team developed a new digital approach to deliver upon a production schedule of one payload – that’s one instrument – every month.
Maxar’s WorldView Legion’s satellites will offer accurate and timely data about the Earth using high-resolution imagery and a high “revisit rate,” or the number of times per day a satellite images a specific location. With digital engineering, the team was working with production in mind, even in the earliest stages of design.
“From the beginning, we digitally designed a lab with a focus on production,” said Madison Dye, WorldView Legion systems engineer for Space & C2 Systems at RI&S. “Rather than manufacturing when required, we treated it like a production line, all in one room. We were able to build all of our hardware before we even finished testing one full flight.”
Digital engineering also does away with the two-dimensional documents that engineers and technicians have historically used. Instead, they work from realistic and interactive 3-D models – including one that simulated the production and buildup of the satellite, right down to the flow of hardware through the factory.
That essentially gave the team a risk-free run-through of production – and an opportunity to learn from it and adapt.
“We’re employing digital engineering in the spirit of ‘fail fast, learn fast,’” said Magaña. “It has the ability to significantly reduce the occurrence of those unknown unknowns. And, by learning everything before the hardware is built, we are able to deliver on the commitments we make to our customers.”
Raytheon Technologies develops space technologies that are used for purposes as diverse as missile warning and defense, intelligence, weather and climate monitoring, Earth observation, human space flight, and beyond. What we do in and for space is essential for global commerce, scientific discovery and national security. Learn more.