Ask the Experts: A Balanced Model for Digital Transformation
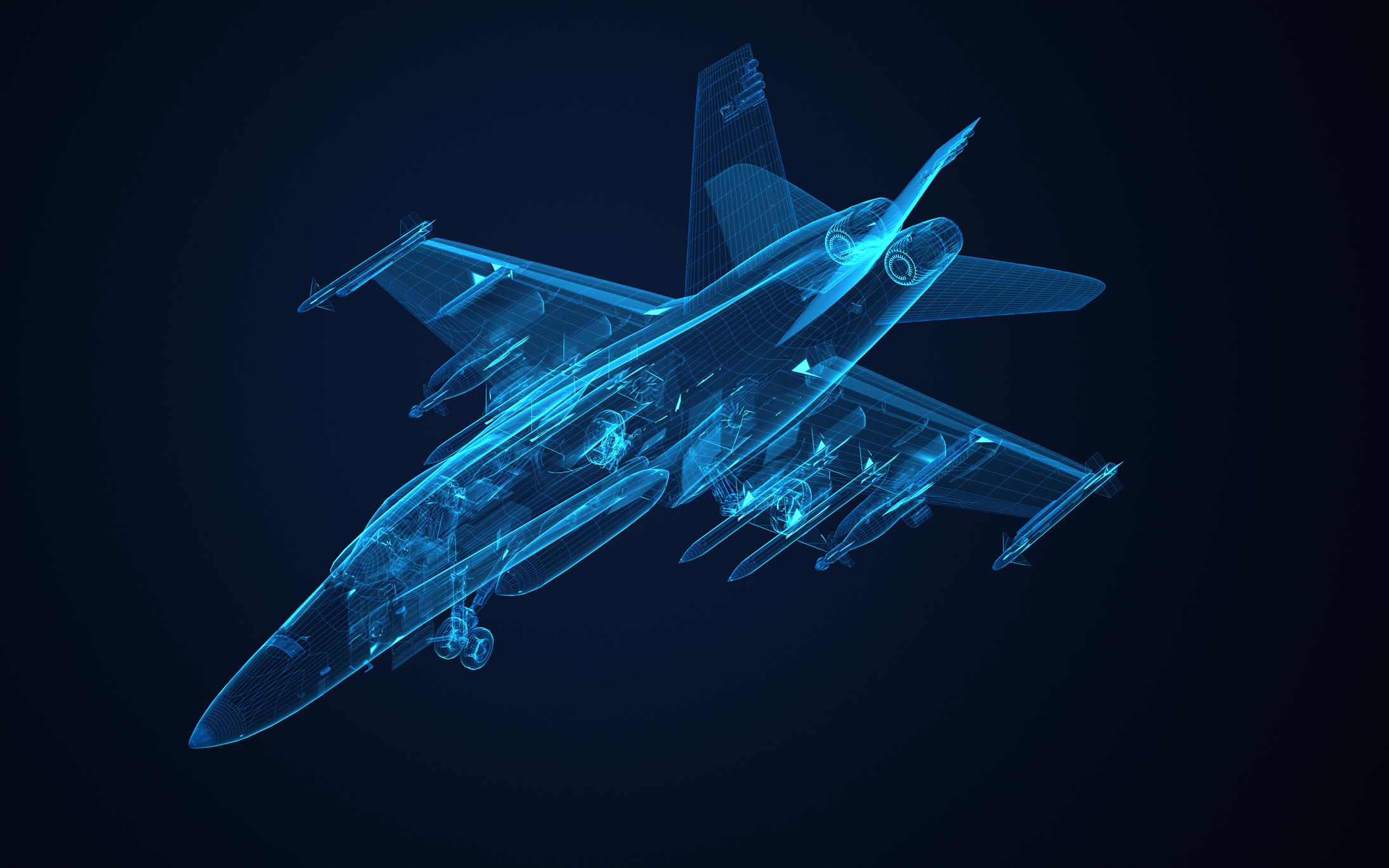
A look at a new approach to modeling that extends the benefits of virtualization to the entire value chain.
Most aerospace companies already leverage 3D modeling, analysis and simulation in design and manufacturing to lower cost, increase quality and reduce time to market. But virtualization has potential beyond the product level. Manufacturers already use tools such as ERP, to create a holistic view of the entire value chain. Synchronizing product modeling with enterprise models of planning, logistics, finances and the supply chain is what HCL Technologies calls the Model Based Enterprise 2.0 (MBE 2.0). Aviation Week spoke with Matthew Cordner, Principal Aerospace & Defense Business Architect, at HCL to discuss MBE 2.0 and other industry trends.
AW: How would you characterize the aerospace industry's maturity compared to other manufacturing sectors when it comes to the digital transformation?
Cordner: When it comes to product capability, testing and monitoring, the aerospace industry has been on the forefront of digital transformation for decades. But because aerospace is such a low-volume industry with long product lifecycles, often 30 to 40 years, the transference of those capabilities into manufacturing, supply chain and financial processes has been much lower than many other sectors, such as high tech and automotive. Aerospace has perfected the art of managing outcomes instead of inputs. Digital transformation requires accurate process inputs, high levels of standardization and synchronized processes. These are not traditional areas of high priority in aerospace.
AW: So how does virtualization fit into the picture of managing all of those variables you mentioned? I typically think of virtualization as a function of product design.
Cordner: There's been a focus for almost three decades now on using digital representations of products and the associated technical data, 3D modeling—the bills of material, and specifications within the engineering organization—to define the product and to do simulations and analysis.
But now we’re seeing virtualization being applied to financial, supply chain and factory modeling.
They’re defining those processes digitally and using the models to simulate actual scenarios. This helps manufacturers make decisions around finance planning and execution and supply chain and material planning. I believe, from a financial perspective, the biggest digital transformation gains over the next five to 10 years in aerospace and defense are going to come from the virtualization of these models of business processes that form this value chain from product design to building, supporting and maintaining the product.
It’s the thread of information that you use to gather information about what customers are going to order, so you can have more accurate demand forecasting. It’s the digital thread on the shop floor that helps you gather feedback of what's performing well, what's not performing well at a machine level and use this information to make real-time adjustments to keep production flowing and take corrective actions for the future.
AW: Can you tell me about HCL’s MBE 2.0 and how that helps bring this digital thread together?
Cordner: As companies look for a competitive advantage in the marketplace, what we find is the advantage often doesn't come from the performance of the product itself. The competitive differentiation comes from the ability to monitor enormous amounts of information inside and outside your company, find insight in it, create plans that address those insights, and rapidly deploy them to the supply chain. This has to be done across the entire value chain, not just engineering, but also manufacturing and the support organizations. The ability to have that insight and agility using digital technologies and data is what we at HCL call Model Based Enterprise 2.0. It helps people to expand beyond the product definition to an enterprise view that uses digital tools to define and optimize the digital threads in each of their functional areas.
For example, in a traditional model, product engineers would throw their design over the fence to manufacturing engineers, who would then have to figure out how to build it. Once they have defined that process, they take those work instructions or process instructions, and they throw it over the wall to operations, who takes those instructions and start building the product. The problem is that if any issues arise related to the design or process, the respective team needs to send all that information back upstream to correct the problem. With a more unified process across the design of the product, the design of the process and the building of the product, we can have that agility that we look for in a resilient supply chain. 3D modeling of products has significantly improved this process from an engineering change management perspective, now it’s time to apply these principles to the management of supply and demand as the product is being produced.
AW: We’re hearing more about supply chain issues these days, whether they’re related to the pandemic or other unplanned events. Could this model help aerospace manufacturers gain better visibility of the current state of their supply chain and enhance predictability?
Cordner: This is certainly a hot topic now. There are many factors that can disrupt a supply chain. And, of course, our supply chain is critical to supporting many functions of our economy. The pandemic has exposed a lot of those weaknesses. Many people are familiar with the executive order President Biden put out in February on American supply chains and highlighting the need for a resilient and diverse and secure supply chain to ensure both our economic prosperity and our national security. It's become front-and-center issue. There are many factors that can disrupt supply chains beyond a pandemic, such as threats from cyber attacks, extreme weather and geopolitical changes. So, there's a new emphasis on the ability for aerospace and defense companies to use these digital technologies to harden their supply chains and make sure that they are resilient and have multiple paths of execution.
For example, in aerospace, the supply chain supporting the fabrication of a flight-critical part is especially vulnerable to disruption since even minor changes can require a costly recertification effort. There needs to be fewer single points of failure in a supply chain, and we need to have both mitigation plans for those threats, which means minimizing the likelihood of a threat, having management plans on how to respond to a threat and knowing how quickly you can respond to restore the integrity of the supply chain.
AW: What should aerospace manufacturers seek from solutions providers to ensure they have the tools and systems in place for a truly unified digital thread?
Cordner: There has been a lot of emphasis on optimizing the way planning and execution on the shop floor interacts with engineering. We have developed a similar perspective to help aerospace companies look at how they can choose tools (MES and MOM) and create processes that also optimize interactions from the shop floor to their ERP systems. More and more aerospace and defense companies asking for help in this area because it doesn't do any good to strengthen one at the expense of the other. They need solutions providers who know how all enterprise systems work together, not just focus on one piece of the equation When we approach a company to help them understand what they need to do, from a digital transformation point of view, we're not dealing with just one particular area, we're dealing with the breadth of the value chain. Being a Model Based Enterprise takes a balanced approach that builds on the success of product modeling and matures into the balance of the value chain.
“According to a panel of A&D industry experts at the Frost & Sullivan Virtual Think Tank event, Industry 4.0 technologies can change the way industry designs, makes, sources, supplies, and services products. The future needs to be circular, integrated, and predictive."
Download the exclusive report to learn more: bit.ly/38Bl0ad