100 Top Technologies: 'Bonded Structures' to 'Automated Throttles'
Guy Norris Graham Warwick May 06, 2016
50. Redux Bonding
From the 1950s into the 1990s, and beginning with the de Havilland Comet in 1949, European commercial aircraft manufacturers made extensive use of bonded metal structures using Redux, a strong and durable adhesive invented in the U.K. in 1942.

51. Wiring Test System
At the end of many aircraft final assembly lines stands a DIT-MCO system used to test the continuity of wiring harnesses. DIT-MCO stands for the Drive-In Theater Manufacturing Co.—the technology has its origins in equipment used to test the audio systems at drive-in movies.

52. Engine Superalloys
Since the development of very-high-bypass turbofans and advanced two-spool military engines, manufacturers have largely focused on improving thermodynamic and propulsive efficiency by increasing pressure ratio, operating at higher temperatures and boosting airflow. Early Nimonic nickel-chrome alloys enabled higher turbine inlet temperature limits from the 1950s onward, but key advances starting in the 1980s began with the development of directionally solidified and single-crystal blades made from a new generation of nickel-based superalloys incorporating materials such as chromium, cobalt and rhenium.

53. GNSS
A pressing need for the U.S. military to know the position of its intercontinental ballistic missiles during the Cold War drove development of the greatest navigation renaissance since the invention of the chronometer—GPS. In order to hit a target, presumably in the Soviet Union, a ballistic missile guidance system would have to be programmed with a highly accurate starting point, a challenge for submarine-based launchers.
Earlier navigation systems, including space-based Transit in the 1960s and ground-based Omega in the ’70s had shortcomings. Transit, the first U.S. satellite-based navigation system, consisted of five satellites and would provide a navigation “fix” once per hour. Omega provided position fixes but with an accuracy of only 4 nm.
First proposed in the early ’70s, the Navstar (Navigation System Using Timing and Ranging) GPS constellation—with 24 satellites in medium-altitude circular orbits—would provide a worst-case position accuracy of 328 ft. horizontally for military users and 1,600 ft. for civilians. The system computed 3-D position based in part on the time required for signals to travel from at least four satellites to the GPS receiver. Other intended uses included land surveying for the U.S. Army, but few anticipated the myriad uses that would develop for GPS, including real-time navigation for aircraft, automobiles and boats as well as missiles and bombs.

54. Fly-by-Wire
Germany developed electronic active control for the A-4 rocket in World War II, and analog fly-by-wire (FBW)was used in the F-16 in 1974 and F-117 in 1981. In fly-by-wire, pilot inputs are transmitted to the flight controls via a computer, which can be programmed to keep the aircraft within its flight-envelope limits, improve handling and reduce workload.
The first aircraft to fly with digital fly-by-wire and no mechanical backup was NASA’s Vought F-8C testbed in 1972. The aircraft had two FBW systems, the primary based on the Apollo Guidance Computer.
The first commercial airliner with analog FBW was the Aerospatiale/BAC Concorde, while the first digital system entered service on the Airbus A320 in 1988.
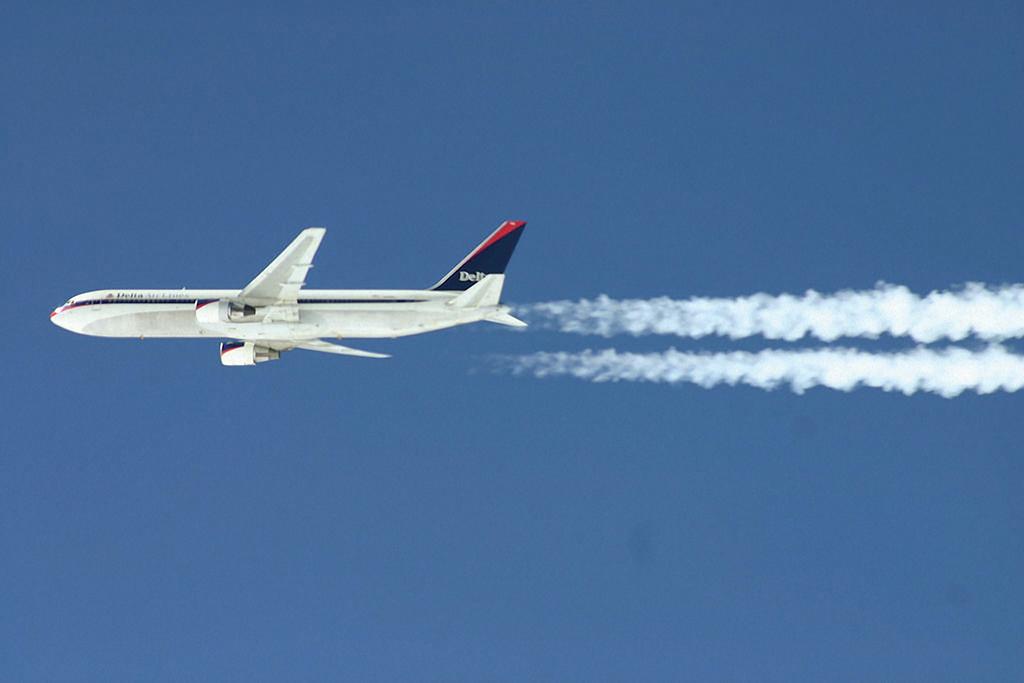
55. TCAS
A safety system that works to prevent mid-air collisions independently of air traffic control, TCAS (traffic alert and collision avoidance system) interrogates other aircraft equipped with an appropriate transponder. Based on the replies it receives, TCAS tracks the range, altitude and bearing of surrounding traffic and, by dividing range by closure rate, calculates the time to the closest point of approach. The system issues a traffic advisory alert first to assist the pilot in the visual search for the intruder and if the intruder gets closer a resolution advisory, which provides the pilot with recommended vertical speed or pitch angle to avoid an encounter.
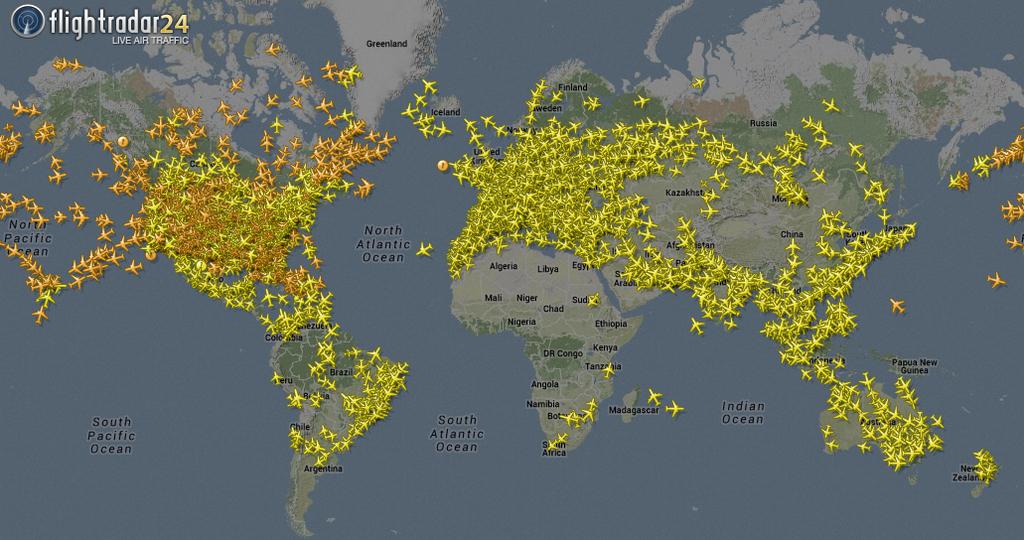
56. ADS-B
When Capt. Skip Nelson made the historic first Automatic Dependent Surveillance-Broadcast (ADS-B) flight in late 2000 under the FAA’s Capstone project, hope was high that the FAA was on the brink of a new surveillance paradigm that would wean air navigation service providers worldwide of costly ground-based radar and usher in the age of self-separation services. But 16 years later, that optimism, in the U.S. at least, is tempered with a certain amount of reality: ADS-B “Out” will replace only a limited number of radar systems, and the majority of aircraft are not yet equipped with 1090-MHz or 978-MHz transceivers that broadcast the aircraft’s GPS-based position and other information at 1-sec. intervals.
The equipment will be required to fly in most U.S.-controlled airspace as of Jan. 1, 2020. The mandate does not include the requirement to install the ADS-B “In” avionics that receive ADS-B data streams and could ultimately be used for self-separation and other high-value functions for airlines. A handful of carriers have equipped with ADS-B In but largely for FAA trial programs.
General aviation operators that have voluntarily equipped with 978-MHz ADS-B In—aka Universal Access Transceivers—are already benefiting from FAA-provided free weather and traffic information on the link. The FAA appears to be holding fast to the mandate, which will require a rapid increase in the number of installed ADS-B systems in the next four years if aircraft are to avoid being grounded.
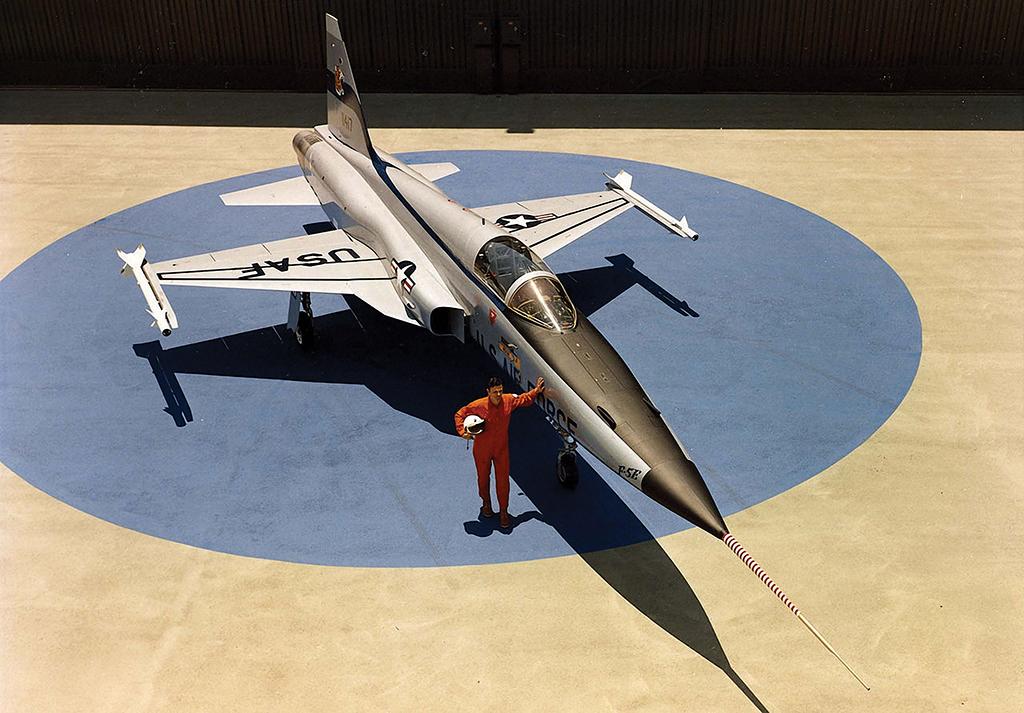
57. Transonic Area Rule
Efforts to develop supersonic aircraft in the late 1940s faced a sharp rise in drag (caused by shockwaves forming at transonic speed) approaching Mach 1 that jet engines were not powerful enough to overcome. NACA (National Advisory Committee for Aeronautics) aerodynamicist Richard Whitcomb realized the aircraft must be designed so the change in cross-sectional area from nose to tail was very smooth, avoiding a dramatic increase in area where the wing and tail met the fuselage—his transonic area rule. In 1954, transonic drag hobbled Convair’s YF-102. Rapidly redesigned with an area-ruled fuselage, YF-102A went supersonic on its first flight that December. The Northrop F-5’s elegant “coke bottle” fuselage (pictured) is an iconic use of area rule.

58. Countermeasures
Fielding of airborne radars in 1940 was quickly followed in 1942 by development of a countermeasure—reflective strips of aluminum codenamed “Window” in the U.K. and “Duppel” in Germany but now called chaff. Development of the Sidewinder in the early 1950s led to infrared decoy flares to test the heat-seeking air-to-air missile. Flares were deployed in the late 1960s to defeat the Soviet AA-2 missile.

59. GPWS/EGPWS
In April 1997, Aviation Week’s Laureate for Electronics was Honeywell engineer Don Bateman, who led development of the Enhanced Ground Proximity Warning System (EGPWS). The system uses an aircraft’s position and onboard terrain databases to alert pilots to terrain in the path ahead as well as to excessive rate of descent, excessive closure rate with terrain, flight into terrain when not in landing configuration, and other potentially fatal pitfalls. GPWS had only a look-down capability.

60. Computer-Aided Design and Manufacturing
First developed in the 1960s, computer-aided design (CAD) has become the backbone of the aerospace industry. McDonnell Aircraft began using computers to help layout designs in 1959 and went on to develop the Unigraphics CAD system, now owned by Siemens. Lockheed developed Cadam, later sold to IBM and then to Dassault Systemes, which developed Catia in the late 1970s. Boeing selected Catia in 1984 and says its 777 was the first aircraft to be designed entirely on computer.

61. Radioisotopic Thermal Generators
Spacecraft need electrical power. Batteries, fuel cells and solar arrays all have limitations—especially for missions of long duration or those far away from the Sun. Enter RTGs—radioisotope thermoelectric generators—developed by the U.S. Atomic Energy Commission in the 1950s.
RTGs convert the heat released in the decay of radioactive material, such as plutonium, into electricity. The first RTG was launched into space in 1961. Since then, they have been used to power many important planetary spacecraft such as Pioneer 10 and 11, Voyager 1 and 2, Galileo, Ulysses, Cassini and, most recently, New Horizons, which visited Pluto.

62. Carbon-Fiber Composites
High-performance carbon fibers were first created from rayon in 1958 at Union Carbide, followed by an improved fiber that was developed in
Japan using polyacrylonitrile, or PAN, the raw material used today. In 1963, the U.K.’s Royal Aircraft Establishment Farnborough developed a high-strength carbon fiber, Hyfil, that was licensed to Rolls-Royce. The engine maker used the lightweight material in the fan blades of the RB.211 high-bypass turbofan powering Lockheed’s L-1011 TriStar. But in 1970, the composite fan failed bird-strike testing, forcing a switch to titanium and extra costs that pushed Rolls into receivership.
While the U.K. developed carbon fiber, the U.S. pursued boron fiber, which was stronger and stiffer. Boron-fiber composites were used in the horizontal stabilizer of the Grumman F-14 in 1974 and horizontal and vertical tails of the McDonnell Douglas (MDC, now Boeing) F-15 in 1976. But boron fiber was expensive, and the U.S. moved to carbon-fiber composite for wing skins on the MDC AV-8B (pictured) and F/A-18, and in 1989 the Northrop B-2 and airframe of the Bell Boeing V-22 tiltorotor.

63. Computational Fluid Dynamics
Computational fluid dynamics (CFD)—the numerical simulation of fluid flows—has become an essential design, analysis and optimization tool for the aerospace industry. Aircraft manufacturers and NASA began developing and using two-dimensional CFD codes in the late 1960s. Use of computers to model three-dimensional flows began at Los Alamos National Laboratory around 1960. Advances in CFD were paced by the development of supercomputers, beginning with Control Data’s 1-megaflop CDC6600 in 1970. Finite element modeling for computational analysis in structures began around the same time.


65. Cooled Turbine Blades
Various methods have been devised to protect turbine blades from extremely high temperatures. The attempts range from thermal barrier coatings made from aluminide and ceramics to a variety of cooling methods that work by pumping cooler air from the compressor into hollow passages inside the blade. Cooling is provided by several means including internally by convection or impingement, or externally by film cooling, effusion or transpiration.

66. Enhanced & Synthetic Vision
Like peanut butter and chocolate, two disparate vision technologies—developed for different reasons and used independently—will arguably be better when joined together in the near future. So-called combined vision systems will fuse database-generated synthetic vision with sensor-based enhanced flight vision systems (EFVS), giving pilots an intuitive 3-D view of the airport environment from afar (using synthetic vision) and an actual view (with the sensors) up close.
The FAA first approved EFVS on a head-up display as a substitute for natural vision down to 100 ft. above the ground in 2001; synthetic vision systems were first approved by the agency for situational awareness purposes in 2006.

67. Head-Up Display
In June 1966, Aviation Week predicted “wide use” of new avionics capabilities installed on the General Dynamics F-111A as part of the Mark II avionics upgrade.
One capability was the head-up display (HUD), a transparent combiner that blends key flight parameters and forward-looking infrared imagery in monochrome with the information already in the pilot’s line of sight through the windscreen, a blending that safety advocates say gives pilots superior situational awareness.
The devices have made measured progress in commercial aviation; some newer aircraft models, including Boeing 787s, come standard with HUDs for both pilots.
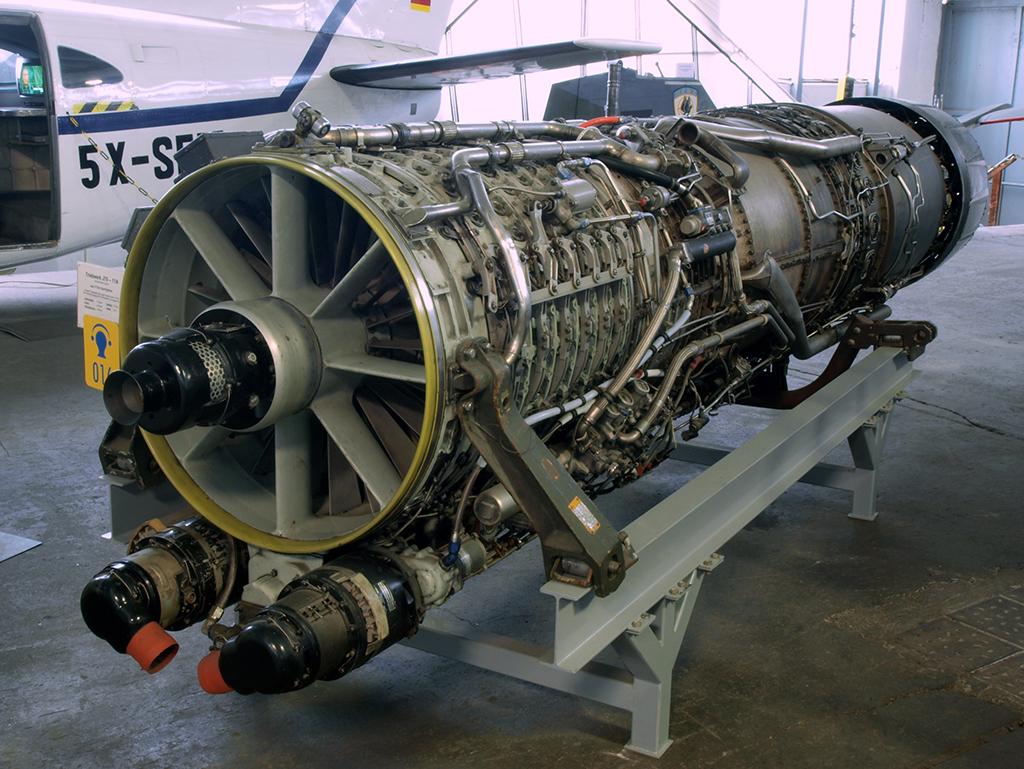
68. Variable-Geometry Stators
Early high-pressure-ratio engines suffered compressor stall and other operating problems at low speeds, particularly during acceleration. Dual spools and interstage compressor bleeding helped offset stalls, but the best solution was found to be variable stators, an automatic system that altered the angle of moveable inlet guide vanes and compressor stators as engine speed rose.
The device changed the angle of attack in the front stages to give rapid and stall-free acceleration, and also improved fuel burn.

69. Variable Inlets and Nozzles
Inlets are sized to deliver the correct mass flow of air to the compressor of the engine at a design point based on the cruise speed. However, in supersonic flight the air is compressed by a wedge in a rectangular inlet or a spiked center-body in an axisymmetric inlet, and shockwaves are formed at the intake lip. As the Mach number changes, the angle of the shockwaves entering the engine can be optimized by varying the position of the wedge or spike accordingly.
Similarly, to optimize engine performance over a wide range of airspeeds, high-speed aircraft have variable nozzles that converge for subsonic flight and diverge for supersonic flight. These “con-di” nozzles converge to accelerate the exhaust through a change of airspeed less than Mach 1 at subsonic speeds and diverge to enable expansion of the exhaust to optimize propulsive efficiency at speeds in excess of Mach 1.

70. Thrust Vectoring
Aircraft rely on powered lift to augment aerodynamic lift to achieve short or vertical takeoffs. Of many options studied, the most successful and practical approach has been vectored thrust, in which the power from a turbofan is turned through nozzle vanes to provide direct lift or to propel the aircraft forward in conventional flight.
This concept, adopted by the U.K.-developed Harrier, has been taken to the next stage by the Lockheed Martin F-35B (pictured), which augments direct lift from a vectoring aft nozzle with a shaft-driven fuselage-mounted lift fan.
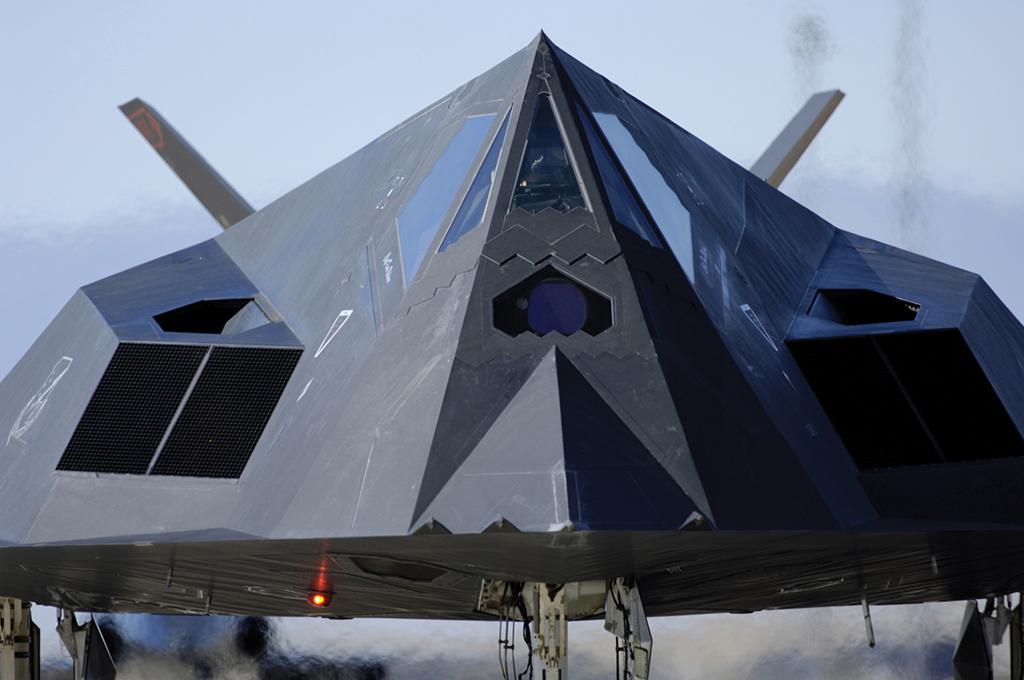
71. Stealth Technology
Efforts to reduce aircraft radar cross-section (RCS) to evade detection began in the 1950s. Lockheed’s A-12, first flown in 1962, was the first aircraft with reduced-RCS shaping (canted vertical tails and a chined body) and radar-absorbent material (RAM) built into the structure. In 1968, Teledyne Ryan flew the AQM-91 Compass Arrow unmanned, designed to survive by stealth alone.
After radar-guided surface-to-air missiles caused heavy losses in Vietnam in 1972 and the Middle East in 1973, Darpa called for a stealth demonstrator. Lockheed won the Have Blue contract in 1976, using a computer program that could predict the RCS of a shape made of flat facets and covered with sheets of RAM. The aircraft flew in 1977 and led to the F-117 (pictured), which became operational in 1983.
Northrop was chosen in 1976 to build an experimental reconnaissance aircraft, codenamed Tacit Blue, using curved profiles, and was the surprise winner of the Air Force competition to build the Advanced Technology Bomber, later named B-2, in 1981. In 1983, the Air Force revised its requirements for the Advanced Tactical Fighter to emphasize stealth, leading to the Lockheed F-22, flown in 1997.

72. Ramjet Engine
The ramjet, theoretically the simplest form of air-breathing engine, consists of a duct in which compression, combustion and expansion through a nozzle take place without any moving parts. Named for the ram effect of the incoming air into the inlet, the ramjet cannot be started from rest and is sometimes combined with a turbojet to bring it to operational speed. One such application was Pratt & Whitney’s J58 turboramjet in Lockheed’s SR-71 spy plane.

73. Carbon Brakes
Lighter, more efficient and offering higher performance than steel brake discs on earlier generations of aircraft, the carbon brake has become increasingly prolific since its early use on military aircraft and commercial introduction on an Airbus A310 in 1986.
The brakes consist of carbon-carbon, a pure form of carbon with a high friction coefficient that readily absorbs the high kinetic energy after landing. During flight tests of the A380, an aircraft weighing 1.27 million lb. was accelerated to 167 kt. before being brought to a halt using the carbon brakes alone.
In the final test, 16 brake-fitted main wheels (out of 20) each successfully absorbed 120 megajoules of energy.


75. Autothrottle
The autothrottle, a high-tech speed control for an aircraft, first emerged in the mid- to late-1960s, along the lines of a patent issued to LTV (Vought) Aerospace in 1968. The patent called for a “speed-sensing autothrottle” that included a “means for compensating for changes in attitude and for preventing stalling during banking of the aircraft.”
Some of the earliest mentions in Aviation Week are reports in 1965 regarding an autothrottle for the C-5A Galaxy, Concorde and Boeing 727 and 737, as a possible requirement for low-visibility landings.
Now commonplace on most commercial, business and even some general aviation aircraft, autothrottles are highly integrated with flight control systems, so much so that pilots can sometimes mismanage the many operational modes, a causal factor in the July 2013 crash of an Asiana Airlines Boeing 777 at San Francisco.
Two technology thrusts that continue to reshape aerospace—materials and computers—began to have a major impact in the 1950s and '60s. Computer-aided design became crucial as airframes moved from bonded-metal structures to carbon-fiber composites. Computational fluid dynamics became the key to advances in aerodynamics. Computer power was the secret to designing for stealth and making the resulting aircraft controllable with fly-by-wire. Through satellite navigation, head-up displays, enhanced vision, terrain databases, even autothrottles, onboard electronics and software made aircraft safer.
100 Top Technologies: 'Protecting the Pilot' to 'Keeping it Together'
100 Top Technologies: 'Aerodynamic Experiments' to 'Modern Monoplanes'
100 Top Technologies: 'Tipping the Wing' to 'Printing the Future'
Check 6 Listen as Aviation Week editors discuss—and debate—why they chose the aviation technologies and innovations featured here. AviationWeek.com/podcast

See more content from the 100th anniversary issue of Aviation Week & Space Technology