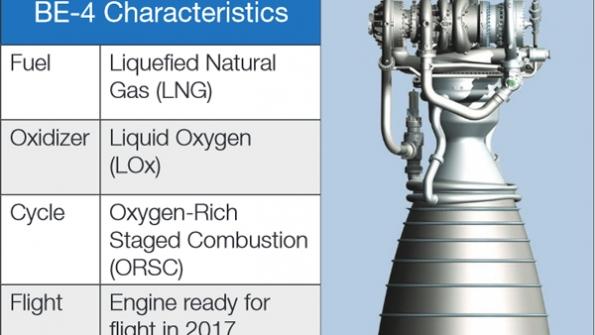
Credit: Blue Origin
COLORADO SPRINGS — United Launch Alliance CEO Tory Bruno says his choice of planning to reuse only the BE-4 engines – not the entire first stage – of the company’s new Vulcan rocket was driven purely by the economics. The cost equation also favors the Blue Origin BE-4 engine, he says, because it...
Subscription Required
This content requires a subscription to one of the Aviation Week Intelligence Network (AWIN) bundles.
Schedule a demo today to find out how you can access this content and similar content related to your area of the global aviation industry.
Already an AWIN subscriber? Login
Did you know? Aviation Week has won top honors multiple times in the Jesse H. Neal National Business Journalism Awards, the business-to-business media equivalent of the Pulitzer Prizes.