Space-Component Manufacturers Turn To 3-D Printing
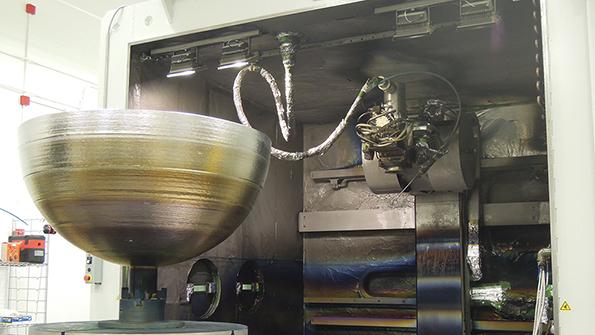
Credit: Frank Morring, Jr./AW&ST
COLORADO SPRINGS—Peter Beck flew here from New Zealand with a rocket engine in his luggage. The tiny powerplant, dubbed Rutherford, drew a lot of interest at the annual Space Symposium with its battery-powered turbomachinery. More to the point was the low launch cost—less than $5 million to orbit...
Subscription Required
This content requires a subscription to one of the Aviation Week Intelligence Network (AWIN) bundles.
Schedule a demo today to find out how you can access this content and similar content related to your area of the global aviation industry.
Already an AWIN subscriber? Login
Did you know? Aviation Week has won top honors multiple times in the Jesse H. Neal National Business Journalism Awards, the business-to-business media equivalent of the Pulitzer Prizes.