Checklists and Callouts: Keep It Simple, Avoid Distraction, Prevent Ineptitude
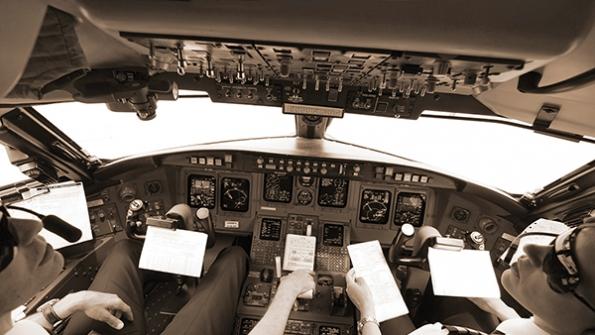
Credit: iStock
The first three decades of powered flight produced an explosive growth in the capabilities and complexities of aircraft. This became all too apparent on the afternoon of Oct. 30, 1935, when Maj. Ployer Hill, chief of the U.S. Army Air Corp’s flying branch, belted into the left seat of the Boeing...
Subscription Required
This content requires a subscription to one of the Aviation Week Intelligence Network (AWIN) bundles.
Schedule a demo today to find out how you can access this content and similar content related to your area of the global aviation industry.
Already an AWIN subscriber? Login
Did you know? Aviation Week has won top honors multiple times in the Jesse H. Neal National Business Journalism Awards, the business-to-business media equivalent of the Pulitzer Prizes.