Smallsats Growing In Utility
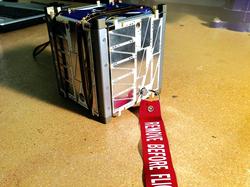
Credit: NASA Ames Research Center
Small satellites, once the realm of one-off low-budget science missions and undergraduate engineering classes, have come full circle with the growing realization among hard-pressed, high-end users that the little birds can do the big jobs, too. The smallest of them—cubesats—are rapidly evolving into...
Subscription Required
This content requires a subscription to one of the Aviation Week Intelligence Network (AWIN) bundles.
Schedule a demo today to find out how you can access this content and similar content related to your area of the global aviation industry.
Already an AWIN subscriber? Login
Did you know? Aviation Week has won top honors multiple times in the Jesse H. Neal National Business Journalism Awards, the business-to-business media equivalent of the Pulitzer Prizes.