Scaled And Virgin Lift Veil On Spaceship Production Progress
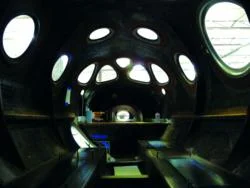
Credit: Christine Choi/Virgin Group
Shimmering, mirage-like, in the heat of California's Mojave Desert, the newly completed steel and concrete of the world's first commercial suborbital spaceship factory proves the goal of space tourism is nearing fruition. Located across the flightline from Scaled Composites at Mojave Air & Space...
Subscription Required
This content requires a subscription to one of the Aviation Week Intelligence Network (AWIN) bundles.
Schedule a demo today to find out how you can access this content and similar content related to your area of the global aviation industry.
Already an AWIN subscriber? Login
Did you know? Aviation Week has won top honors multiple times in the Jesse H. Neal National Business Journalism Awards, the business-to-business media equivalent of the Pulitzer Prizes.