NASA, Boeing Test Low-Drag Truss-Braced Wing Concept
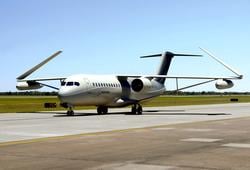
Tap the icon in the digital edition of AW&ST for a look at the history of the truss-braced wing, or go to AviationWeek.com/truss Look at any sailplane and it is clear—long, thin wings make flying more efficient. But sailplanes are light and slow; for heavier, faster airliners, there is a limit...
Subscription Required
This content requires a subscription to one of the Aviation Week Intelligence Network (AWIN) bundles.
Schedule a demo today to find out how you can access this content and similar content related to your area of the global aviation industry.
Already an AWIN subscriber? Login
Did you know? Aviation Week has won top honors multiple times in the Jesse H. Neal National Business Journalism Awards, the business-to-business media equivalent of the Pulitzer Prizes.