Mexico’s Welcome Mat Attracts Aerospace Manufacturers
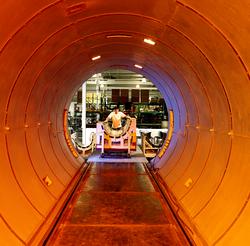
Credit: Nordam
In the past decade, Mexico's welcome mat for the aerospace establishment has found an industry eager to manufacture “south of the border.” The obvious attraction is Mexico's lower wage-structure: some say that in Mexico manufacturers pay a tenth of what equivalent assembly jobs cost in the U.S...
Subscription Required
This content requires a subscription to one of the Aviation Week Intelligence Network (AWIN) bundles.
Schedule a demo today to find out how you can access this content and similar content related to your area of the global aviation industry.
Already an AWIN subscriber? Login
Did you know? Aviation Week has won top honors multiple times in the Jesse H. Neal National Business Journalism Awards, the business-to-business media equivalent of the Pulitzer Prizes.