Lockheed, Pentagon Address F-35B Bulkhead Cracks
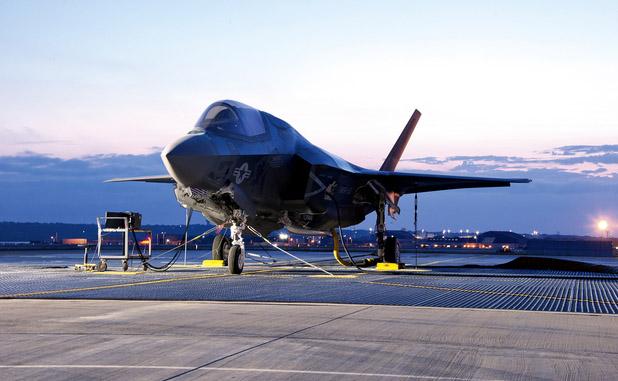
Credit: Lockheed Martin
Lockheed Martin is designing a fix to address cracks found in one of four primary wing carry-through bulkheads on an F-35B ground-test article that was undergoing durability tests for a second life of service beyond 8,000 flying hours. The suspect bulkhead is the same structure found in 2010 to have...
Subscription Required
This content requires a subscription to one of the Aviation Week Intelligence Network (AWIN) bundles.
Schedule a demo today to find out how you can access this content and similar content related to your area of the global aviation industry.
Already an AWIN subscriber? Login
Did you know? Aviation Week has won top honors multiple times in the Jesse H. Neal National Business Journalism Awards, the business-to-business media equivalent of the Pulitzer Prizes.