Full-Stall Simulators Take Shape
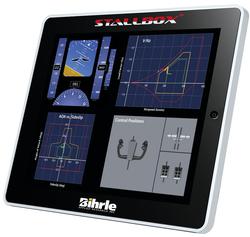
Credit: Bihrle Applied Research
It will be summer before an FAA preliminary rule to upgrade full-motion simulators with extended models to handle full stall training hits the streets, and nearly five years before airlines have to officially put the updated machines to work. Despite the long grace period, the industry is taking a...
Subscription Required
This content requires a subscription to one of the Aviation Week Intelligence Network (AWIN) bundles.
Schedule a demo today to find out how you can access this content and similar content related to your area of the global aviation industry.
Already an AWIN subscriber? Login
Did you know? Aviation Week has won top honors multiple times in the Jesse H. Neal National Business Journalism Awards, the business-to-business media equivalent of the Pulitzer Prizes.