Flying The Gulfstream G280
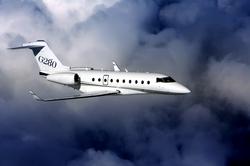
Credit: Gulfstream Aerospace
Gulfstream Aerospace soon will begin customer deliveries of its $24-million G280, a 3,600-nm-range super midsize jet. Although not new to the category—Gulfstream acquired the Galaxy (nee Israel Aerospace Astra IV) in 2001 and renamed it—the G200's performance was inferior to Bombardier's muscular...
Subscription Required
This content requires a subscription to one of the Aviation Week Intelligence Network (AWIN) bundles.
Schedule a demo today to find out how you can access this content and similar content related to your area of the global aviation industry.
Already an AWIN subscriber? Login
Did you know? Aviation Week has won top honors multiple times in the Jesse H. Neal National Business Journalism Awards, the business-to-business media equivalent of the Pulitzer Prizes.