‘Flying’ The Centaur Optionally Piloted Aircraft
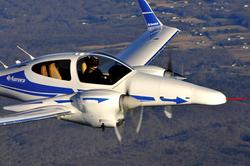
Aurora Flight Sciences is raising the stakes in airborne intelligence surveillance reconnaissance (ISR) platforms by lowering costs and increasing operational flexibility. The Manassas-based company's $4.5-million Centaur OPA, short for Optionally Piloted Aircraft, can perform most of the ISR...
Subscription Required
This content requires a subscription to one of the Aviation Week Intelligence Network (AWIN) bundles.
Schedule a demo today to find out how you can access this content and similar content related to your area of the global aviation industry.
Already an AWIN subscriber? Login
Did you know? Aviation Week has won top honors multiple times in the Jesse H. Neal National Business Journalism Awards, the business-to-business media equivalent of the Pulitzer Prizes.