Dassault Unveils Falcon 5X
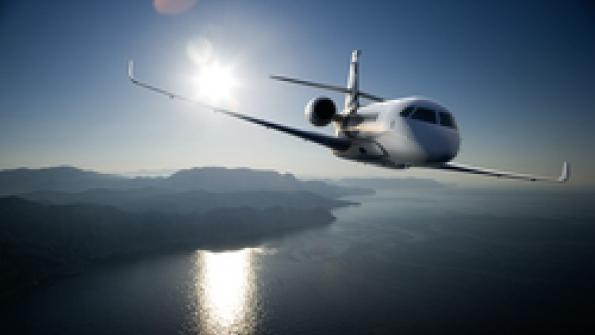
Credit: Dassault Falcon Jet
Bigger is better in the booming large-cabin business aircraft segment. Just look at the 200+ orders Gulfstream has for its G650 uber-jet, an aircraft with the largest cabin cross-section of any purpose-built jet in current production. Dassault Aviation, though, set an even larger cabin size standard...
Subscription Required
This content requires a subscription to one of the Aviation Week Intelligence Network (AWIN) bundles.
Schedule a demo today to find out how you can access this content and similar content related to your area of the global aviation industry.
Already an AWIN subscriber? Login
Did you know? Aviation Week has won top honors multiple times in the Jesse H. Neal National Business Journalism Awards, the business-to-business media equivalent of the Pulitzer Prizes.